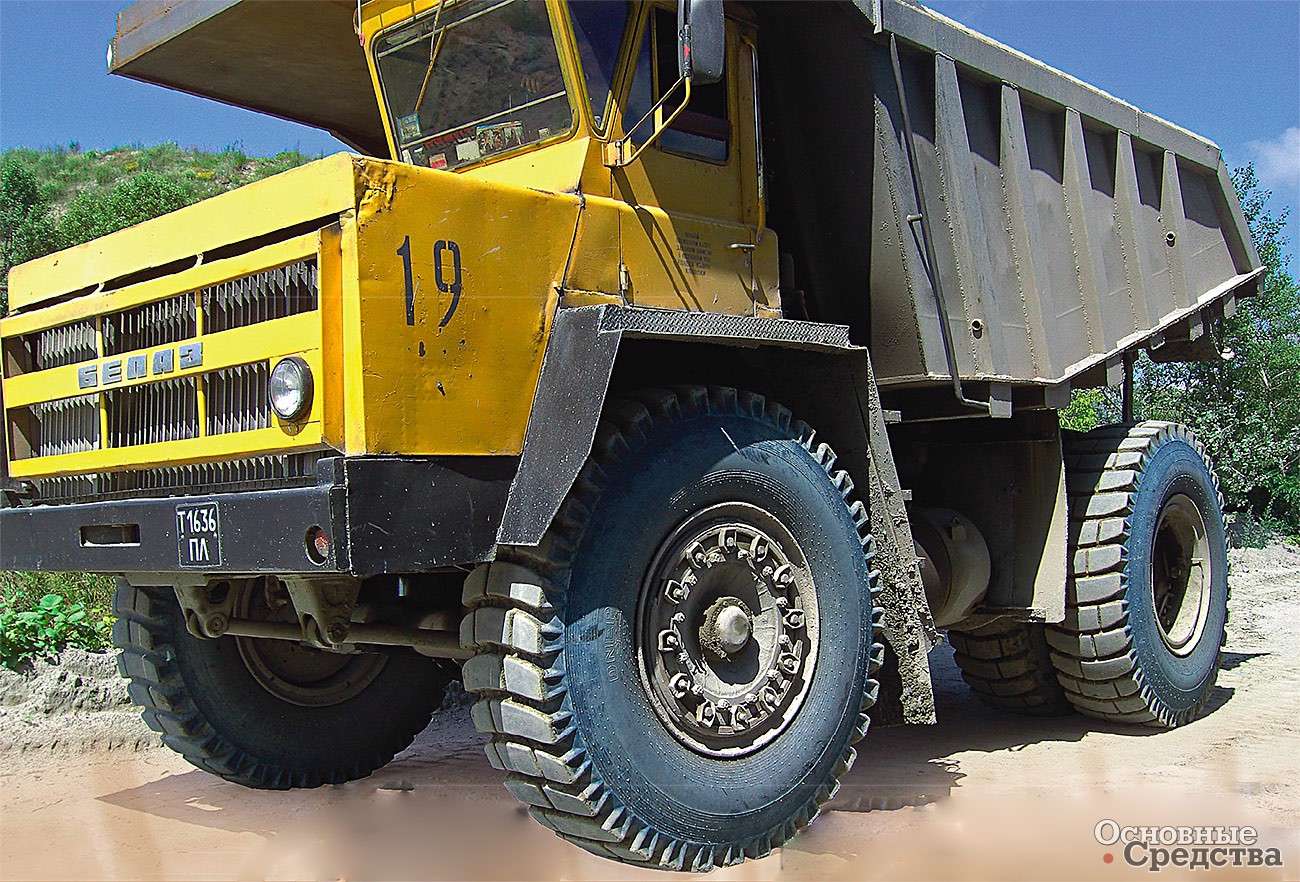
Жизнь после жизни
Восстановление и утилизация автомобильных шин
Рост парка автомобилей в индустриально развитых странах в последние годы в свою очередь означает, что растет и количество изношенных автошин. По данным Европейской Ассоциации по вторичной переработке шин (ЕТRА), общая масса изношенных, но непереработанных шин в России намного превышает 1 млн т. В странах СНГ сегодня накоплено более 50 млн. ед. изношенных шин.
Протектор износился. Что дальше?
Покрышки, непригодные для дальнейшей эксплуатации, являются долговременным источником загрязнения окружающей среды. Они не подвержены биологическому разложению, в местах их складирования создаются условия для обитания грызунов и насекомых. Покрышки пожароопасны, а продукты их неконтролируемого сжигания оказывают крайне негативное влияние на почву, воду, атмосферу. Из тонны сгоревших шин окружающая среда «получает» 270 кг сажи и 450 кг токсичных газов, таких как антрацен, флуорентан, пирен, а также бифенил и бенз(а)пирен, которые относятся к сильнейшим канцерогенам. Представители природоохранных организаций утверждают, что накопление изношенных шин вредит экологии, жизнедеятельности людей, причем речь идет не только о ныне живущих, но и о последующих поколениях.
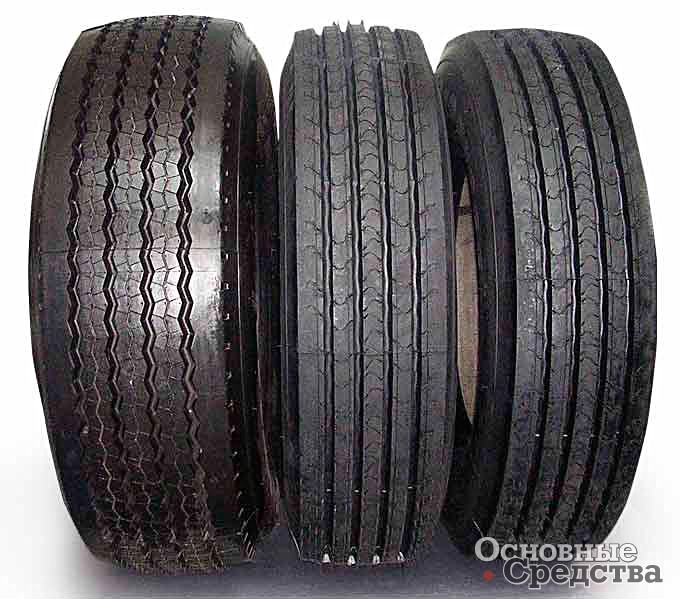
Сегодня самый распространенный метод утилизации шин – сжигание покрышек в цементных печах, что, однако, вовсе не означает, что это лучший метод. Теплотворная способность резины составляет 32 ГДж/т, и это соответствует углю высокого качества. Применение в данном производстве большого количества старых автошин негативно отражается на качестве цемента, так как содержащаяся в них сталь проявляется в цементе как оксид железа, который окрашивает материал. Метод также экономически нецелесообразен: уничтожаются содержащиеся в шине ценный каучук, металлокорд, текстильный корд.
Вторым по масштабам методом утилизации является переработка шин в резиновую крошку разных фракций. Потребности промышленности в этом виде сырья огромны, и спектр применения крошки очень широкий. Наиболее экономически обосновано использование крошки в качестве добавок в различные резиновые смеси, в том числе используемые при производстве новых шин. Резиновую крошку широко применяют в качестве модификатора битума в дорожном строительстве. Крошка различных фракций необходима при изготовлении резинобитумных мастик, кровельных материалов. Это сырье применяют для выпуска плит, используемых в самых разных сферах производства: настилы и полы для животноводческих ферм, резиновые плиты, укладываемые на трамвайных и железнодорожных переездах, полы в производственных и спортивных сооружениях, на детских игровых площадках. «Резиновые» порошки (размер частиц от 0,5 до 1,0 мм) используют и в качестве сорбента для сбора сырой нефти и жидких нефтепродуктов с поверхности воды и почвы.
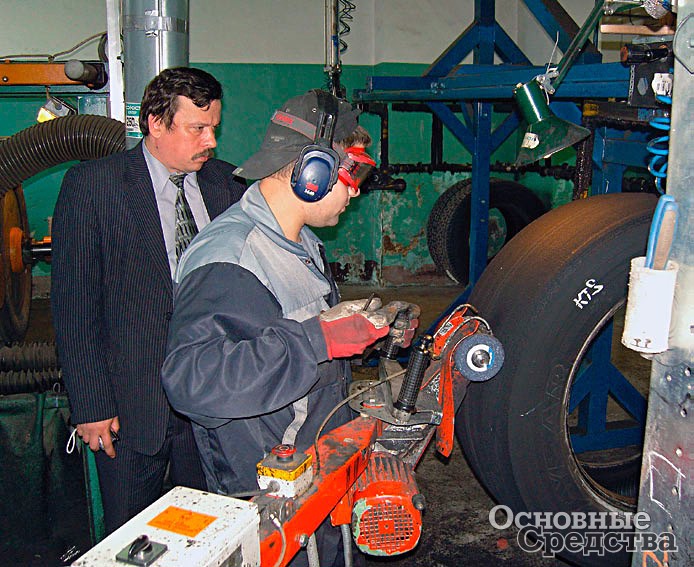
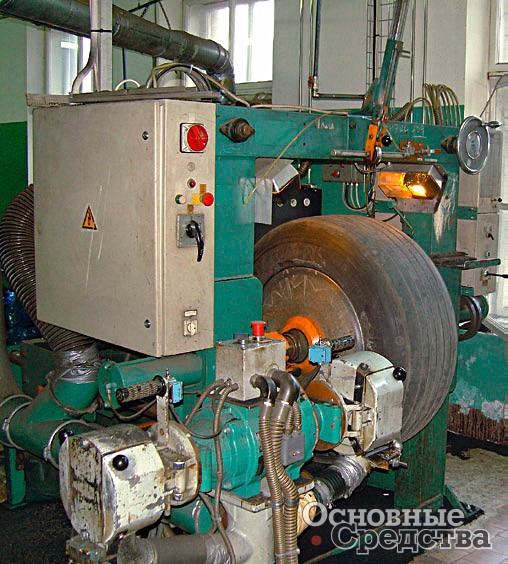
Основным препятствием для широкого внедрения этого вида переработки шин является сложность отделения резины от металлического и текстильного корда. В настоящее время существует около десятка технологий, облегчающих этот процесс, но все они в той или иной степени несовершенны, а потому вопрос оптимального способа утилизации остается сегодня открытым.
С точки зрения экологичности очень привлекателен водоструйный метод, когда струя воды под высоким давлением вырывает кусочки резины. Качество получаемого резинового порошка при этом высокое, но и энергозатраты немалые: на производство 1 кг порошка тратится 1 кВт.ч электроэнергии.
При бародеструкционном методе предварительно раздробленную на крупные куски покрышку загружают в специальную камеру, где под действием высокого давления и температуры резина отделяется от металлокорда, но, к сожалению, полной очистки металлокорда этот метод не дает: требуется дополнительная степень очистки, а это лишние затраты.
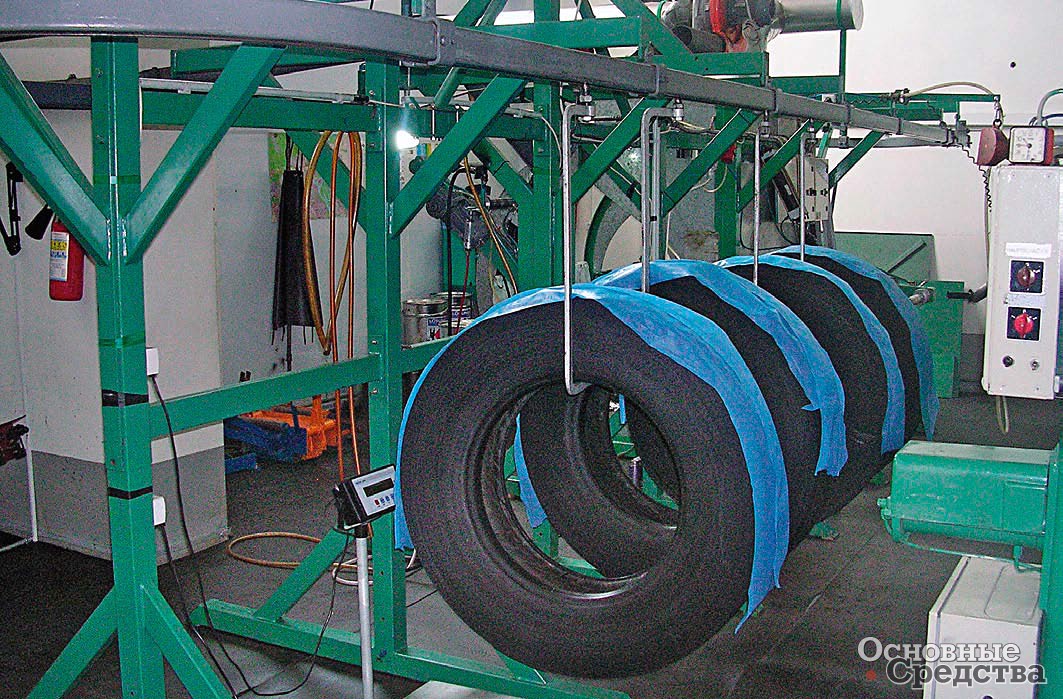
Метод механического дробления шин привлекает низкой себестоимостью и сохранением первоначальной структуры и свойств каучука и других полимеров, содержащихся в отходах. По этой технологии после удаления бортовых колец покрышки режут на четыре части и пропускают через вальцы. При дальнейшем измельчении получается резиновая крошка, но и в этом случае использовать металлокорд в качестве металлолома не представляется возможным из-за низкого качества очистки.
Криогенный способ измельчения решает задачи разделения покрышки на составные компоненты с достаточно высокой степенью чистоты, однако технология требует применения жидкого азота. Сложность его доставки, хранения, высокая стоимость и высокие энергозатраты на его производство являются основными причинами, сдерживающими в настоящее время внедрение низкотемпературной технологии. Возможно использование несколько более дешевых, но громоздких турбохолодильных машин для получения и очистки холодного воздуха и холодильных камер для заморозки кусков шин. Себестоимость получаемой при низких температурах крошки высокая, а поверхность крошки гладкая, и это ухудшает ее совместимость с другими полимерами, в том числе с каучуками.
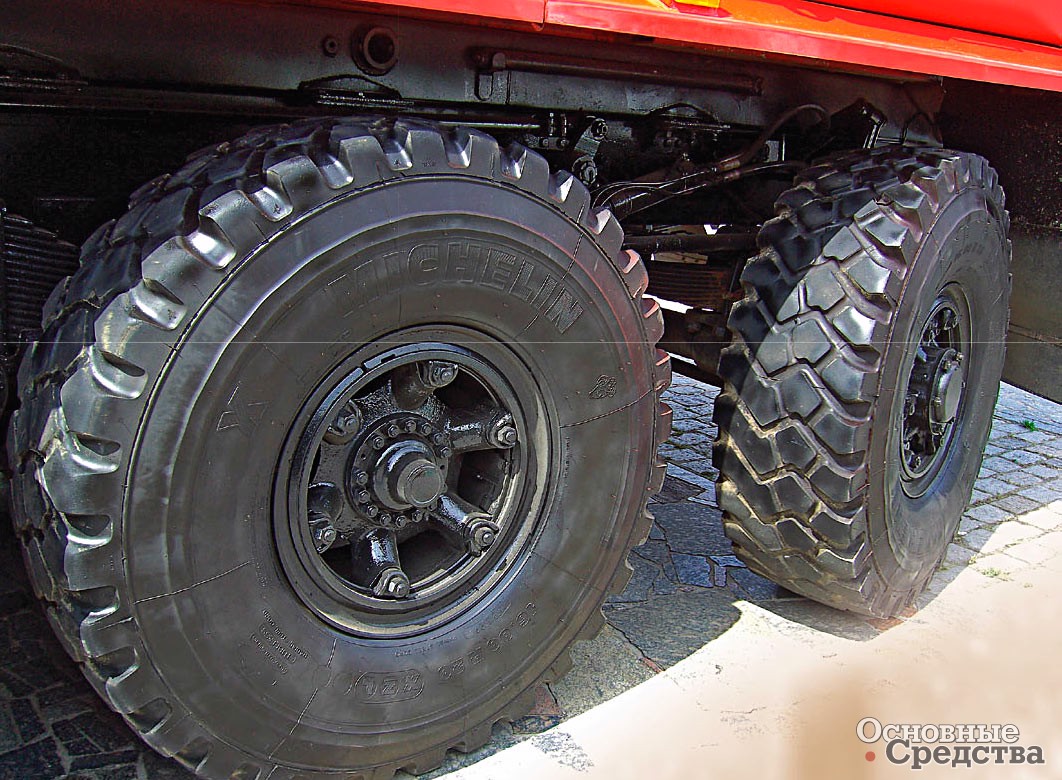
Один из перспективных, по оценкам специалистов, методов, разработанный российскими учеными и получивший в 2000 г. Золотую медаль Международного салона изобретений в Женеве, это «озонный» способ утилизации. Суть его в том, что после удаления бортового кольца шину режут на четыре части, помещают в специальную камеру и подвергают одновременно воздействию озоносодержащего газа и механическим нагрузкам. В процессе обработки озон разрушает связи в резине, а механическое воздействие способствует развитию микротрещин. В результате шина полностью рассыпается в мелкую крошку с отделением металлического и текстильного корда. Получаемый порошок не слипается, размер частиц не превышает 0,1…0,2 мм. Озонная технология значительно экономичнее других существующих и, кроме того, абсолютно экологически безвредна – озон окисляет все вредные газообразные выбросы. Недостаток метода в том, что полученная этим способом крошка при использовании в качестве добавки при изготовлении новых шин значительно ухудшает их физико-механические показатели.
Получило развитие и еще одно направление в утилизации шин – пиролиз. По этой технологии изношенные шины режут на крупные части, обрабатывают в специальных камерах химическим путем, а в результате образуется соляросодержащая жидкость, из которой путем магнитной сепарации отделяется металлокорд. Полученную жидкость в зависимости от ее качества можно использовать как топливо для котельных и различного рода печей, а при определенной дополнительной очистке можно получить дизтопливо неплохого качества. Тем не менее производство это экологически небезопасное, с достаточно вредными для персонала условиями труда, да и комплектация линии пиролиза установкой очистки получаемого на первой стадии мазута значительно увеличивает стоимость в целом довольно недорогого технологического процесса.
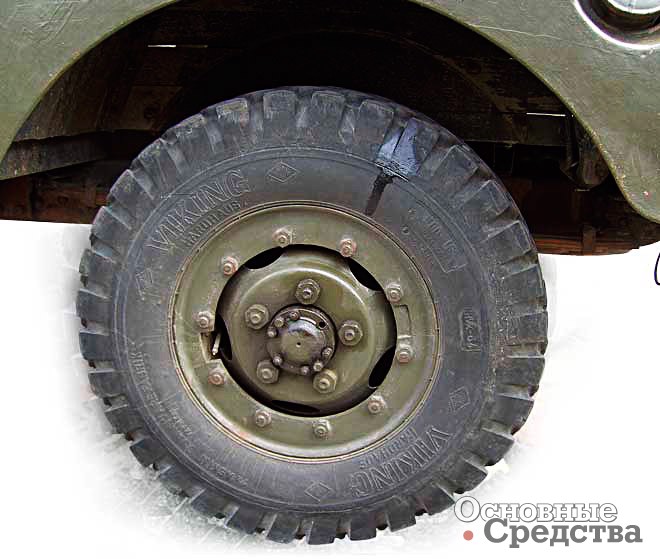
А может, еще побегаем?
Восстановление шин в условиях развивающегося общемирового кризиса может стать экономически неизбежным для предприятий, активно использующих в своей деятельности спецтехнику, а также для компаний, намеревающихся не терять позиции на рынке транспортных услуг. Внедрение новых экологических стандартов в России также способствует развитию этого направления производства.
Преимущества восстановленной шины очевидны. Вот пример: автопоезд-«фура» укомплектован 10 колесами. Шины «стираются» в среднем за год-полтора. И что же – выкидывать «лысую» резину массой 70...90 кг при истирании протектора до 2 мм высотой? Если используются импортные, в основном немецкие материалы для восстановления и при наличии импортного каркаса, в результате «наварки» можно гарантированно пройти еще 100…150 тыс. км. Вполне реально восстановить покрышку и два, и даже три раза, а это дополнительный пробег в 350…450 тыс. км. Если цена «наварной» грузовой шины составляет примерно 4,5…5 тыс. руб., то цена новой аналогичной от 9,5 тыс. руб. (Китай) до 16 тыс. руб. (Michelin).
В Европе объемы продаж «наварной» резины составляют примерно половину всего объема реализуемых грузовых и специальных шин. По статистике, 4/5 европейских предприятий, оказывающих транспортные услуги, покупают именно восстановленные покрышки, и это не самые бедные предприятия. В Китае 8 из 10 пригодных шин проходят восстановление, и это понятно: на производство новой покрышки в переводе на сырую нефть тратится 80 л, а на восстановление такой же всего 7 л!
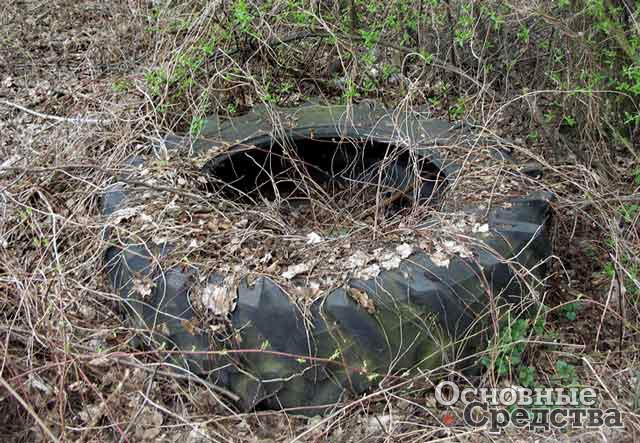
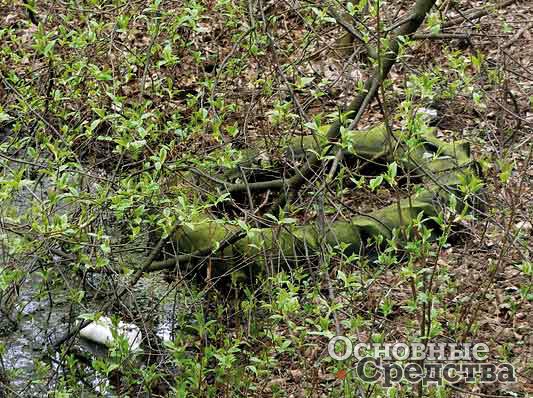
В общем, если на вашем автотранспортном средстве стоят шины ведущих мировых производителей – Bridgestone, Continental Yokohama, Nokian, Michelin и подобных и если вы видите, что покрышку в связи с износом даже на заднюю ось опасно ставить, вам надо решить, по какому пути пойти. Самое дешевое – это произвести так называемую «нарезку». Это специальный метод, при котором профессионально подготовленный работник с помощью спецоборудования углубит протекторные канавки миллиметра на три, в зависимости от первоначального износа. Европейский производитель, заранее предполагающий такой «конец» своего изделия, специально делает протекторный слой более толстым и ставит на боковине клеймо «Regroovable». Сложность метода состоит в том, что требуется довольно высокая точность прорезания ремонтируемой покрышки, а также в том, что углубление протектора возвращает жизнь покрышке ненадолго, и после этой операции практически все предприятия, восстанавливающие шины, в работу их не берут. Впрочем, преимущества в плане экономии очевидны: после такого ремонта колесо проходит еще 20…30% своего первоначального ресурса, но большое значение при этом имеет качественный уровень каркаса и квалификации нарезчика. А затраты на нарезку составляют всего 3% стоимости новой шины, тогда как затраты на восстановление наваркой – около 50…60% цены нового колеса, а «ходить» восстановленная покрышка будет примерно половину ресурса новой.
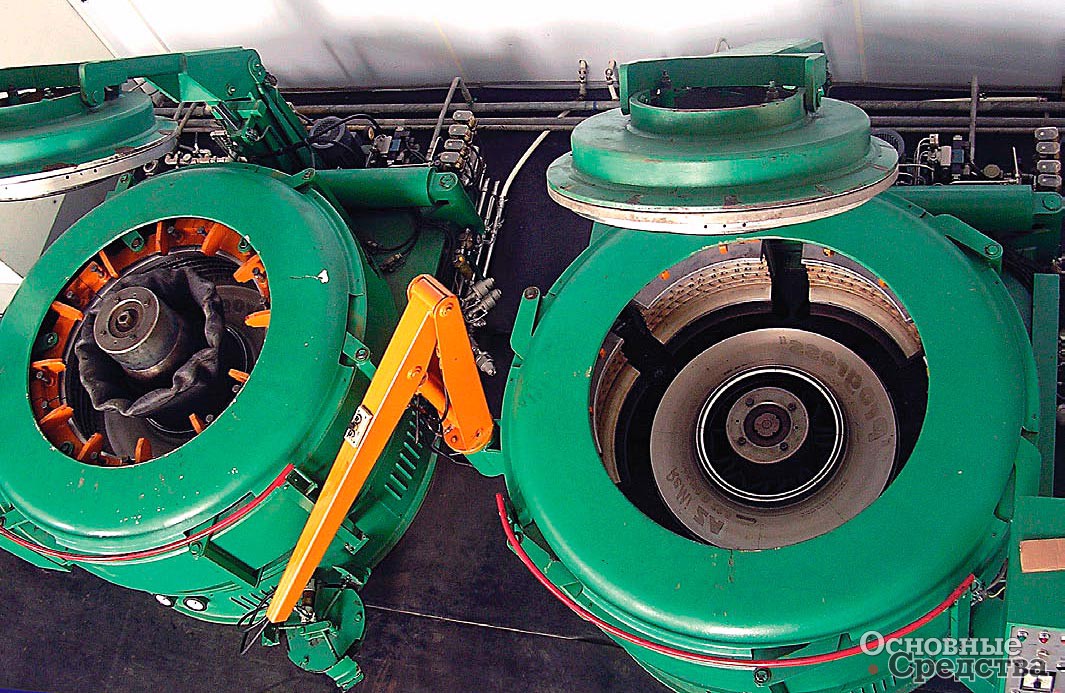
До конца 1950-х гг. почти единственным и широко применяемым был метод восстановления автомобильных шин «горячей» наваркой. Этот метод существует и сегодня, но требует больших производственных площадей и больших энергозатрат. Выгоден он в основном там, где большие объемы производства и «навариваются» в основном шины одного типоразмера и протектора. За рубежом этот метод применяют в основном для восстановления авиационных покрышек, при этом объемы восстанавливаемых авиашин все увеличиваются. Прочный многослойный каркас позволяет при нормальных условиях эксплуатации восстанавливать их 5...6 раз, но известны случаи, когда авиапокрышка «наваривалась» 15 раз! На имеющихся в России мощностях восстановлению подлежат каркасы и шины ведущих европейских фирм Michelin, Goodyear, Pirelli, Continental, Dunlop, Bridgestone, продукция которых рассчитана на вторую и третью жизнь. Отечественные покрышки мало восстанавливают из-за того, что чаще всего водитель стирает их до такой степени, что они попросту становятся непригодны для наварки, да и езда по нашим дорогам вызывает такие дефекты у и без того не очень мощного каркаса, что его при приемке чаще всего бракуют.
Предприятия, специализирующиеся на восстановлении колес, завозят каркасы из-за рубежа и при входном ультразвуковом контроле отбраковывают порядка 2% покрышек. При сдаче в наварку импортных качественных шин известных европейских брендов, износившихся уже на наших трассах, выбраковывают примерно 20% сдаваемых шин.
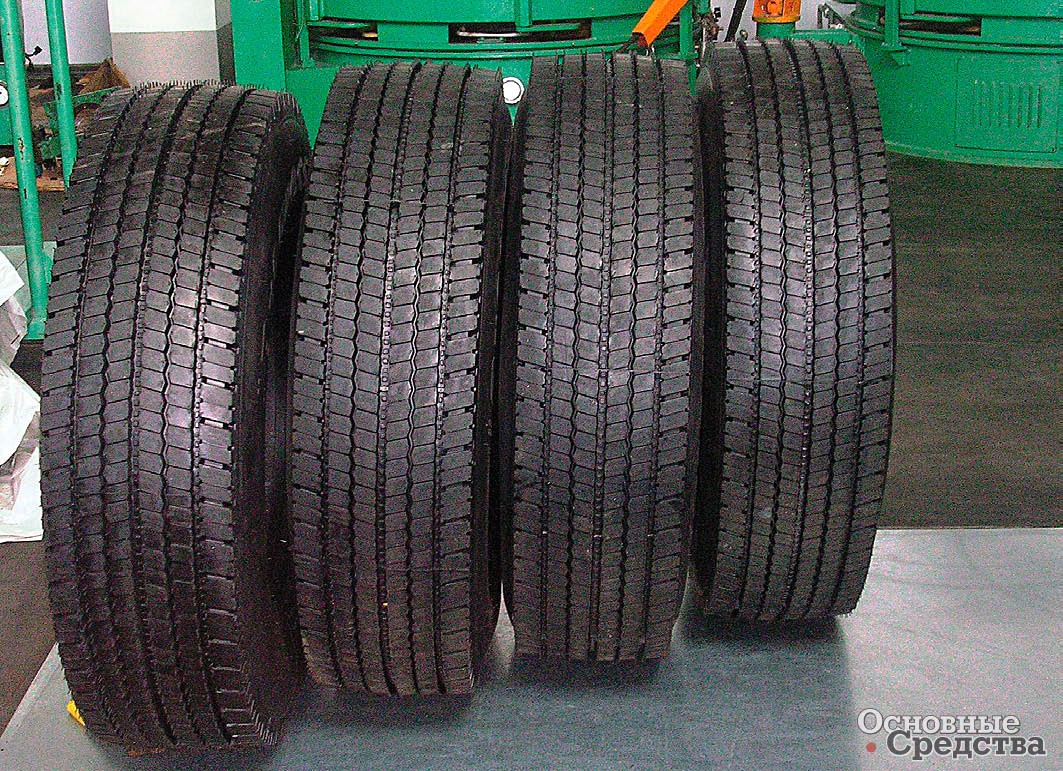
С появлением новых конструкций шин с металлическим кордом в каркасе и брекере основным методом восстановления стала «холодная» технология. При наличии каркаса высокого качества этот метод гарантирует возможность «наваривания» 3…4 раза. Для монтажа линии, производящей этим методом, к примеру, 900 покрышек в месяц, требуется производственное помещение площадью всего 500…600 м2 при рабочем потреблении тока 50…60 кВт.ч, и обслуживают линию четыре человека. Стоимость такой линии из Европы – порядка 220 тыс. евро.
К сожалению, в огромной России наберется не более двух десятков линий по восстановлению «холодным» способом, которые производят примерно 500...600 тыс. шин в год, а продажи новых шин исчисляются десятками миллионов. При существующих сегодня экономических реалиях нерентабельно возить на восстановление шины более чем за 500 км, поэтому потенциал деятельности этого сектора производства огромен. Конечно, стоимость восстановленной покрышки достаточно высока и ненамного отличается от цены отечественной новой. Однако если будет больше предприятий по восстановлению, то и цена снизится. Сегодня прибыль таких предприятий составляет от 70 до 100% на каждой покрышке, а значит, есть куда «подвинуться». Причем себестоимость восстановленной покрышки «горячим» способом почти вдвое ниже. И потом, куда все-таки девать изношенные шины предприятию? В Европе уже сегодня платят от 200 евро за тонну при сдаче шин в утилизацию, у нас пока в регионах цена от 3,5 тыс. руб., но в центре есть цена и 12 тысяч. В землю покрышку не закопаешь – все организации теперь отчитываются, какова судьба каждой отработавшей свое шины. Итак, инициативные российские предприниматели, слово за вами.
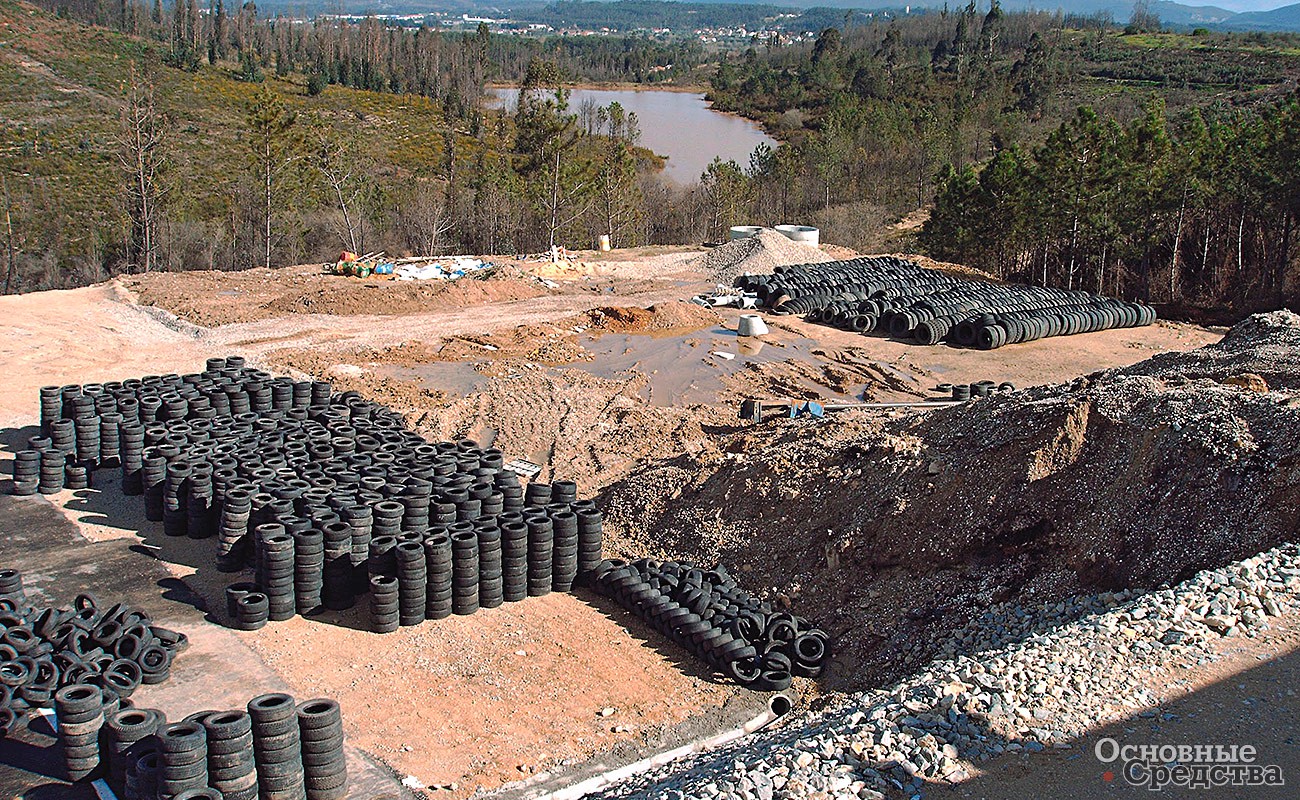

Goodyear разработала новую технологию восстановления шин TreadMax
Этот новый продукт является сочетанием новой технологии производства шин Max Technologies, разработанной Goodyear, и технологии восстановления шин с качеством, эквивалентным новой шине. При этом сопротивление качению восстановленной шины такое же, как у новой шины. В технологии TreadMax используются каркасы новой конструкции, разработанной специалистами Goodyear, ремонтный протектор наваривают по новой технологии. Толщина протекторов новых и восстановленных шин увеличенная, рассчитанная на повторную нарезку рисунка, и изготавливают их из резиновой смеси нового состава.
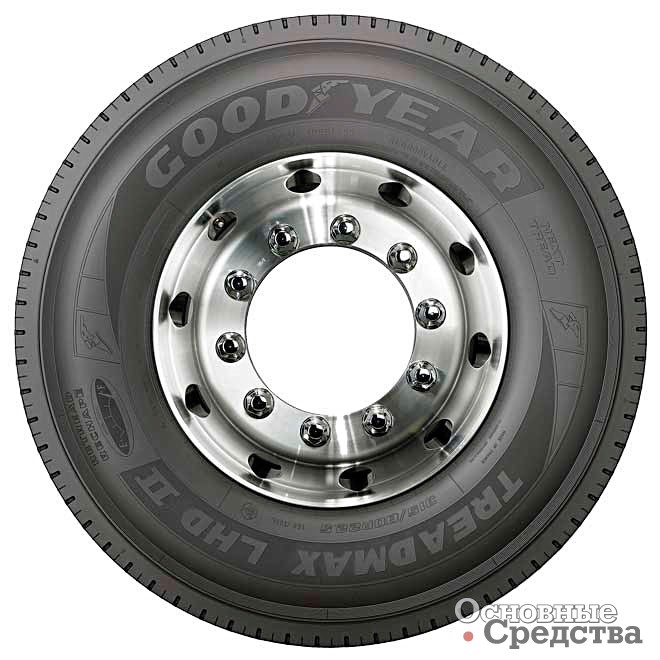
Goodyear утверждает, что ее шины рассчитаны на 4 срока эксплуатации. После первого износа протектора нарезают новые канавки, затем еще раз и еще, а в четвертый раз наваривают новый протектор TreadMax. И каркас шины рассчитан на столь долгий срок эксплуатации. Отремонтированная шина с наваренным протектором помечается как «Next Thread» – «новый протектор».
Новости от компании Yokohama
Еще в январе 2007 г. компания впервые в мире начала массовое производство шин из материала вторичной переработки. Этот материал производят из вулканизированной резины отработавших свой срок покрышек. Компания разработала технологию вторичной переработки шин, а уже в 2007 г. в производстве шин было использовано 400 т рециклированного материала.
Также Yokohama совместно с японской дорожно-строительной компанией Nippon Road Co., Ltd. разрабатывает новый материал для дорожного покрытия, в его состав входят крошка из измельченных старых шин и гравий, а в качестве вяжущего используется битум. Этот материал является альтернативой асфальту, и одно из преимуществ нового материала – снижение шума при прохождении автомобилей. Материал проходит испытания на некоторых дорогах общего пользования в Японии.