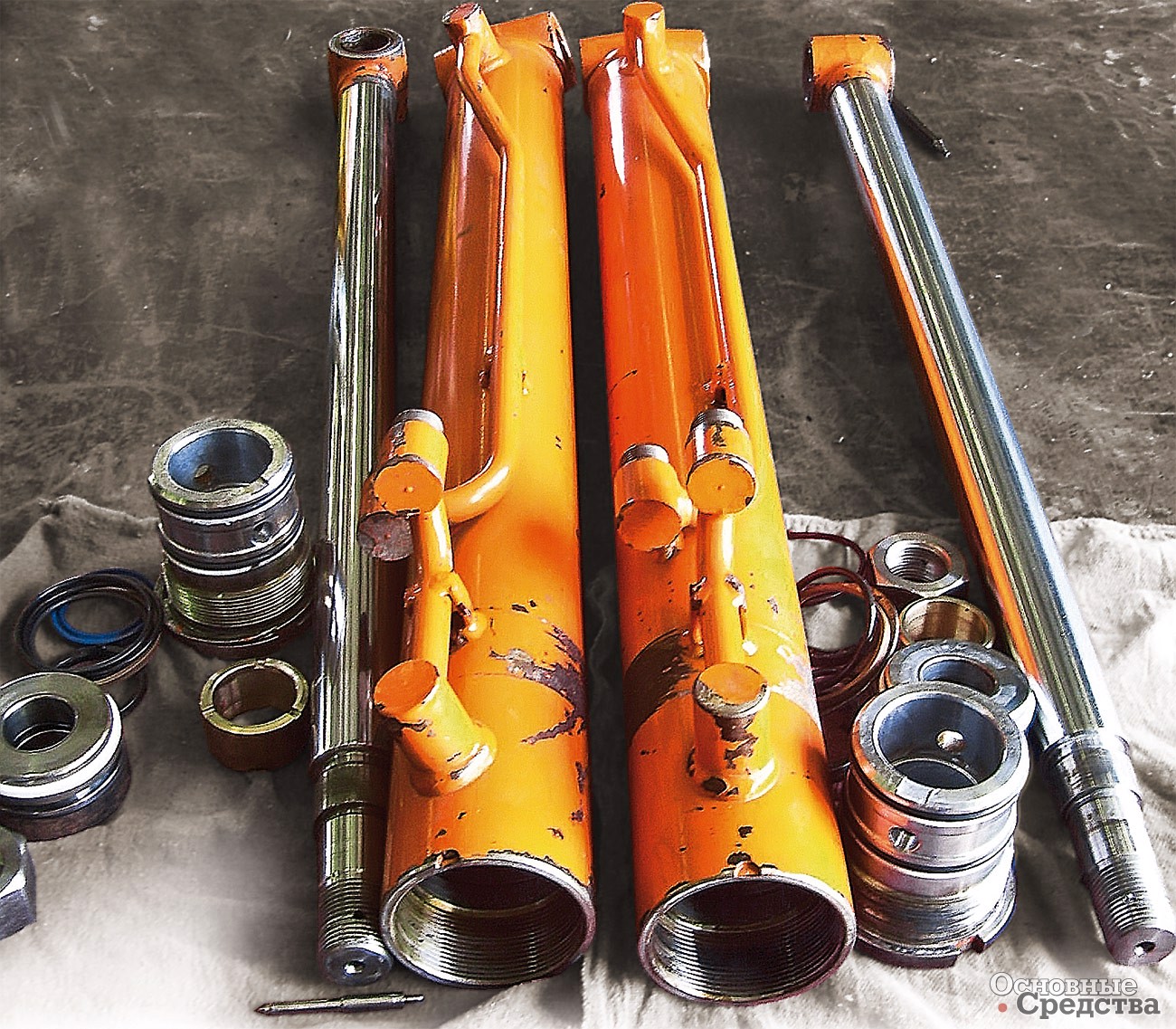
Гидравлика «в возрасте»
Сложности ремонта
Ремонт импортной гидравлики – направление довольно молодое на российском рынке услуг по ремонту и обслуживанию дорожно-строительной техники. Если говорить о наиболее дорогих и сложных в ремонте узлах: распределителях, насосах, гидромоторах хода, то настоящих специалистов в этом деле не так и много. Отрадно видеть, что чаще всего эти задачи решают не случайные люди, а специалисты с большим стажем работы, которые еще в советских НИИ изучали проблемы работоспособности гидропривода. Получается, что советская высшая техническая школа умела готовить настоящих мастеров своего дела, если они спустя десятилетия при серьезном дефиците технической информации умудряются реанимировать сложнейшие узлы импортной гидравлики.
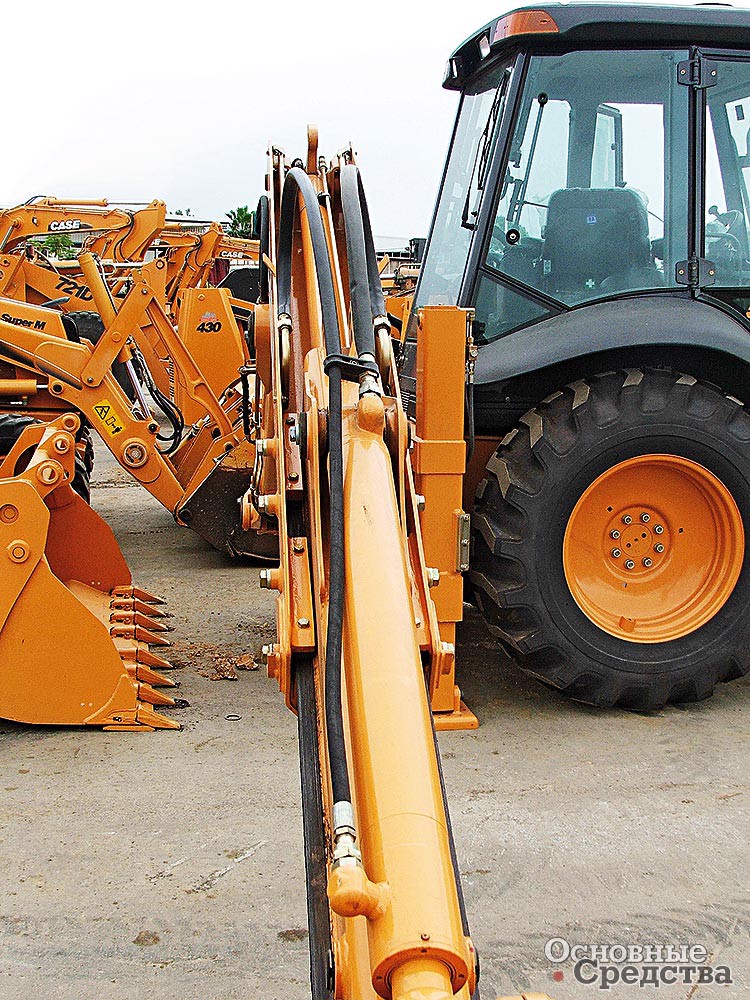
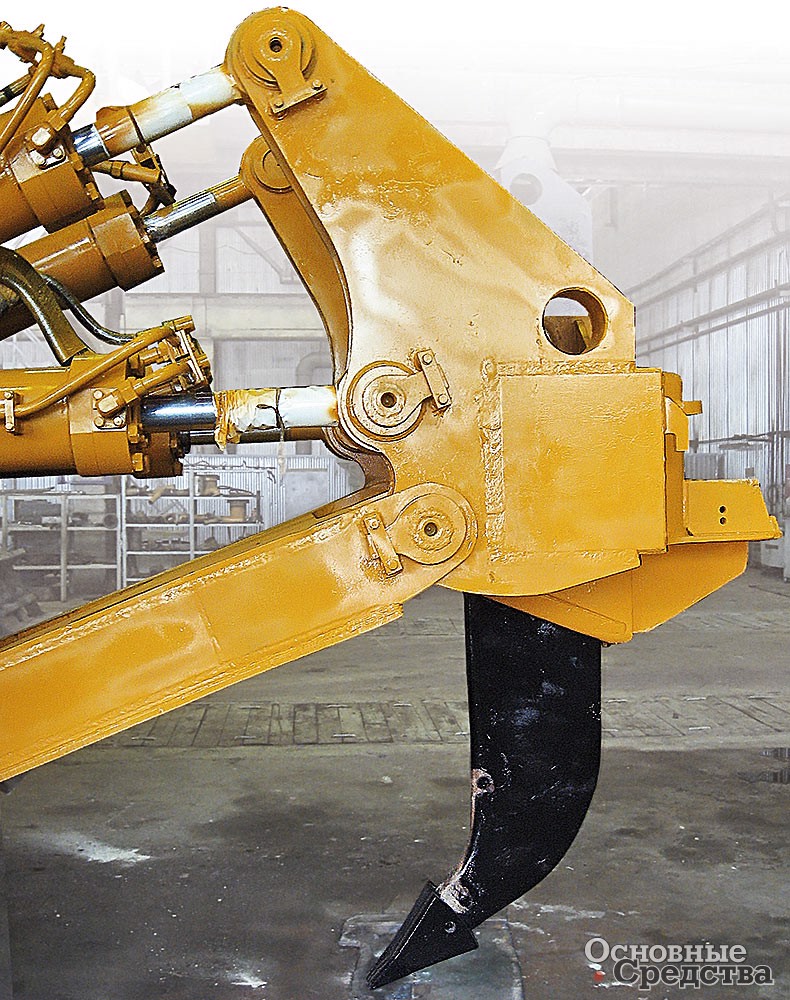
Посмотрим, что сегодня представляет собой рынок услуг по ремонту гидравлики на периферии. Как и рынок спецтехники, он очень четко делится на два сегмента. В первый сегмент попадают технические центры, где ремонтируют преимущественно отечественную гидравлику, во второй – сервис-центры по ремонту импортных агрегатов. Оба сегмента существуют весьма обособленно друг от друга. Клиентура сервис-центров разных сегментов практически не пересекается. Ремонтные предприятия, работающие с отечественной гидравликой, чаще всего созданы на базе организаций, где занимались ремонтом и обслуживанием тяжелой землеройной и дорожно-строительной техники еще в годы СССР. Если сравнивать с ситуацией, в которой оказались их коллеги, ремонтирующие импортную технику, то работают они в довольно спокойных условиях. У компаний приличная производственная база, многим даже удалось сохранить профессиональный коллектив. Эти сервис-центры отлично справляются с ремонтом отечественной гидравлики любой сложности, используя давно выстроенные связи с производителями комплектующих и накопленный опыт. Ремонт производят в полном соответствии с требованиями производителя. Каждый агрегат разбирают, затем моют детали и дефектуют. По результатам дефектовки принимают решение о восстановлении либо замене изношенных компонентов. При необходимости хонингуют внутренние поверхности под новый ремонтный размер. Серьезных проблем при ремонте обычно не возникает. Дефицита запасных частей на гидравлические агрегаты отечественного производства нет. Наиболее востребованные узлы, ремонтные комплекты и расходные материалы есть в наличии в большинстве сервис-центров. В таких сервис-центрах пытаются осваивать и ремонт импортной гидравлической аппаратуры, но все же предпочтение отдается текущему, несложному ремонту, не требующему замены оригинальных деталей и узлов. Такое избирательное отношение к ремонту импортной гидравлики объясняется высокой трудоемкостью и сложностями с поиском и поставками комплектующих.
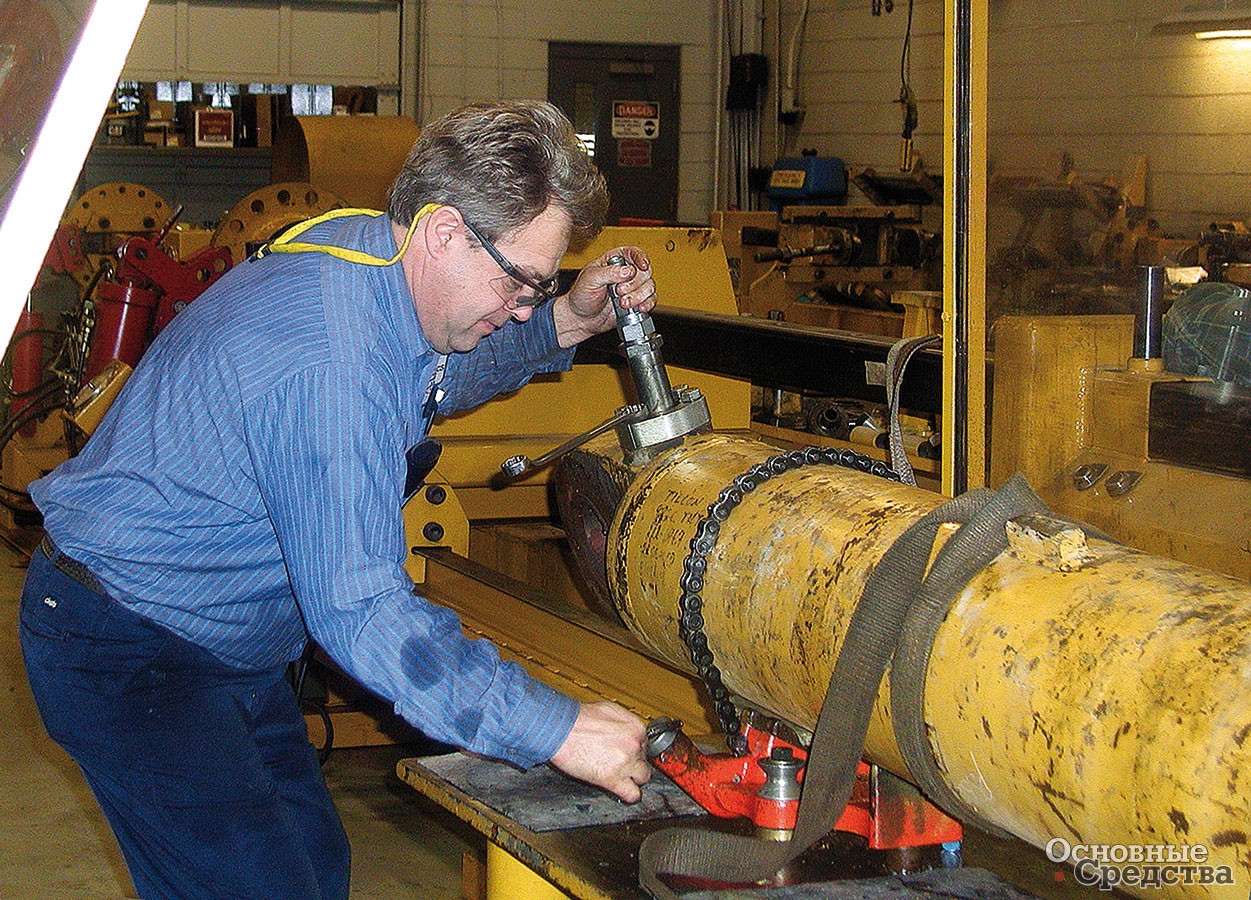
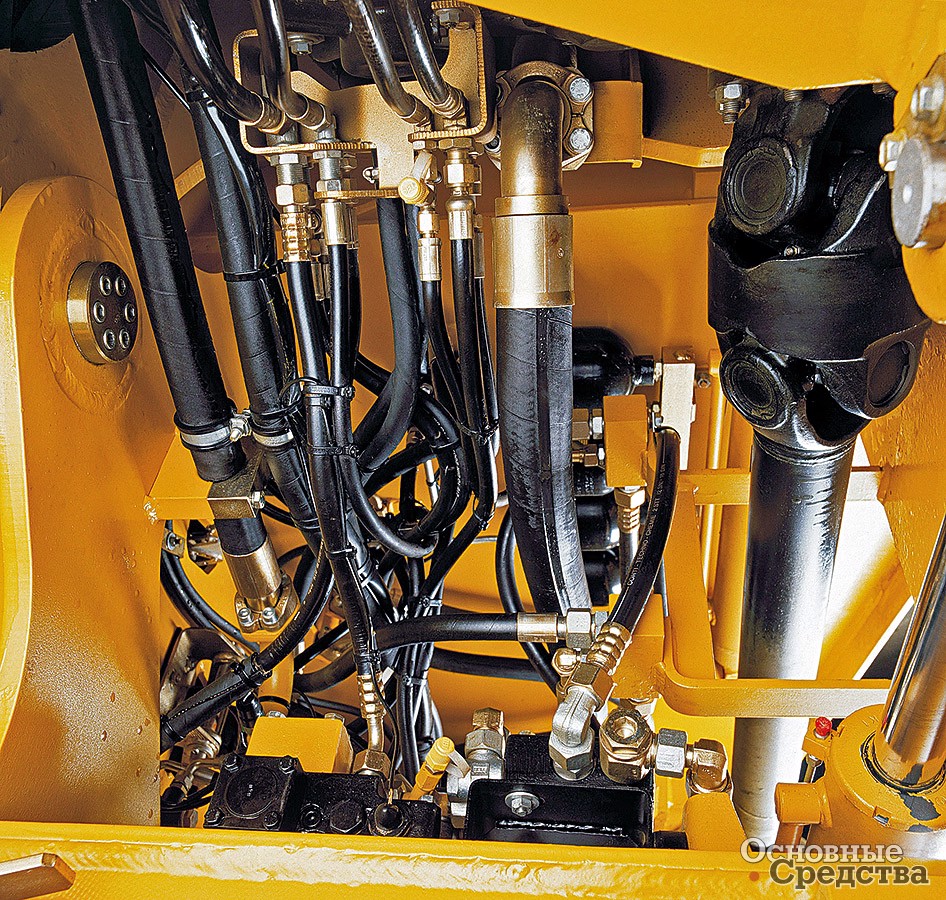
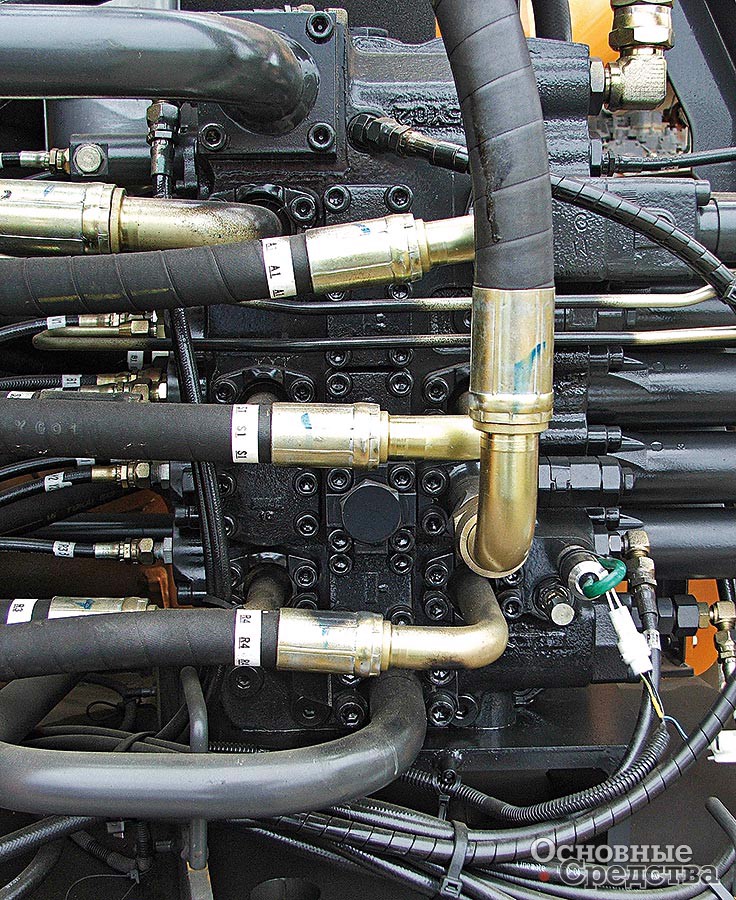
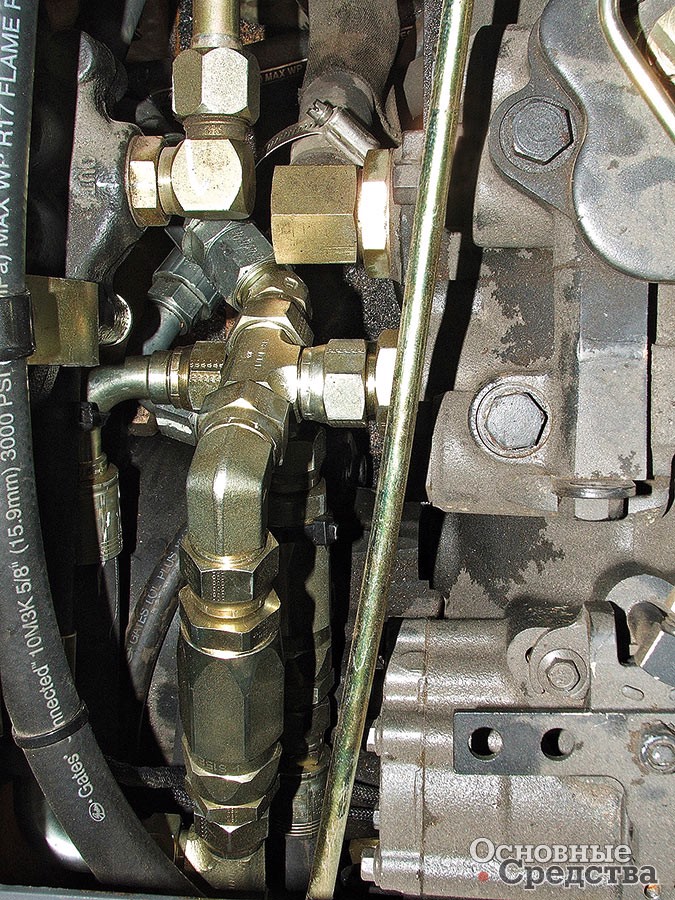
Самыми проблемными в ремонте являются гидравлические агрегаты, произведенные еще в 1990-х гг. К сожалению, в российских регионах доля техники с большим сроком эксплуатации все еще высока. Это связано с тем, что довольно длительное время парк дорожно-строительных машин активно пополнялся за счет японской и корейской техники, бывшей в употреблении. Эта техника приходит на российский рынок уже в весьма изношенном состоянии, причем наиболее массовым спросом пользуются экскаваторы, бульдозеры, краны и автовышки с наработкой не менее 10 лет. Отказы такой техники не редкость, тем более что российские потребители зачастую не выполняют элементарных требований по техническому обслуживанию. Какое-либо самостоятельное техобслуживание отсутствует вообще, как отмечают представители сервис-центров, и вызвано это не только отсутствием средств. Серьезную проблему представляет нехватка элементарной технической информации о регламенте ТО. Поскольку всю подержанную технику, которую ввозят в Россию, поставляют «серые» дилеры, у эксплуатантов порой нет даже карты смазки, а спецификации на рекомендованные смазочные и расходные материалы потребители также вынуждены собирать из сомнительных источников информации либо самостоятельно переводить японские и корейские документы. Официальные дилеры этих марок не хотят помогать владельцам такой техники, тогда единственный выход для них – это профессиональные независимые технические центры по ремонту гидроаппаратуры, где есть собственная производственная база, каталоги запасных частей, опытный персонал. Таких на рынке очень мало, и они также испытывают острую нехватку достоверной информации. Бо'льшая часть техники, поступающей в ремонт, уже снята с производства. Не производят и узлы гидравлической аппаратуры. Ремонтным предприятиям приходится искать аналоги или самостоятельно производить некоторые детали. Выполнить эту работу можно лишь при наличии оригинальных каталогов запчастей, а их на старую технику, которая официально не поставлялась на российский рынок, достать тоже непросто. На практике такая работа под силу только тем предприятиям, у которых есть налаженные связи с научными и конструкторскими бюро, которые в состоянии сделать необходимые расчеты на прочность и производительность гидравлики. И даже в этом случае требуется постоянный обмен информацией и опытом с дилерскими сервис-центрами. Эти факторы существенно отражаются на сроках и стоимости восстановительного ремонта, но если речь идет о тяжелой технике, то ремонт в любом случае оказывается более выгодным предложением, чем покупка нового агрегата. В среднем стоимость капитального восстановительного ремонта обходится на 40% дешевле, чем покупка нового агрегата.
Если же речь идет о технике, произведенной в середине 1990-х гг., то покупка нового гидроагрегата, например ходового гидромотора, вовсе не имеет смысла, поскольку его стоимость на 15…20% ниже, чем стоимость всей машины. Ремонт узла при существенно меньших затратах позволяет продлить эксплуатацию техники еще на несколько лет. В результате полноценного ремонта можно обеспечить ресурс до 70…80% от ресурса нового узла.
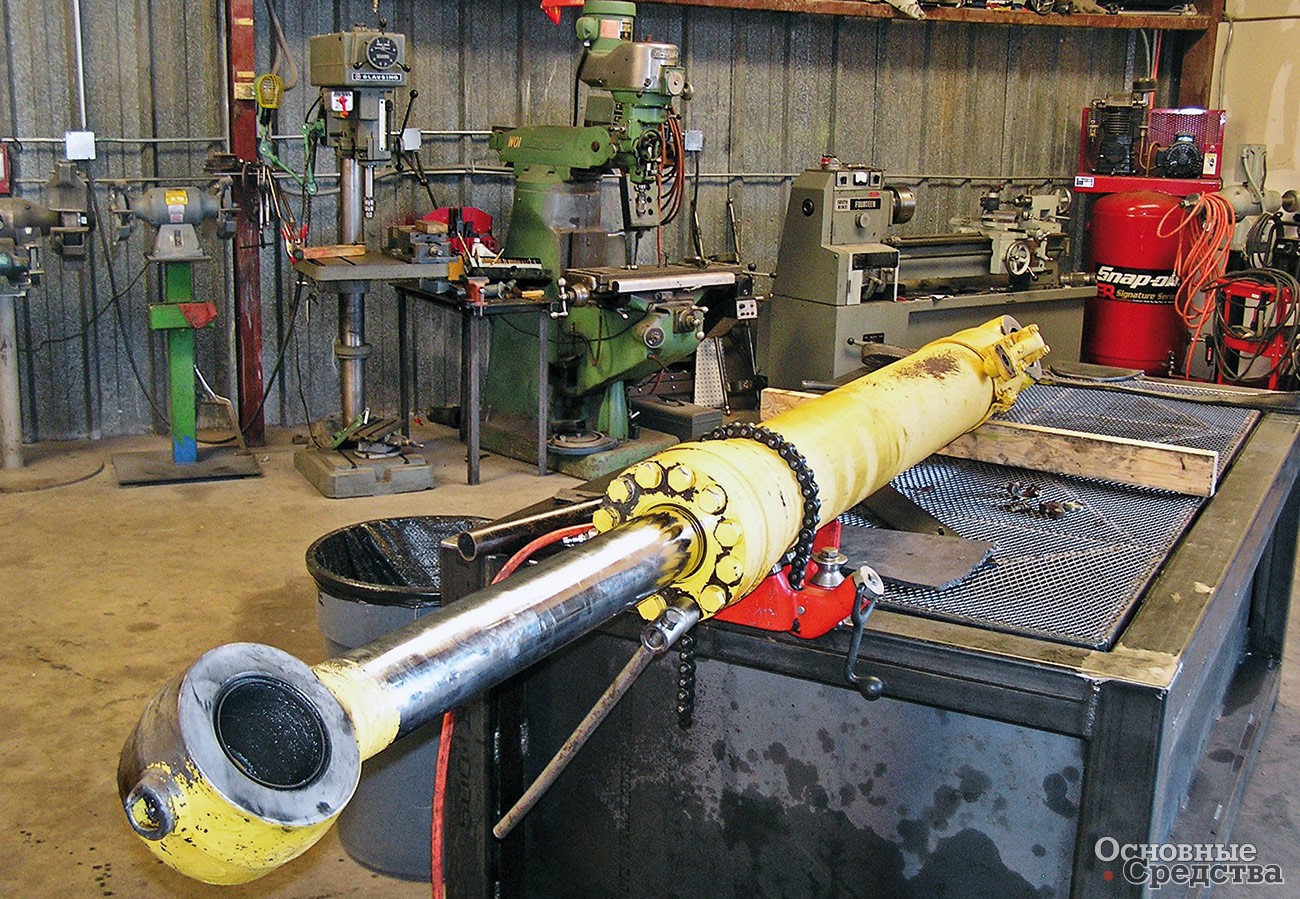
Впрочем, как отмечают технические специалисты, безграмотной эксплуатацией можно «убить» любой узел за несколько месяцев. Значительная часть техники находится в руках небольших компаний, где нет собственной ремонтной базы. Машины там работают буквально на износ. Гидравлическое масло и фильтры меняются нерегулярно. Часто происходит грубейшее нарушение правил эксплуатации: летом работают на зимнем гидравлическом масле, зимой – на летнем. Вязкость масла не соответствует рекомендованной. Эта проблема очень серьезная для карьерной и строительной техники, постоянно работающей в условиях сильнейшего запыления. Штоки гидроцилиндров таких машин постоянно находятся в контакте с цементной и рудной пылью. Масло загрязняется так быстро, что, если его не менять, очень скоро гидросистема начинает перекачивать вместо масла субстанцию, состоящую из смазочного материала и грязи. Такой коктейль приводит к сильнейшему износу пар трения в гидроагрегатах, нестабильной работе клапанов и золотников. И если пренебрегать элементарными правилами эксплуатации, вашей реальностью в ближайшее время станет капитальный ремонт гидравлики, поскольку обычной заменой уплотнений уже не обойдешься. И в завершение в очередной раз повторю банальные истины: чистота гидравлической жидкости – это залог длительной эксплуатации современной гидравлической аппаратуры.
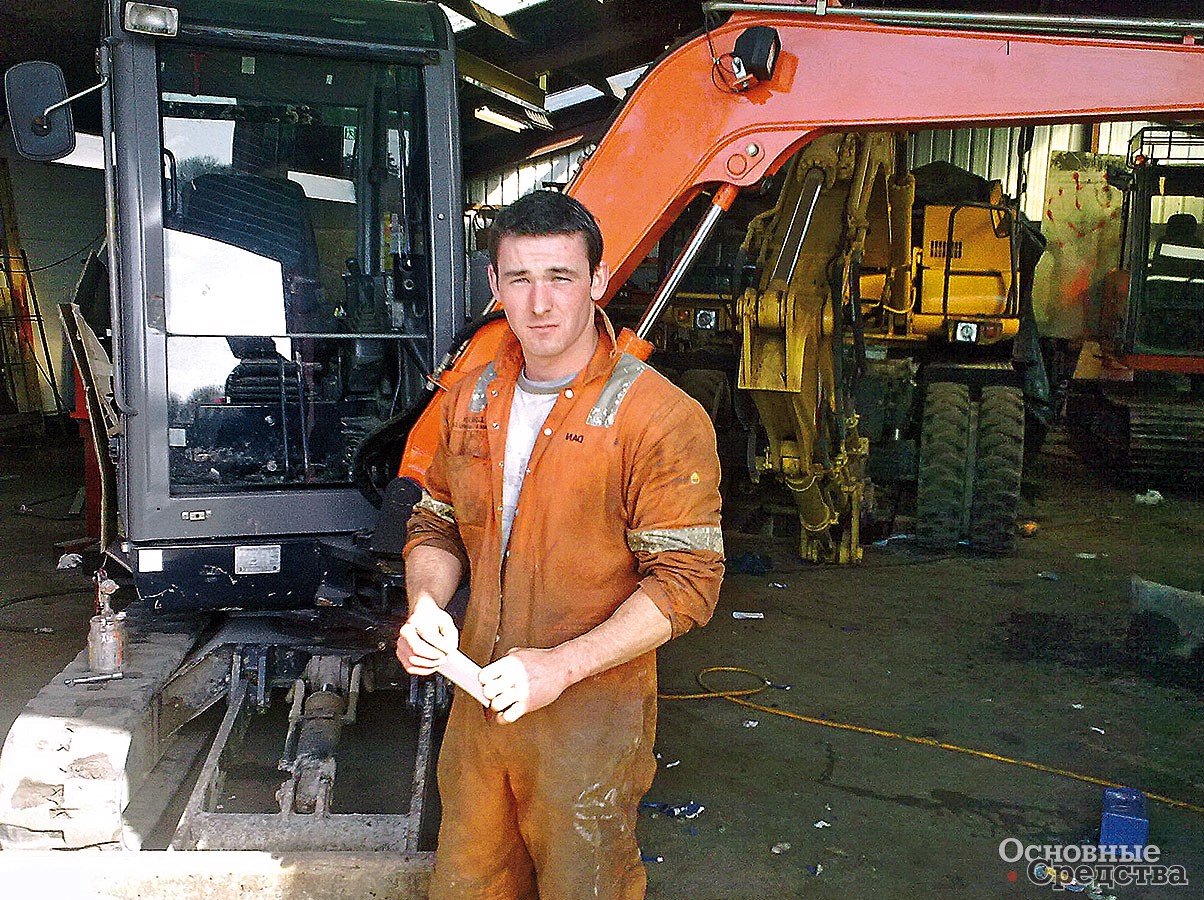