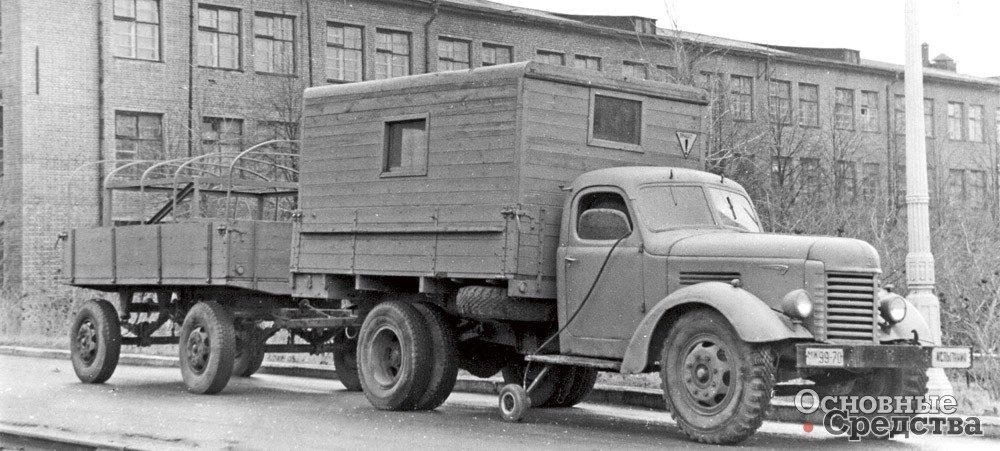
Тормоза по проводам
Тормозные механизмы с электроприводом для автомобильных прицепов
Такой привод позволял обеспечить малую величину времени срабатывания, гарантировал одновременность включения в действия тормозов на всех осях автопоезда, вне зависимости от состава автопоезда, давал возможность изменять характеристики темпа роста приводного усилия в широких пределах, что позволяло обеспечить полное согласование действия тормозов всех осей автопоезда. Кроме того, величины тормозных усилий электрического привода можно было изменять с места водителя или автоматическими приспособлениями, в зависимости от нагрузки тягача и прицепного состава, в зависимости от коэффициента сцепления шин с дорогой, обусловленного дорожными условиями, а также осуществлять раздельное управление тормозами тягача и прицепов.
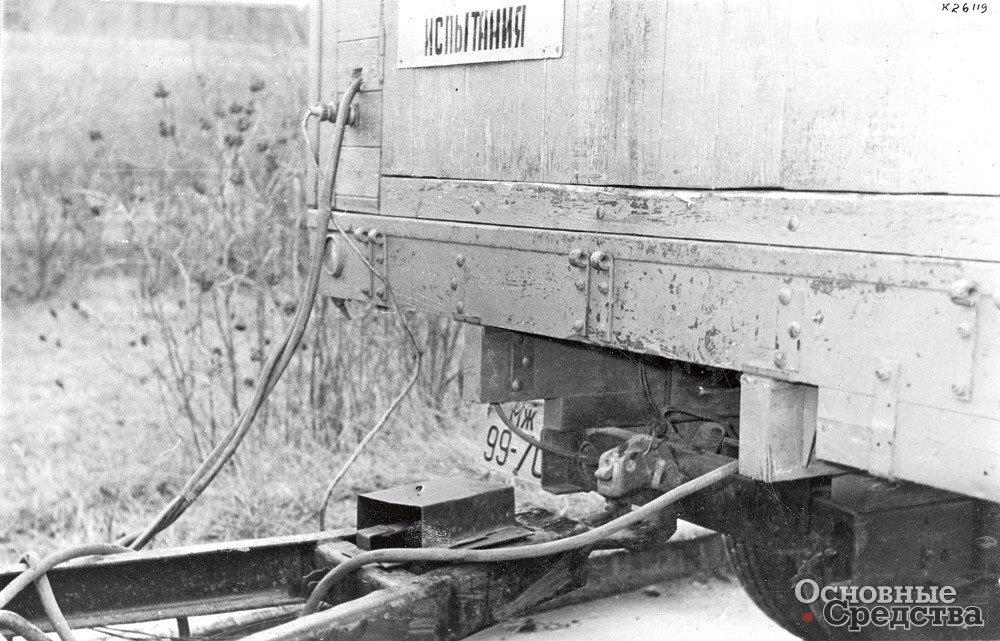
Приведенный в НАМИ анализ конструкций тормозов с электрическим приводом самых разнообразных типов показал, что для прицепов малой и средней грузоподъемности наиболее рациональными являются инерционные тормоза с электромагнитным приводом. Прицепы, оборудованные тормозами с электромагнитным приводом, могли работать с различными тягачами, имеющими любой привод к тормозам.
Одним из основных недостатков электромагнитных приводов к тормозам считалась зависимость работы тормозов от состояния заряда используемой аккумуляторной батареи. Максимальная сила тока, потребляемая электромагнитным приводом, составляет порядка 9–10 А в расчете на двухосный прицеп с тормозами на всех колесах, средняя сила потребляемого тока составляла 5–6 А. Таким образом, обычный автомобильный генератор мог обеспечить питание электромагнитных тормозов питанием электрическим током.
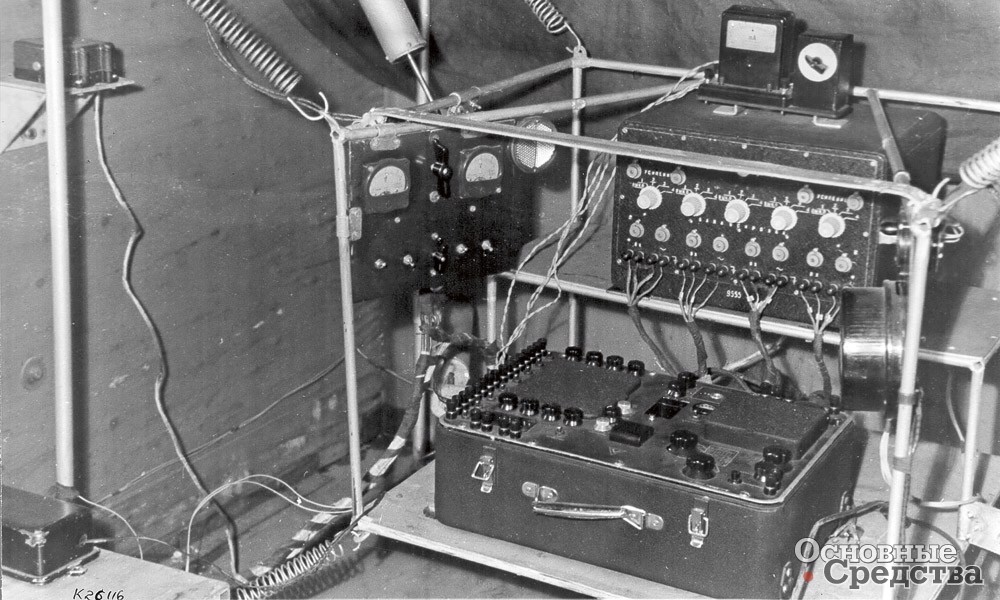
В 1957 г. в НАМИ сделали расчет электромагнитного привода для прицепа отечественного производства, затем выпустили рабочий проект и построили опытные образцы инерционного колесного тормоза с электромагнитным приводом для прицепа общей массой 6 т и грузоподъемностью 4 т. Эти образцы подвергли всестороннему исследованию на стенде и в дорожных условиях. Одновременно были построены образцы комбинированного контроллера (блока управления), позволяющего осуществлять управление тормозами прицепа как совместно с тормозами тягача, так и раздельно, то есть включать тормоза только прицепа.
Разработанные и построенные в НАМИ инерционные тормоза с электромагнитным приводом имели колодочный тормозной механизм, выполненный в двух вариантах: с двумя заклиниваемыми (плавающими) колодками и с колодками, работающими с самоусилением. Тормозной механизм с двумя заклиниваемыми колодками обладает следующими положительными качествами:
- возможностью получения более высокой эффективности торможения по сравнению с тормозами обычного типа за счет использования обеих колодок в качестве ведущих;
- одинаковая эффективность действия тормоза при движении вперед и назад;
- тормоз имеет хорошее следящее действие то есть обеспечивает определенную пропорцию между усилием привода и тормозным моментом.
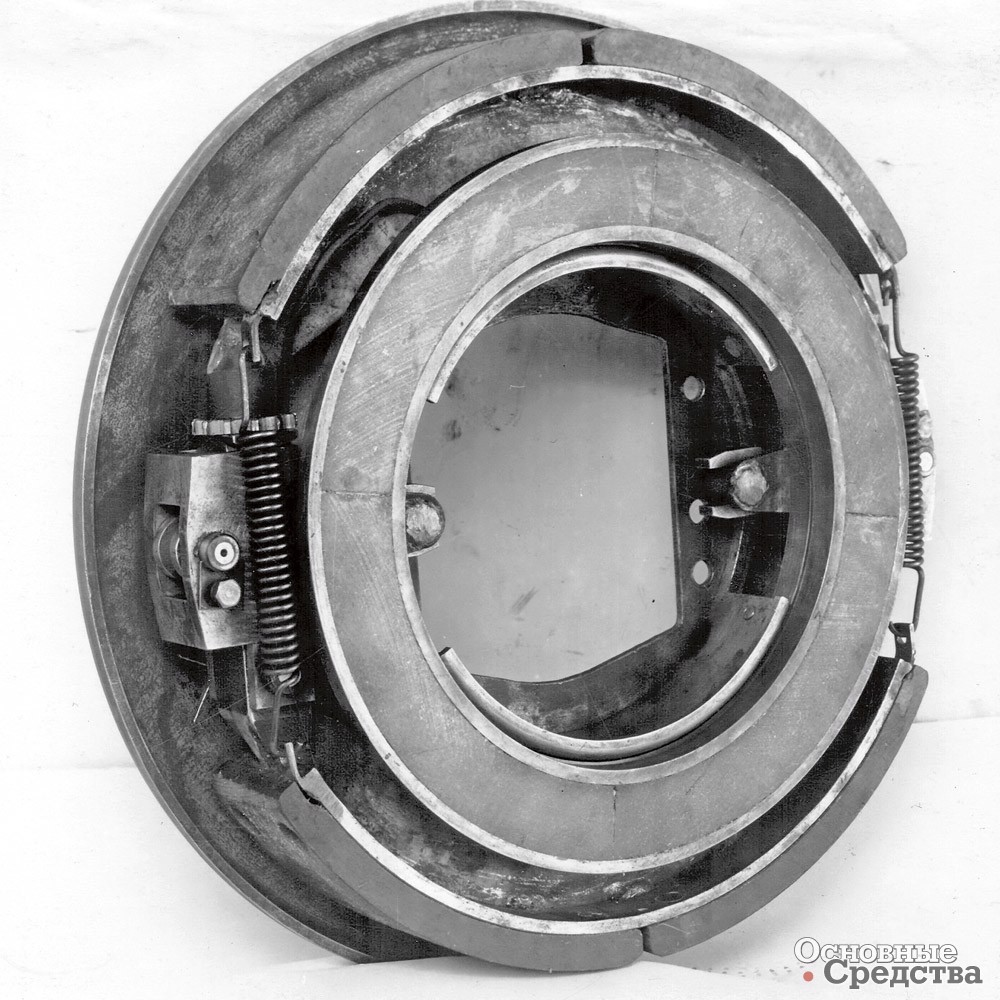
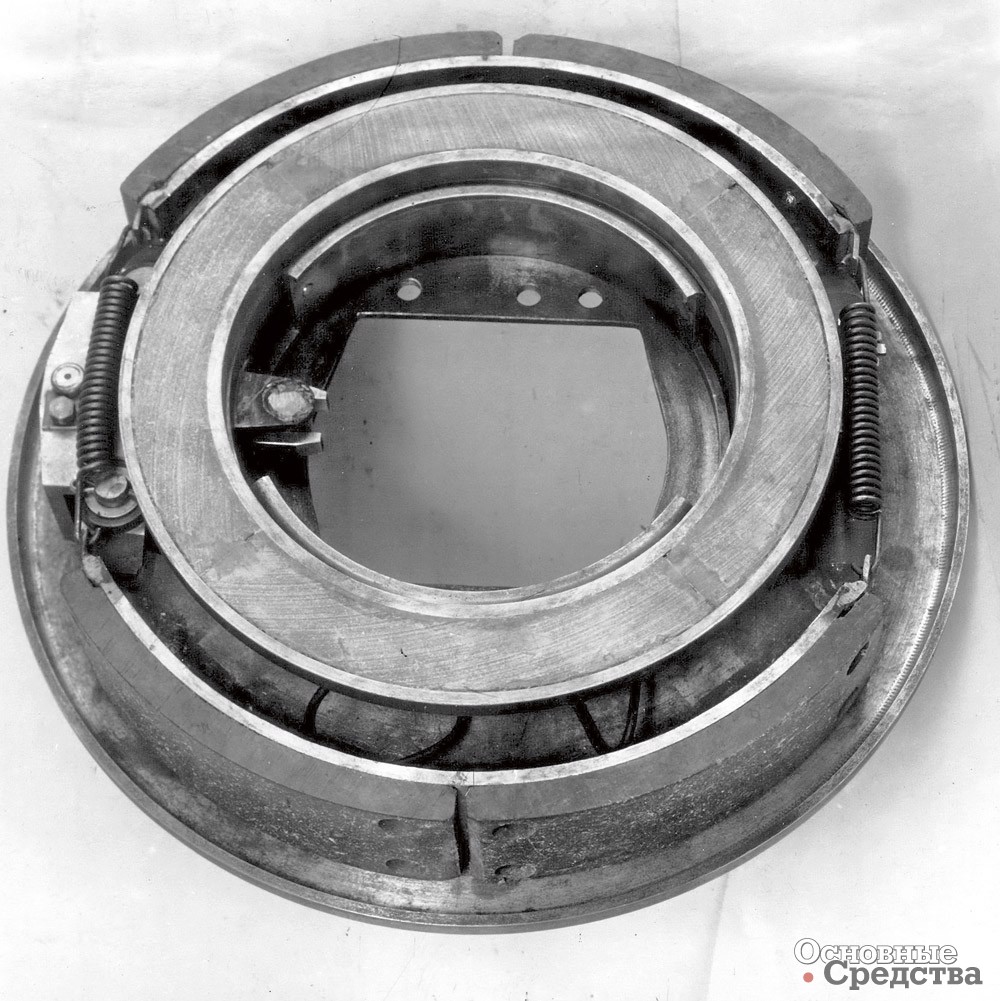
Тормозной механизм с самоусилением, то есть с передачей усилия от одной колодки на другую, был сделан для определения максимально возможного тормозного момента при тех же габаритах и параметрах тормоза и электромагнита. Диаметр тормозного барабана опытных образцов тормозов НАМИ равнялся 420 мм. Такой габаритный размер был принят из условия установки тормоза в колесе автомобиля ЗИЛ-150. Электромагнитный привод состоял из двух основных частей: кольцевого электромагнита и якоря в виде диска. Электромагнит свободно надевался на опору, приваренную к тормозному щиту, и мог на ней поворачиваться в обе стороны на определенный угол, ограниченный упором. Величина этого угла соответствовала повороту с изношенной тормозной накладкой, при которой тормоз будет еще работать без регулировки.
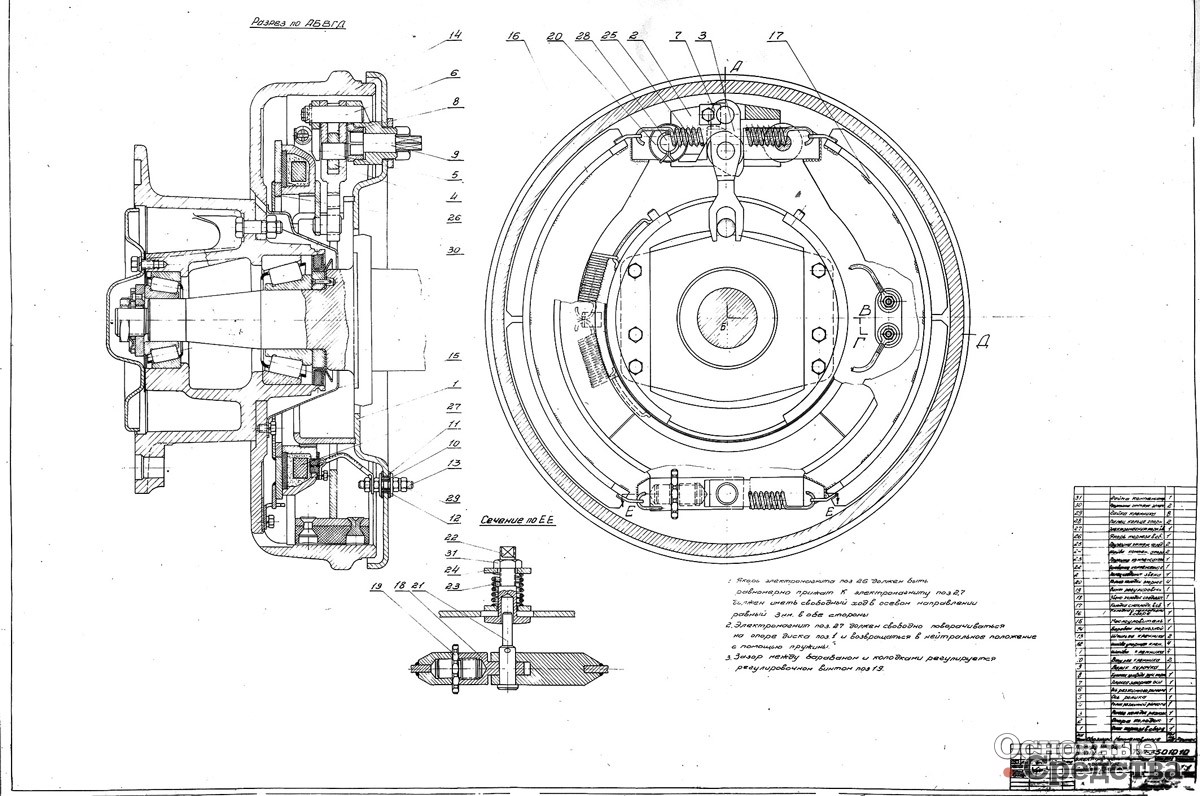
Электромагнит имел корытообразный корпус кольцевого типа, выполненный из магнитопроводной стали. В корпусе размещалась обмотка, залитая для предохранения от влаги и повреждений составом, состоящим из бакелитового лака с литейным песком, высушенным в печи при температуре 140–160 °С в течение трех часов. Для создания необходимого трения между якорем и электромагнитом со стороны его полюсов приклеивалась кольцевая фрикционная вставка. Для обеспечения быстрой приработки полюса неработавшего магнита выступали над поверхностью вставки на 0,2–0,3 мм. После приработки на якоре образовывались две концентрические канавки в местах соприкосновения полюсов электромагнита. В месте посадки корпуса электромагнита на опоры впрессовывались медные кольца, служащие подшипником и экраном, предотвращающим рассеивание магнитного потока. После торможения две пружины возвращали электромагнит в нейтральное положение.
Якорь состоял из двух дисков из мягкой стали, разделенных между собой медной фольгой толщиной 0,15 мм и сваренных медью. Медная прокладка снимала остаточную намагниченность якоря, чем обеспечивалось «чистое» растормаживание. Якорь присоединялся к тормозному барабану через пластинчатые пружины, дающие ему возможность перемещаться в осевом направлении, и постоянно прижимали его с небольшим усилением к полюсам электромагнита. Через эти пружины на барабан передавался реактивный момент муфты. Сам якорь крепился к тормозному барабану шестью болтами. В рабочем положении якорь должен был перемещаться от первоначального положения примерно на 4 мм в сторону деформации пластинчатых пружин. Этим обеспечивалось необходимое прижатие якоря к полюсам электромагнита и компенсировался возможный износ поверхностей трения электромагнитной муфты. Проверка правильности положения якоря производилось замером расстояния между торцом якоря и барабанов при снятом барабане и при собранном тормозе через специальное окно в тормозном барабане.
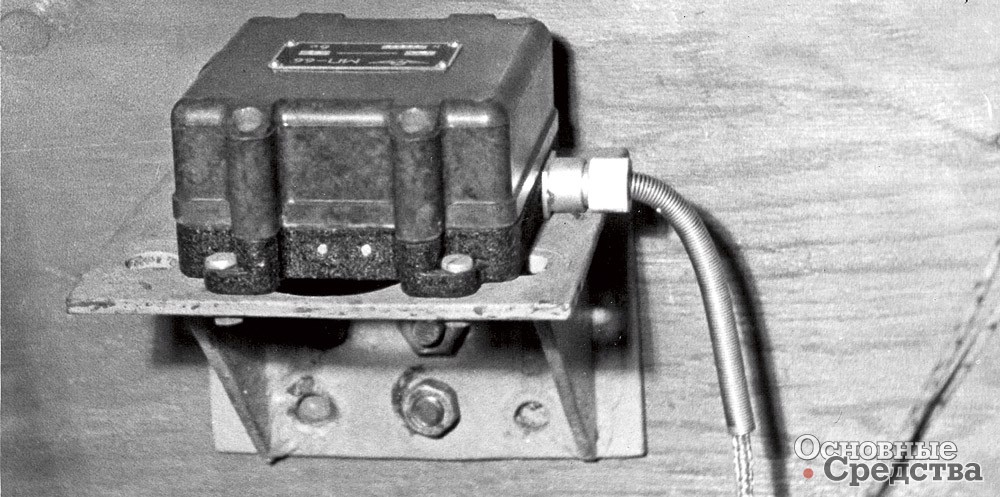
Тормоз, работающий с самоусилением, имел одну опору колодок, на которую опирались колодки сварной конструкции через опорные кольца и пальцы колец. С другого конца колодки соединялись через наконечники пальцем. Регулировка зазора между тормозным барабаном одной накладки производилась винтом, а другой – автоматическим устройством. В тормозе такого типа уменьшено передаточное отношение рычажной передачи от электромагнита к колодкам по сравнению с тормозом предыдущей конструкции.
Работа тормоза с электромагнитным приводом происходила следующим образом: при возбуждении электромагнита вращающийся якорь притягивался к электромагниту и увлекал его за собой. Электромагнит поворачивался на некоторый угол и через разжимные рычаги воздействовал на колодки, прижимая их к барабану. Сила нажатия на колодки зависела от момента трения, создаваемого электромагнитной муфтой, то есть пропорционально величине тока, проходящего по обмотке электромагнита. Питание электромагнитных тормозов прицепа производилось от аккумуляторной батареи автомобиля напряжением 6 В. Изменение величины тока, идущего в обмотки возбуждения электромагнита тормоза, осуществлялось посредством изготовленного в НАМИ комбинированного контроллера, который позволял производить включение тормозов как от пневматического привода тормозов тягача, так и водителю. Водитель мог, управляя контроллером, затормаживать автопоезд только одним прицепом. Контроллер представлял собой ступенчатый реостат и состоял из 10 сопротивлений, соединенных с латунными пластинами различной длины, которые замыкались контактной пластиной при перемещении штока приводной камеры. Приводная камера присоединялась к пневматическому приводу тормозов тягача.
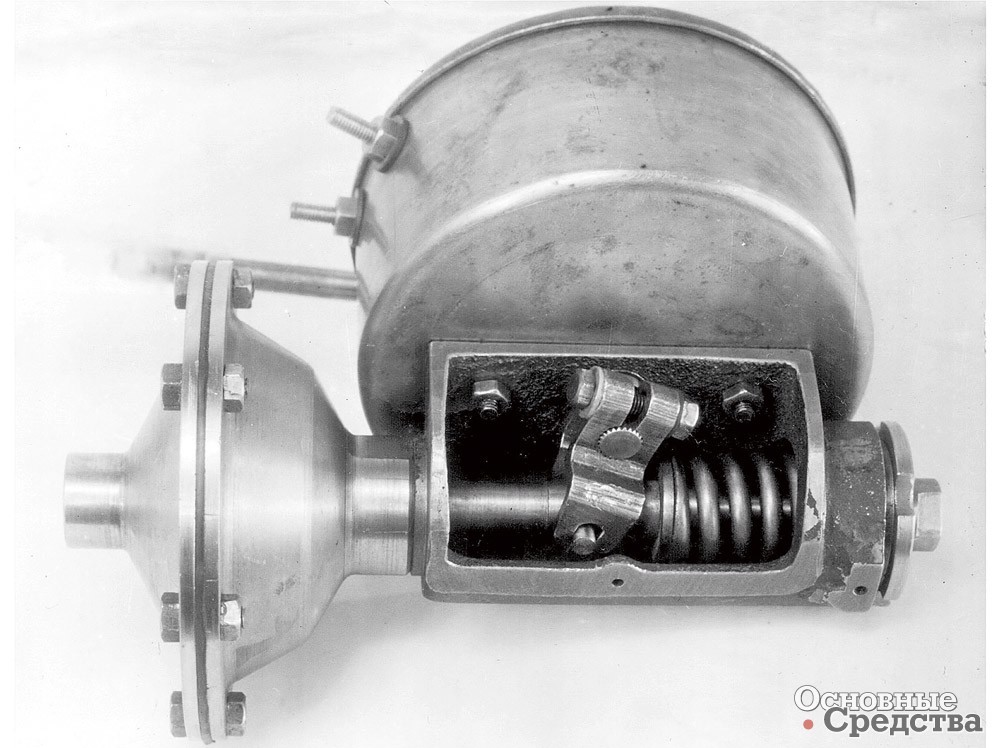
Изготовленные опытные образцы тормоза с электромагнитным приводом смонтировали на прицеп ЛАЗ-729. Прицеп должен был буксироваться грузовиком ЗИЛ-120, на котором была смонтирована аппаратура управления. Комбинированный контроллер для удобства пользования ручным включением тормозов прицепа устанавливался на рулевой колонке автомобиля. Реостат регулирования силы торможения прицепа установили в кабине на специальном щитке. На щитке располагались две сигнальные лампочки, с помощью которых должен был осуществляться контроль за направлением усилия, действующего в сцепке: сжатие показывала красная лампочка, зеленая – растяжение. Лампочки работали от датчика, установленного на дышле прицепа. Лампочки зажигались только при включении стоп-сигнала. С помощью контроля усилия в сцепке устанавливалось требуемое положение реостата, соответствующее правильной соразмерности действия тормозов тягача и прицепа в зависимости от загруженности прицепа.
Предусматривались испытания автопоезда с полной нагрузкой, с половинчатой нагрузкой прицепа и без него; с разгруженным тягачом, буксирующим прицеп без нагрузки и с полной нагрузкой. Определение тормозного пути производилось «пятым колесом» и прибором «путь-скорость-время». Запись параметров торможения автопоезда производилась на горизонтальном участке сухого асфальтированного шоссе при начальной скорости движения 30 км/ч. Торможение производилось при резком и плавном включении тормозного привода с помощью специального пневматического цилиндра, который приводился в действие от ручного крана, установленного на рулевой колонке тягача, с питанием от отдельного ресивера, размещенного в кабине. Отдельным реостатом, установленным в цепь электромагнитного привода, изменялась тормозная сила на задних колесах прицепа из-за перераспределения нагрузок на оси прицепа при торможении.
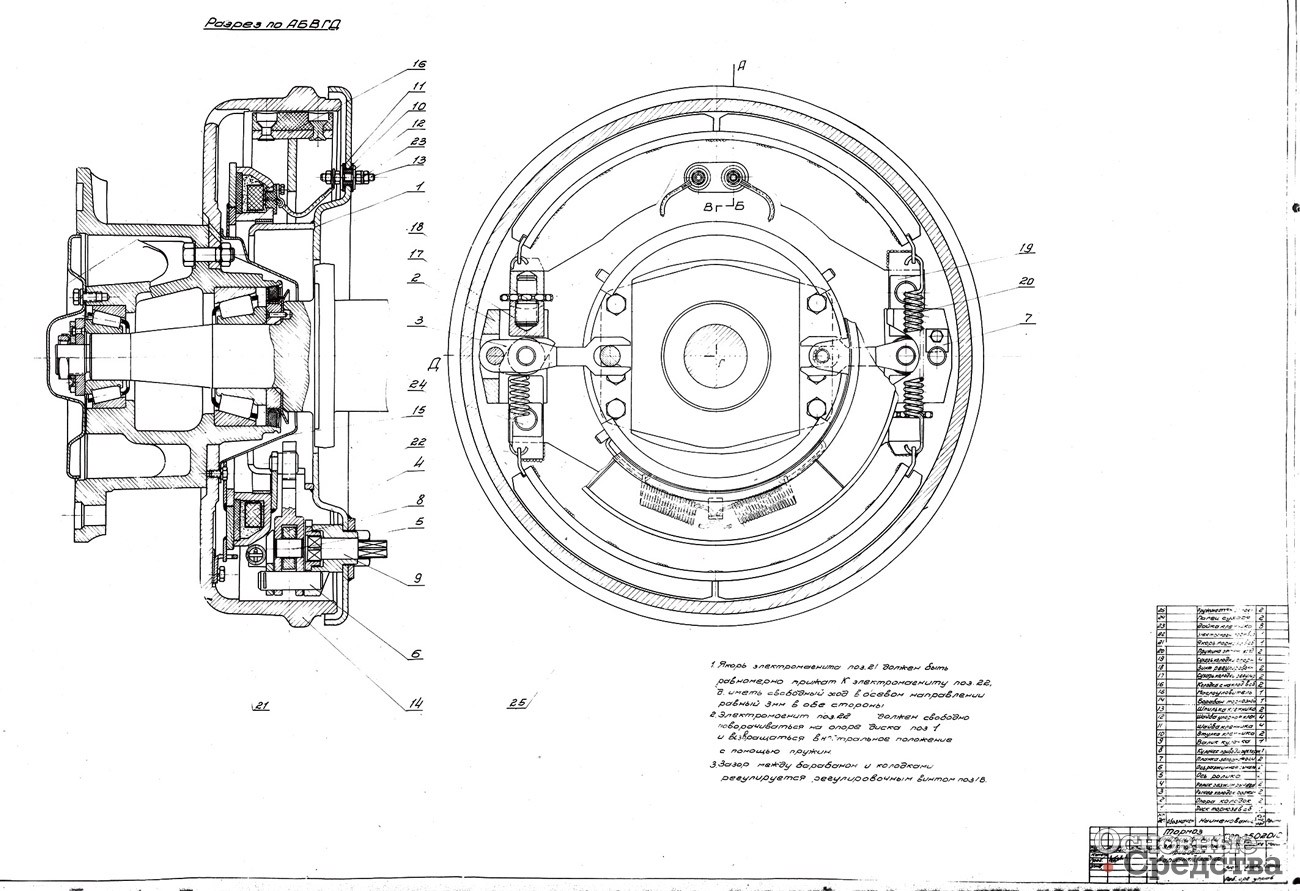
Во время испытаний связь между водителем и оператором, размещенным в кузове автомобиля, осуществлялась с помощью звукового сигнала, включаемого оператором. Оператор следил за записью параметров торможения осциллографической установки. Установка состояла из шлейфового осциллографа типа МПО-2, четырехканального усилителя, блока умформеров РУ-II, блока питания, состоящего из двух аккумуляторных батарей по 12 В. Осциллограф записывал следующие параметры процесса торможения:
а) давление воздуха в передней тормозной камере тягача;
б) давление воздуха в задней тормозной камере тягача;
в) тормозной момент переднего колеса тягача;
г) тормозной момент заднего колеса тягача;
д) усилие в сцепке;
е) тормозной момент переднего колеса прицепа;
ж) тормозной момент заднего колеса прицепа;
з) ток в обмотке возбуждения электромагнита заднего тормоза прицепа;
и) замедление автопоезда;
к) отметку времени каждые 0,25 с.
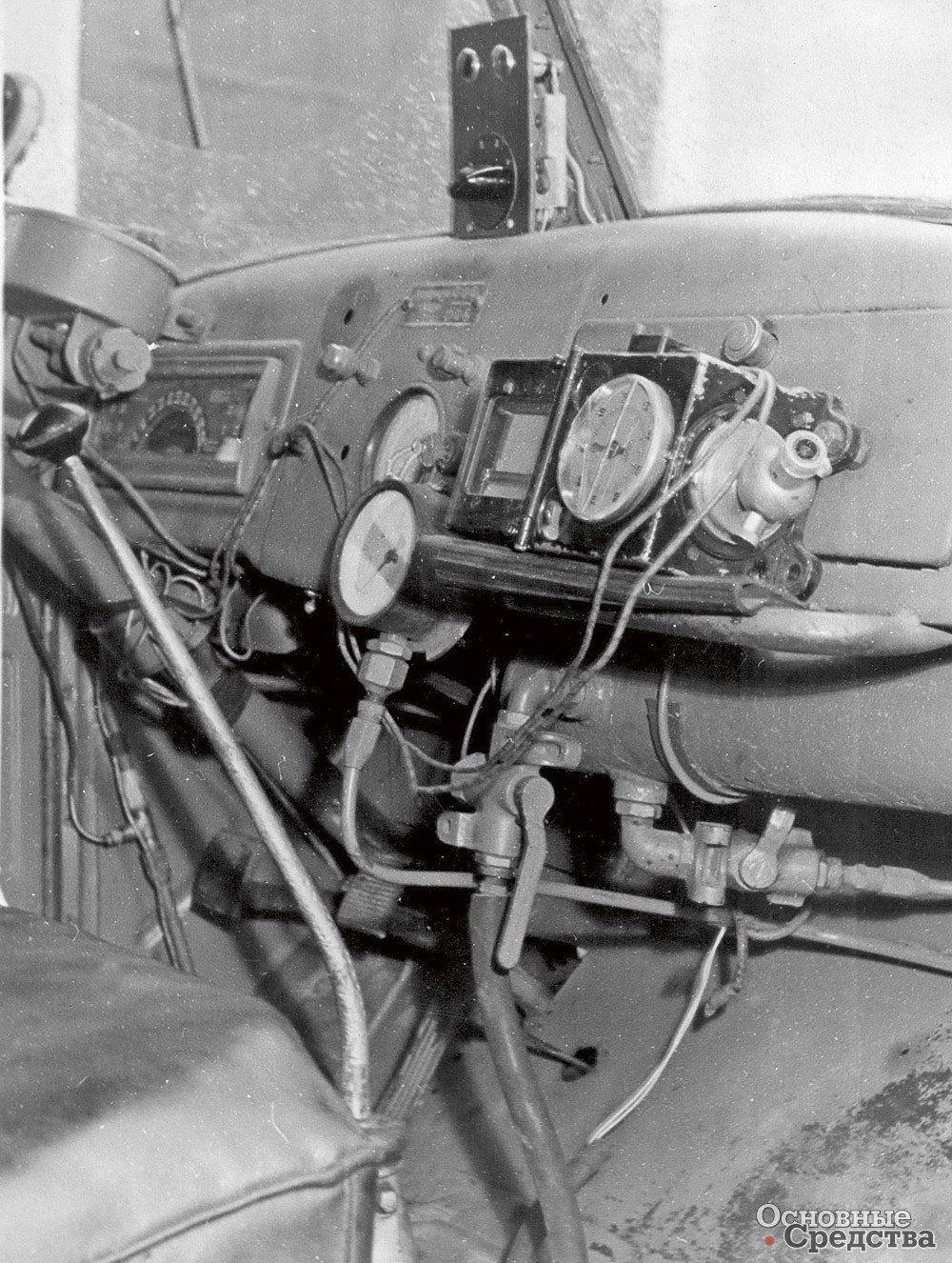
На основании результатов, полученных при стендовых и дорожных испытаниях опытных образцов тормозов с электромагнитным приводом, делались следующие выводы.
- Спроектированный и изготовленный в НАМИ инерционный тормоз с электромагнитным приводом вполне работоспособен, обладает легким управлением и по эффективности может быть использован в качестве колесного тормоза для колес с нагрузкой в 1500–1800 кг на колесо. В частности, тормоз с двумя заклиниваемыми колодками развивает тормозной момент 500–550 кгм при токе в 3 А.
- Электромагнитная муфта тормоза при токе в 3 А имеет приводной момент 30–32 кгм. При испытаниях электромагнитной муфты в водной среде ее нормальная работа не нарушалась, имело место лишь небольшое снижение величины тормозного момента.
- Тормоз с электромагнитным приводом имеет малое время срабатывания: время нарастания тормозного момента до 80% его максимального значения составляло 0,37 с при напряжении 6 В и 0,27 с при напряжении 12 В.
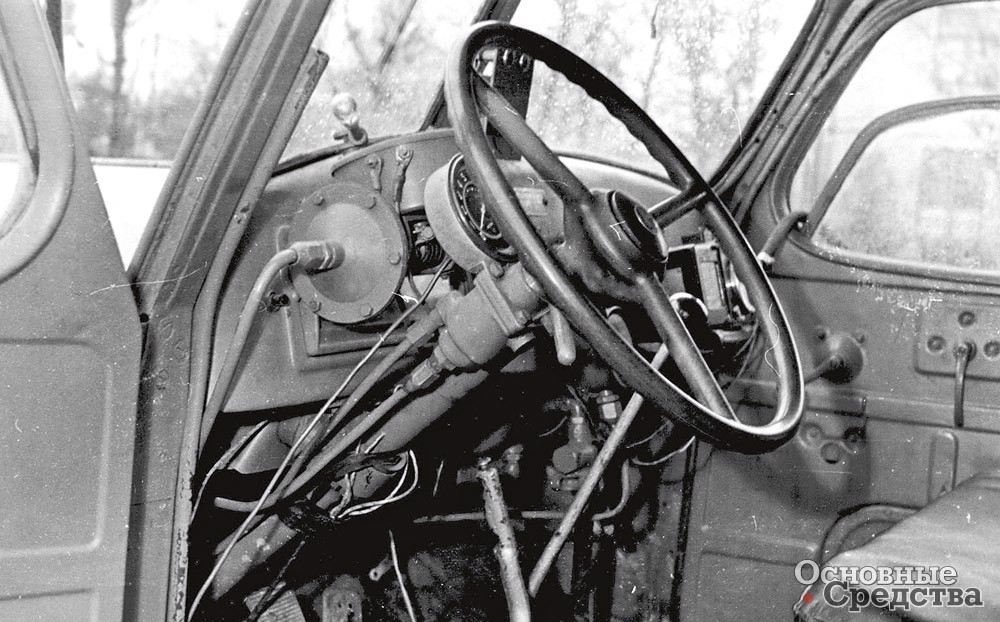
Дальнейшее уменьшение времени срабатывания тормоза при необходимости может быть достигнуто форсированием переходных процессов в цепи обмотки возбуждения электромагнита.
В заключении отчета говорилось: «Инерционные тормоза с электромагнитным приводом могут быть рекомендованы для применения на автомобильных прицепах средней грузоподъемности с использованием питания от стандартной аккумуляторной батареи тягового автомобиля».
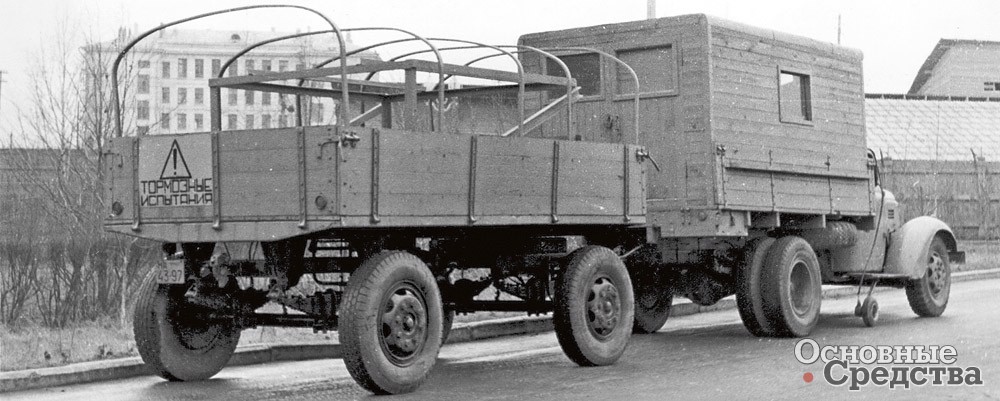