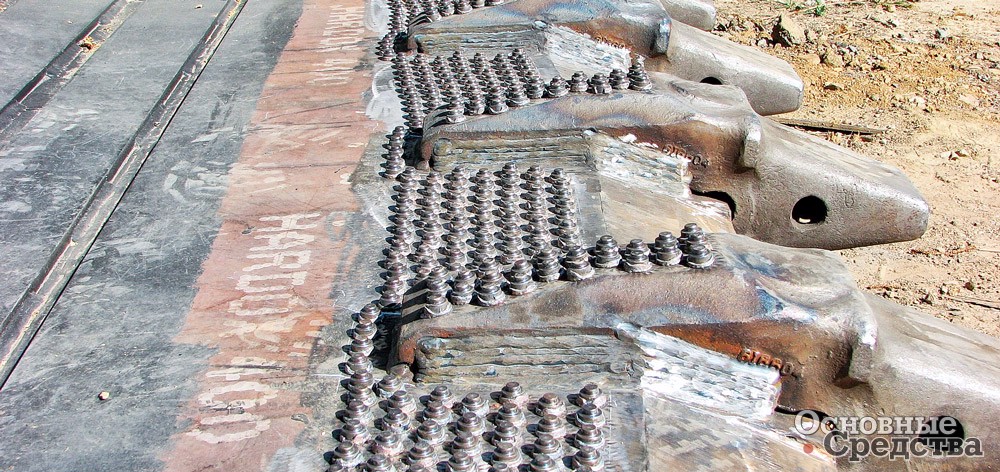
Наварка твердым сплавом поверхностей орудий землеройной техники
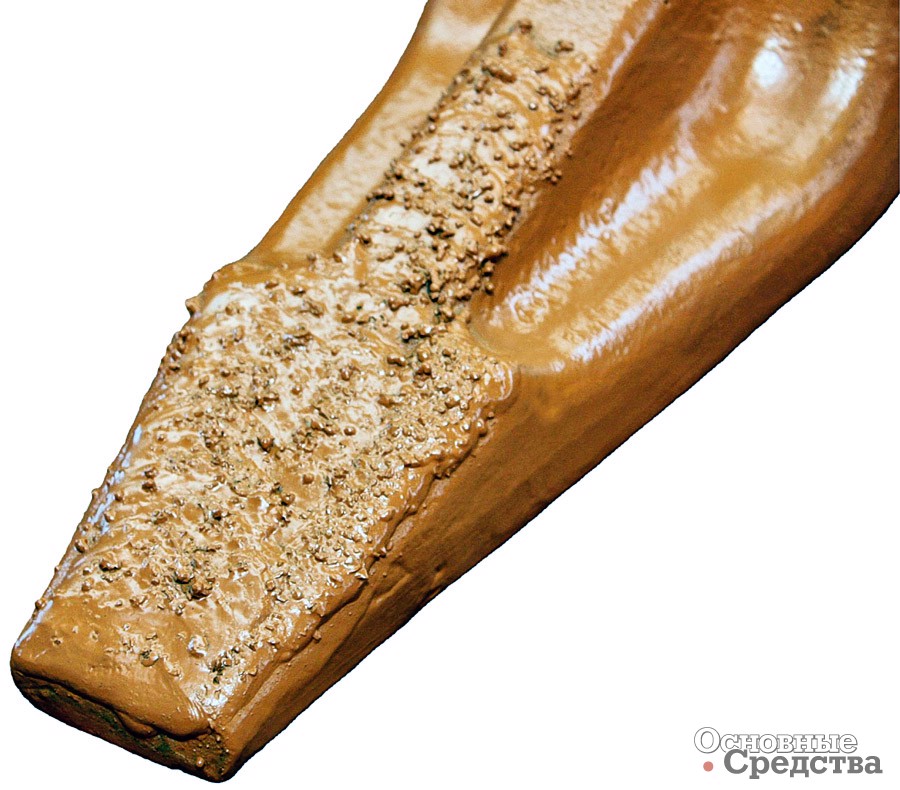
При работе с грунтом и другими материалами компоненты землеройных машин – ковши, зубья, отвалы, кромки бура, гидромолоты, гидроножницы и даже грунтозацепы гусеничных траков испытывают абразивные воздействия и изнашиваются. И здесь нет исключений: орудия даже самого малого размера подвержены износу такого рода.
Для восстановления и упрочнения зон, в которых в результате трения или ударов возникает абразивный износ (режущие кромки и рабочие поверхности), чтобы продлить срок службы землеройного оборудования, применяется наварка твердым сплавом, т. е. нанесение способом сварки нового, более прочного материала на изнашиваемую поверхность. Те части орудия, которые не подвергаются абразивному износу, в упрочнении не нуждаются. Для восстанавливаемой детали рекомендуется производить наварку твердым сплавом уже после восстановления первоначальных размеров детали обычным способом, чтобы дополнительно увеличить срок ее службы. Наварка твердым сплавом может использоваться и в качестве превентивной меры, например, если орудие выполнено из материала, недостаточно прочного для разработки скальной породы.
Другим способом увеличения срока службы ковша или режущего инструмента является наплавка готовых износостойких пластин из твердого сплава.
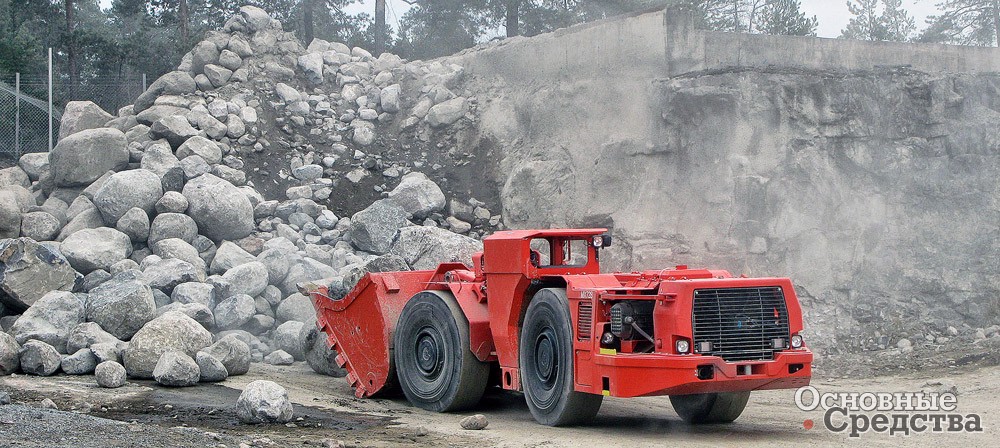
Подбор материалов для упрочняющего и буферного слоев
Многие совершают такую ошибку: используют для наварки нового орудия такие же электроды или проволоку, какие использовались ранее для наварки других орудий, или те, что привыкли использовать. Но это может оказаться совершенно неправильным – для наварки каждого орудия твердым сплавом следует специально подбирать материалы: проволоку или электроды. Основное требование при выборе присадочной проволоки: у нее должен быть максимально такой же химический состав, что и у свариваемых материалов. Конечно, при выборе твердых сплавов для наварки желательно следовать рекомендациям производителя орудия.
Углеродистые и низколегированные стали при упрочнении обычно наплавляют без предварительного нагрева, но они могут приобрести высокую хрупкость, и потребуется предварительная или завершающая термообработка для снятия внутренних напряжений, чтобы предотвратить возникновение трещин.
Аустенитные марганцевые стали должны свариваться без подогрева и последующей термообработки. При упрочнении в результате сварки они могут приобрести повышенную хрупкость. Во время упрочнения температура основного металла должна быть в диапазоне 10–260 °С, иначе хрупкость стали возрастет.
![Ковш экскаватора [b]до[/b] упрочнения твердосплавными пластинами](/article/16104-navarka-tverdym-splavom-poverhnostey-orudiy-zemleroynoy-tehniki-nesokrushimaya-zashchita/05a.jpg)
![Ковш экскаватора [b]после[/b] упрочнения твердосплавными пластинами](/article/16104-navarka-tverdym-splavom-poverhnostey-orudiy-zemleroynoy-tehniki-nesokrushimaya-zashchita/05b.jpg)
На практике отличить углеродистые и низколегированные стали от аустенитно-марганцовистых можно с помощью магнита: первые являются магнитными, вторые – не магнитны, однако после упрочнения аустенитно-марганцовистые стали также становятся магнитными.
Важно, чтобы твердый сплав наваривался в два (или три) слоя. При наплавке первого слоя металл основы расплавляется и смешивается с твердым сплавом. Второй (или третий) слой будет уже чисто твердосплавным, защищающим от абразивного износа. Если требуется наплавлять большую толщину, нижние слои наплавляются электродами из малоуглеродистой стали и лишь заключительные – твердосплавными.
При отсутствии ударных нагрузок упрочнение хрупкими высокоуглеродистыми твердыми сплавами, содержащими карбид или карбид с хромом, наилучшим образом защищает от износа. Наваривая слои, не стоит класть много слоев, особенно карбида хрома. Не рекомендуется делать слишком много проходов при наплавке твердосплавной проволокой, потому что это может увеличить склонность металла, находящегося внизу, к растрескиванию, т. к. сплав может быть хрупким.
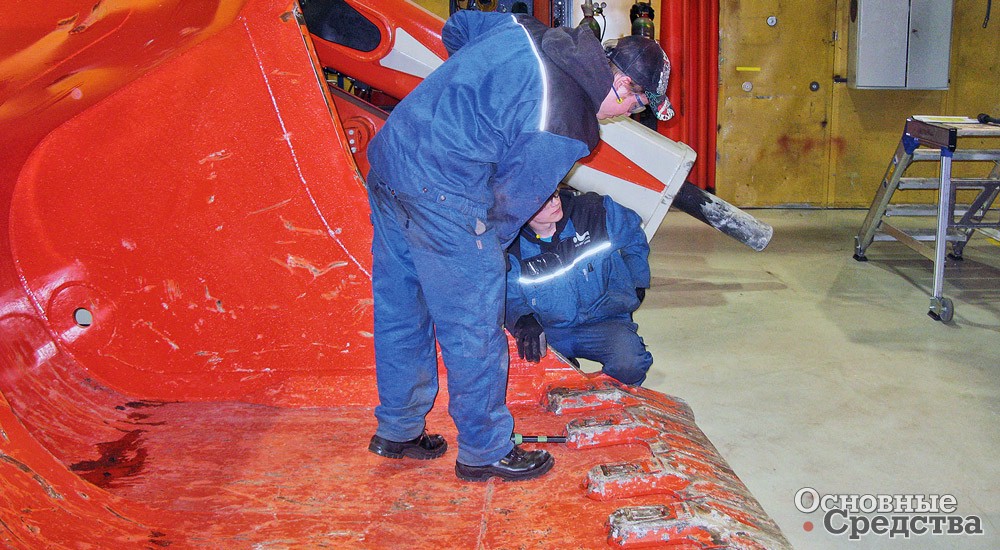
Поддерживающий слой используется не всегда. При наварке твердым сплавом ковшей его, как правило, используют, но при упрочнении зубьев орудий, применяемых для разработки горных пород, и других подобных деталей зачастую обходятся лишь одним твердосплавным слоем. Если же нужно максимально укрепить зубья, накладывают первый (буферный и соединительный) слой твердого металла, способного воспринимать высокие нагрузки, и уже на него наваривают твердый сплав. Рекомендуется использовать легированный металл для создания первого наплавного слоя. Это не обязательно должна быть малоуглеродистая сталь, обычно рекомендуется использовать для первого слоя более твердый сплав, но может быть, не такой твердый, как металл второго, защитного слоя. В процессе работы орудия верхний твердосплавный слой получает удары и деформируется, но слои, находящиеся ниже, также обладают достаточной прочностью и не деформируются, поддерживая верхний защитный слой и защищая металл основы. Зубья ковшей можно эксплуатировать сразу после наплавки, без обработки наплавленной поверхности.
Твердосплавные пластины рекомендуется приваривать пластичным сплавом, чтобы избежать растрескивания. При использовании для наварки твердого металла швы получаются хрупкими. Сварные швы из пластичного металла лучше выдерживают удары и менее подвержены растрескиванию.
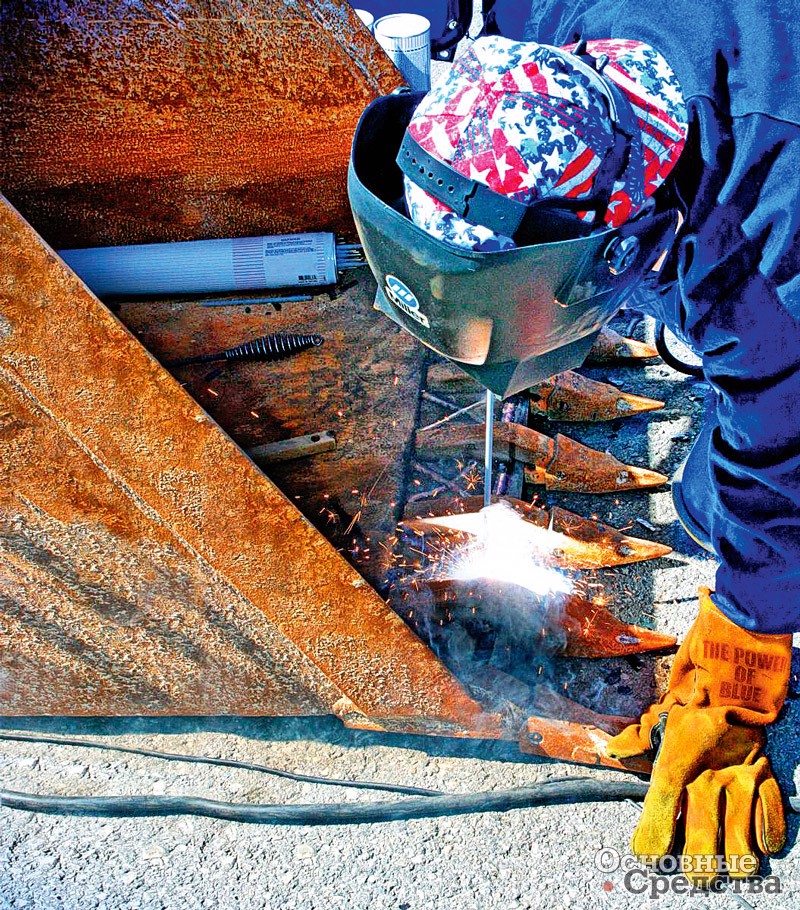
Технологии наварки
Оборудование и технологии, которые используются для упрочнения рабочих поверхностей орудий путем наварки твердым сплавом, могут быть различными в зависимости от условий работы (в мастерской или в «поле») и от того, из каких металлов изготовлены орудия. Для наварки обычно используются сварочные электроды с покрытием (ручная электродуговая сварка) либо сварка полуавтоматом цельностержневой либо порошковой проволокой в среде инертных (защитных) газов.
Оборудование для ручной наплавки электродом компактное и удобно для работ «в поле», на месте эксплуатации оборудования. Разработано много видов электродов, которые используются для наложения сварочных швов в любой плоскости. Но во время сварки электрод с покрытием сгорает не полностью. Если после работы взвесить все оставшиеся «огарки», будет видно, как много денег пропало впустую.
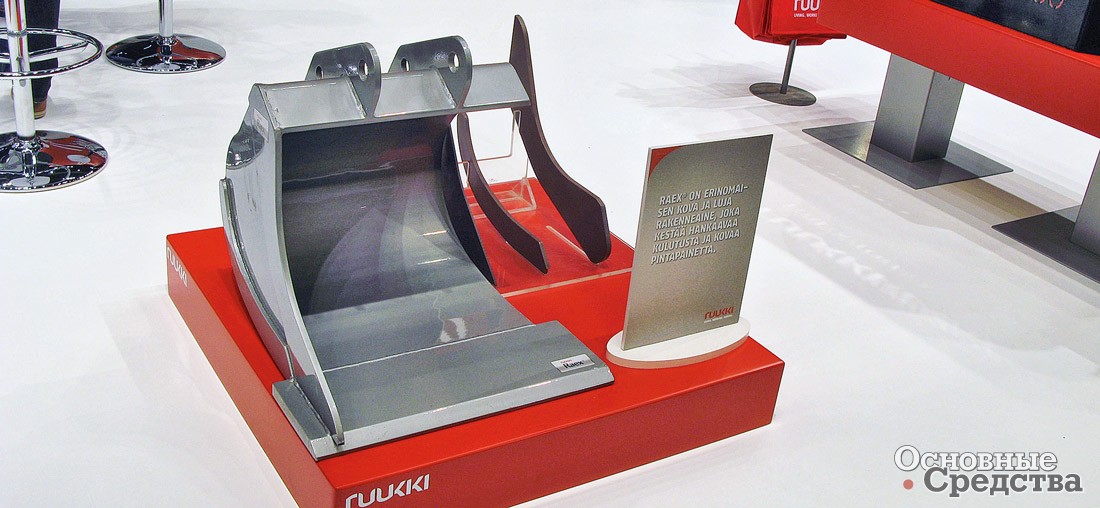
Часто предпочитают использовать сварку полуавтоматом с порошковой или цельностержневой проволокой, поскольку она дешевле и проще в использовании, требования к квалификации сварщика минимальные. К тому же при автоматической сварке производительность намного выше, работа выполняется быстрее. Для сварки порошковой проволокой не нужен газовый баллон, дуга почти не чувствительна к наличию ветра, может использоваться в полевых условиях благодаря возможности сварки открытой дугой. Но порошковая проволока стоит дорого, и имеет смысл ее использовать только в тех труднодоступных местах, куда сложно доставить баллон с газом. К тому же считается, что качество швов получается хуже, чем при сварке полуавтоматом цельностержневой проволокой в среде защитных газов. Существенный недостаток порошковых проволок, сдерживающий их широкое промышленное применение, – повышенная вероятность образования в швах пор, вызываемая наличием пустот в проволоке. Как уже упоминалось, недостатком сварки цельностержневой проволокой является необходимость доставлять на рабочее место кроме аппарата еще и баллон с газом и длинный газовый шланг, чего при работе в полевых условиях не всегда удается сделать. В поле удобнее производить наварку твердым сплавом, не применяя защитных газов, т. е. производить сварку открытой дугой. Известны разработанные некоторыми компаниями (например, Lincoln Electric Co.) сорта сварочной проволоки, которыми можно производить наварку твердым сплавом и в среде защитных газов, и без них.
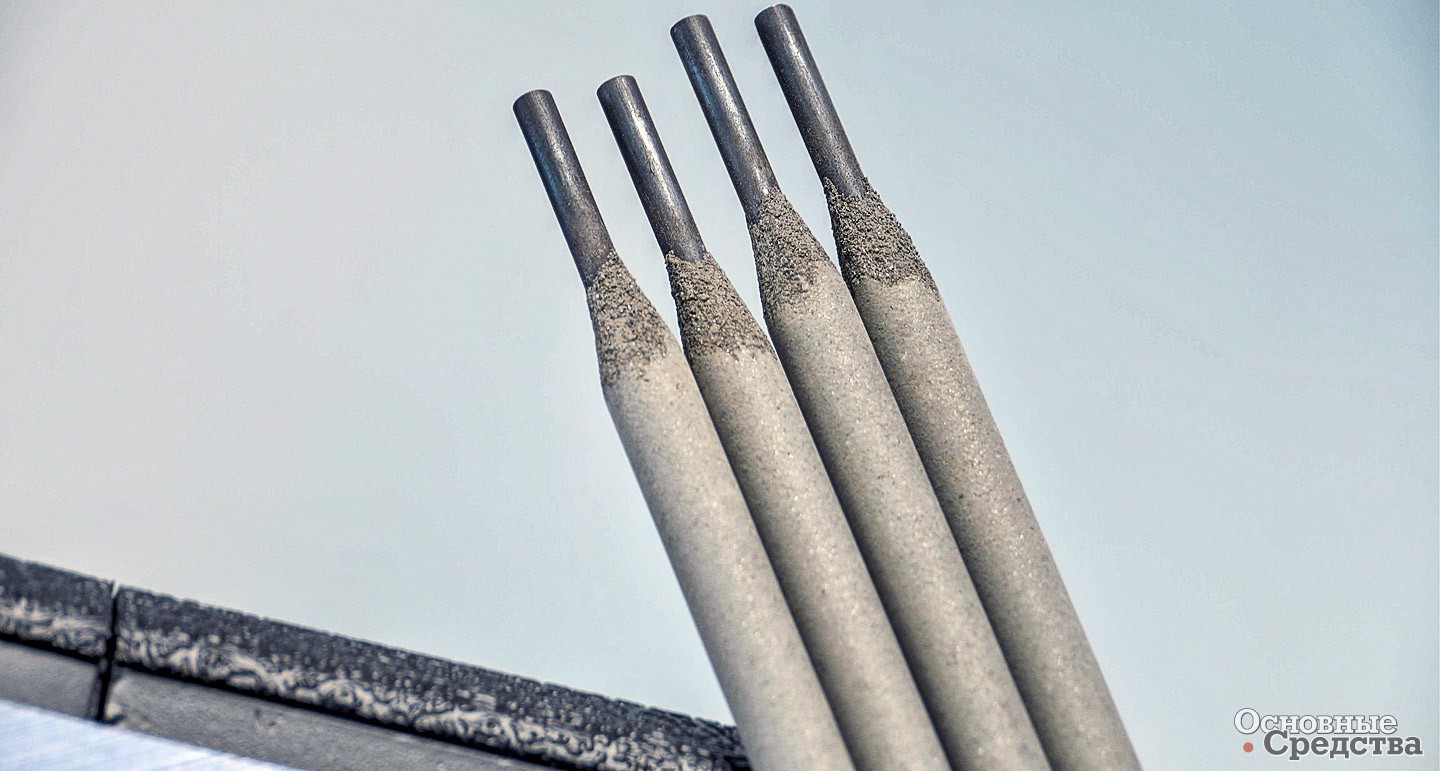
Если наварка твердым сплавом выполняется проволокой в среде инертных газов, рекомендуется выполнять работу в помещении (желательно небольшом), в котором можно было бы организовать эффективную вентиляцию и не допускать задымления. Работа в этом случае будет идти намного лучше, эффективнее работает система охлаждения сварочного пистолета, и токопроводящий наконечник (мундштук) прослужит дольше.
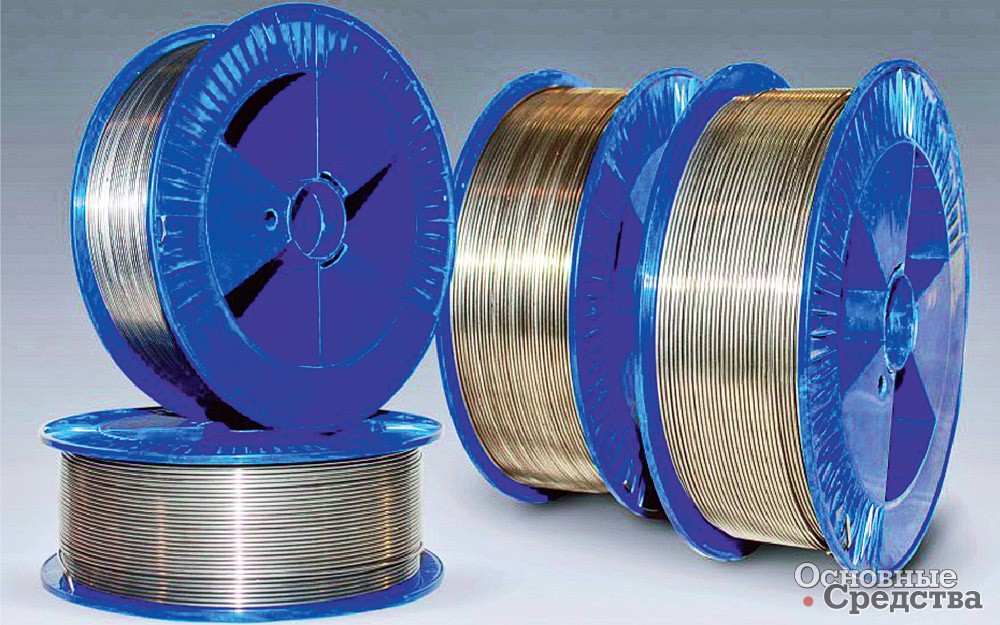
Усиливающие швы – квадратами и ромбами
Рабочие поверхности ковшей обычно защищают наварными швами-валиками высотой около 5 мм, пересекающимися в форме квадратов или ромбов. Нередко прямо на только что купленный дорогой ковш наносят «рисунок» из твердосплавных наварных швов. За счет неполного покрытия поверхности упрочнение получается дешевле. Специалисты считают, что обе формы рисунка одинаковы по функциональным качествам. Но общее правило таково: расстояние между параллельными швами должно составлять 40–45 мм, чтобы там задерживалась грязь. Во время работы твердосплавные наварные швы и грязь служат комплексной защитой металлу ковша, и срок его службы увеличивается.
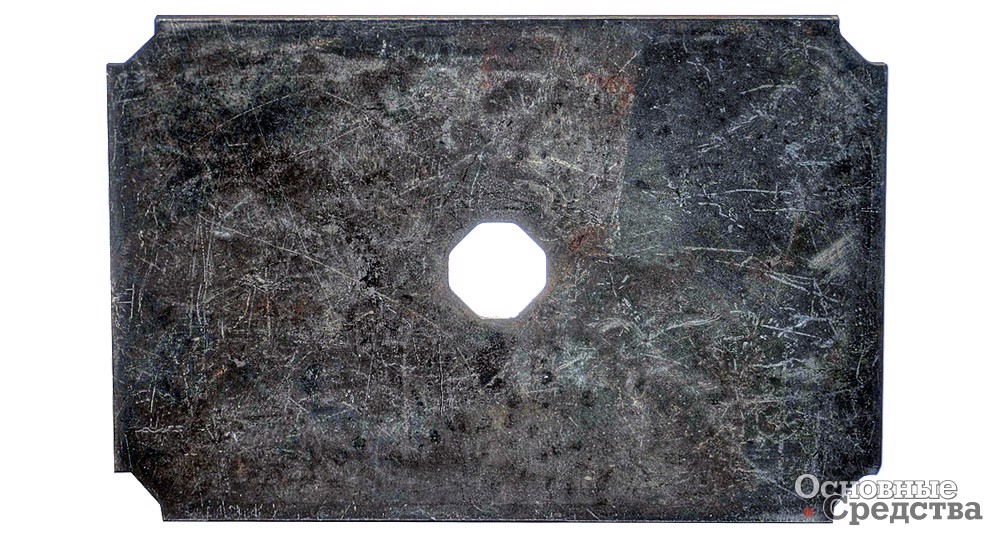
Форма рисунка, образуемого наварными швами, зависит от типа грунта и рабочего орудия. Например, при работе со скальными породами рекомендуется выбирать рисунок или наварные линии, расположенные параллельно направлению, по которому происходит изнашивание, то есть для защиты таких ковшей наваривают швы, вытянутые в направлении, по которому движется ковш. Если же ковш работает с песчаным грунтом или верхним слоем почвы, наварные швы обычно располагаются скорее в направлении, поперечном движению ковша, чтобы грунт лучше задерживался между валиками из твердосплавного металла. Если же ковш используется для работы с грунтами и скального, и песчано-почвенного типов, то рекомендуется использовать рисунок из перекрестных линий (ромбами) или в виде «ёлочки».
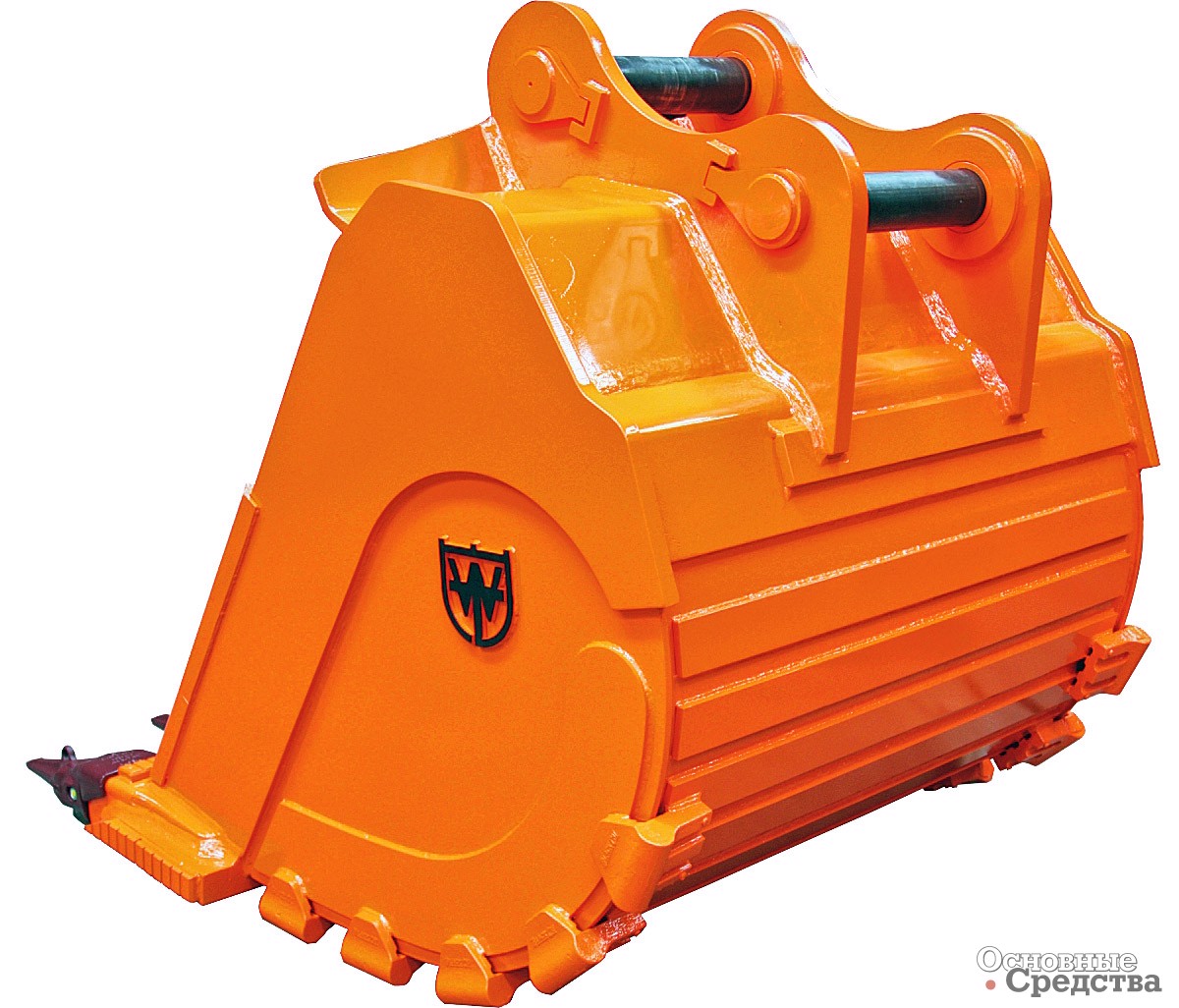
Техники, выполняющие эту работу, должны следить, чтобы точно соблюдались размеры «рисунка» и высота наваренного шва. Обычно при наварке твердым сплавом допускают две характерные ошибки. Во-первых, делают слишком крупные клетки или ромбы. Как правило, увеличивают расстояния между швами в целях экономии. Но в «клетках» или «ромбах» шириной 75–100 мм грязь почти не задерживается, и следовательно, никакой защиты металла от абразивного воздействия не получается. Во-вторых, при наварке устанавливают слишком большую величину силы тока или напряжения. В результате вместо валиков сварные швы получаются плоскими или даже образуются впадины. Рекомендуется выполнять наварку твердым сплавом при минимально возможной температуре металла, чтобы он разжижался как можно меньше, тогда швы будут получаться выпуклыми и хорошо задерживать «защитную» грязь на поверхности орудия.
Твердосплавные пластины, которые навариваются на землеройные орудия, также могут иметь, например, отверстия посередине, которые выполняют ту же роль, что и «сетка» из сварных швов – задерживают «защитную» грязь, предохраняющую металл пластины от контакта с грунтом, т. е. от износа.
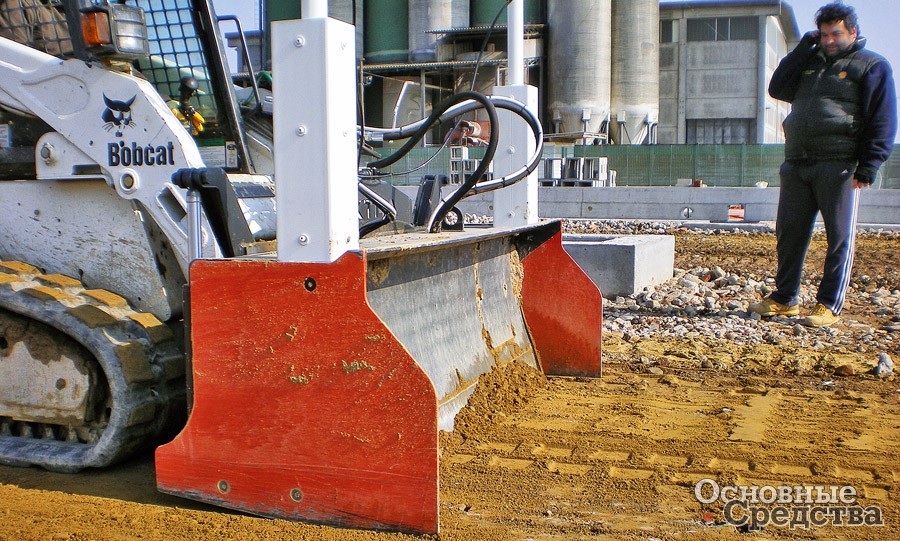
Экономический эффект
Упрочнение путем наварки твердым сплавом – отличное средство, позволяющее замедлять темп износа рабочих поверхностей орудия. Насколько увеличится ресурс землеройного орудия в результате наварки твердым сплавом, зависит прежде всего от условий его работы. В одной местности приходится работать с глинистым грунтом, в другой – с песчаным, а в третьей – со скалистым. Понятно, что износ орудия в каждом случае будет отличаться. В общем же можно сказать, что наварка твердым сплавом увеличивает срок службы землеройного орудия в 4–10 раз, а иногда и больше. При этом затраты на упрочнение оборудования путем наварки твердым сплавом составляют от 10 до 75% от стоимости нового орудия – это очень выгодная инвестиция.
Однако, принимая решение об использовании технологии упрочнения поверхностей, следует тщательно проанализировать экономическую сторону вопроса. Каков желательный срок службы орудия до износа? Может быть, его ресурса будет достаточно и без упрочнения? Сравните стоимость наплавки со стоимостью нового орудия. Имея необходимые исходные данные, можно подобрать оптимальные варианты упрочняющей наплавки по приемлемым ценам, т. к. из-за содержания в наплавочных материалах кобальта, вольфрама, молибдена, ниобия и других дорогих металлов стоимость расходных материалов для наплавки может быть очень высокой. Проанализируйте условия работы орудия: если условия работы таковы, что этот наваренный упрочняющий слой или упрочняющая пластина могут быть сколоты с поверхности орудия или поломаны, или оператор использует такие приемы работы, при которых преимущества упрочненной поверхности не используются в полной мере, затраты на упрочнение не окупятся с максимальным экономическим эффектом.
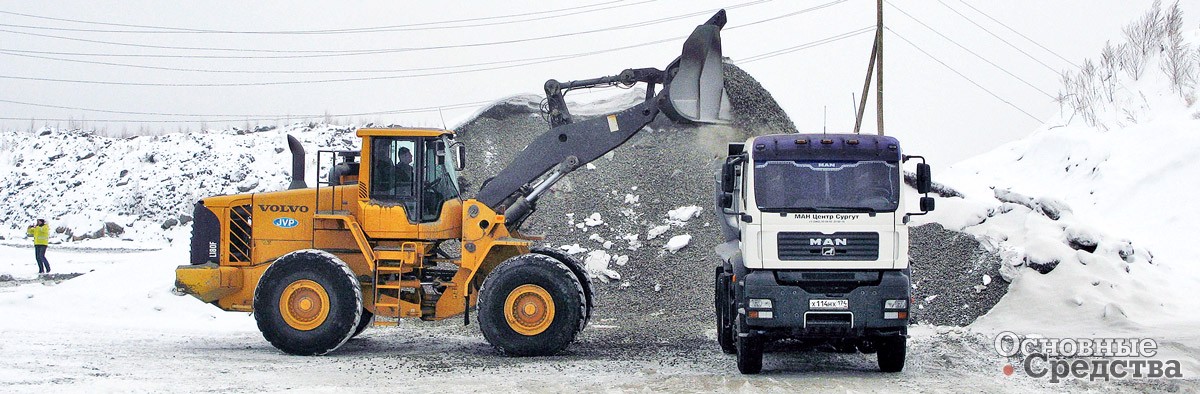
Сколько раз можно повторять наварку твердым сплавом одной и той же детали? По мнению ряда специалистов, возможное количество наварок зависит от того, какие сплавы для этого используются, но в общем случае, пока зуб (или иная деталь) не износится настолько, что упрочнение его потеряет всякий смысл, можно наваривать твердый сплав поверх изношенного. В эксплуатации еще можно встретить, например, бульдозеры, которые работают не один десяток лет, их отвалы восстанавливались наваркой много раз.
Дилеры некоторых ведущих мировых компаний предлагают клиентам услугу: проведение анализа износа деталей оборудования, для того чтобы помочь в принятии решения относительно использования технологии наварки твердым сплавом. Специалисты дилера анализируют характер износа рабочих поверхностей ковша или отвала при данных условиях работы, проводят измерения с помощью трехмерного сканирования, которое помогает точно воссоздать первоначальную геометрию рабочих поверхностей орудия, и помогают клиенту понять, стоит восстанавливать исходную форму рабочей поверхности орудия с помощью наварки твердым сплавом или лучше заменить деталь на новую.
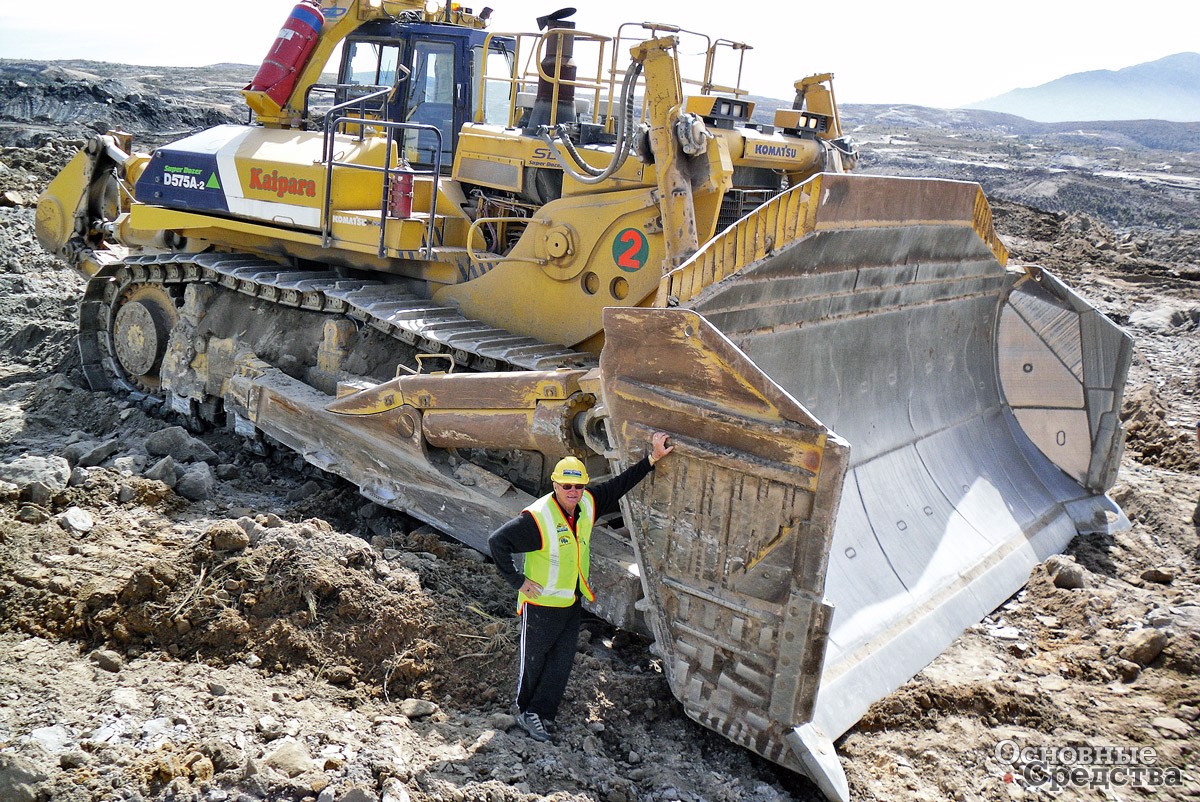