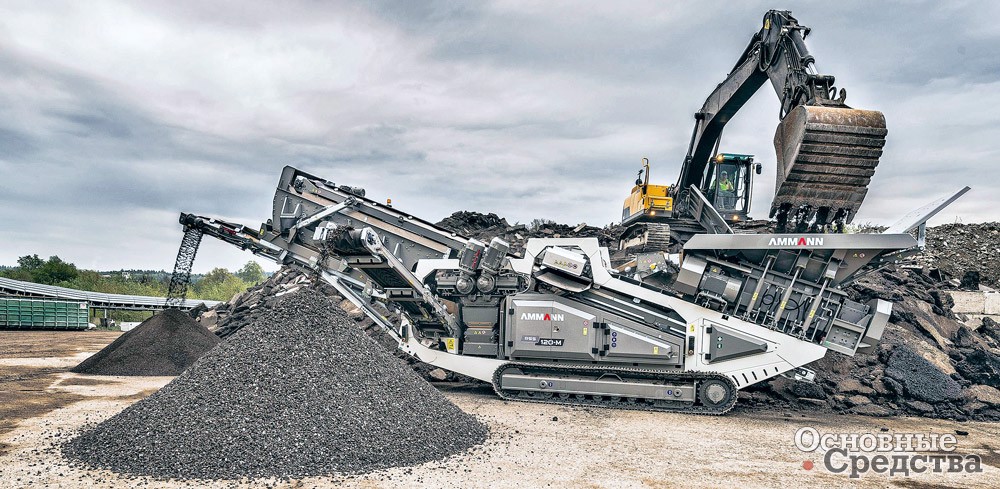
Оборудование для производства асфальтобетонных смесей
Использование вторичного асфальта
Одним из перспективных направлений в дорожном строительстве, которое быстро развивается, является использование гранулята старого асфальтобетона (РАП) в асфальтобетонной смеси, так как за счет него уменьшается потребность в дорогостоящем битуме и каменных материалах. Таким образом, одновременно с сохранением природных ресурсов применение РАП помогает снизить первоначальные затраты на содержание и строительство дорог. Применение РАП в России проходит тестовую стадию и регламентируется предварительными национальными стандартами 244–2017 «Дороги автомобильные общего пользования. Переработанный асфальтобетон. Технические условия» и 245–2017 «Дороги автомобильные общего пользования. Переработанный асфальтобетон. Методика выбора битумного вяжущего при применении переработанного асфальтобетона в асфальтобетонных смесях».
На первом этапе при реализации технологии РАП разработчики стремились достичь максимального использования вторичного материала. Сейчас кроме этого учитывается общий расход энергии для производства асфальта, а также растущие требования контролирующих органов в отношении вредных выбросов.
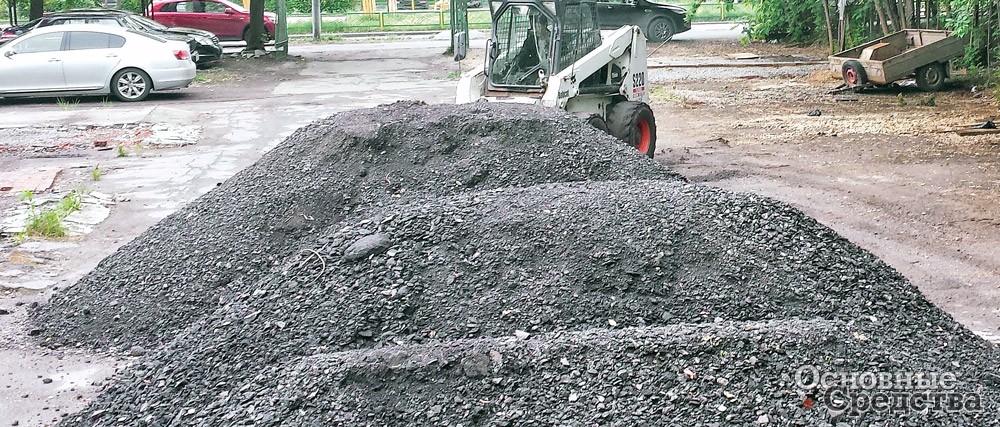
Для демонтажа старого покрытия обычно применяется дорожная фреза или ударно-отбойный инструмент. Чтобы использовать разнородный по размерам и составу вторичный материал, его необходимо сначала подготовить. Для этой цели лучше всего подойдет специализированная техника, например, дробильно-сортировочная установка Ammann RSS 120-M.
Этот мобильный комплекс на гусеничном шасси включает двухступенчатую дробилку с размером входного проема 1200х900 мм, грохот с двумя ситами и магнитный сепаратор. Медленно вращающиеся фрезы дробилки со сменными ножами обеспечивают щадящее дробление, сохраняют исходные частицы перерабатываемого материала и минимизируют выход мелких фракций. Установку можно подготовить к работе через 30 минут с момента доставки на рабочую площадку. Оператор может использовать дистанционное управление. Максимальная выработка достигает 180 т/ч.
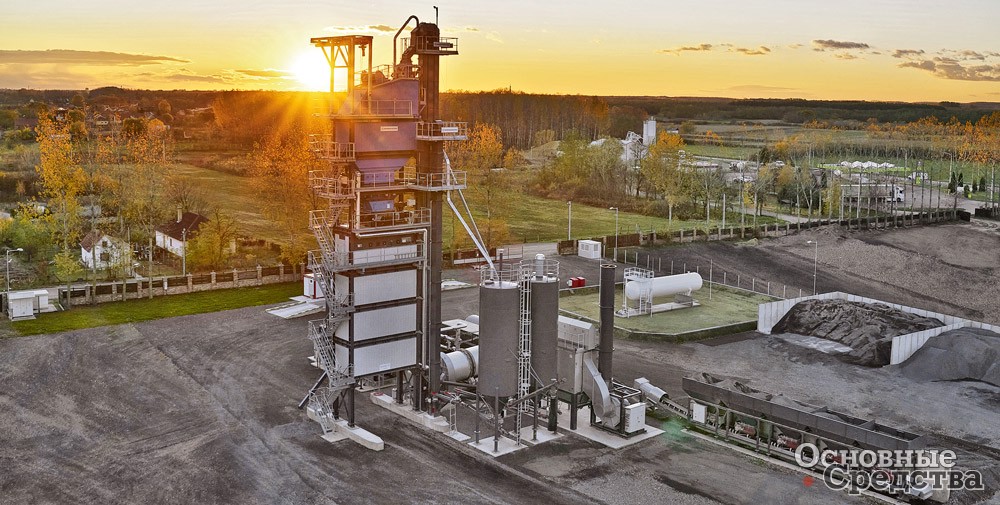
Новые модели асфальтовых заводов
В ответ на новые запросы компания Benninghoven в своих установках TBA модульного типа применяет теперь барабан с генератором горячего газа, работающий по принципу противотока, снижающий уровень вредных выбросов и потребление энергии. При горячем рециклинге задача состоит в том, чтобы нагреть перерабатываемый вторичный материал до оптимальной рабочей температуры 160° так, чтобы уровень выбросов не превысил установленных значений, а содержащийся битум не выгорел. Для достижения такого результата в барабане с генератором горячего газа нагрев происходит не напрямую, а в режиме противотока в отличие от параллельных барабанов. Материал движется в противоположном направлении к источнику нагрева. В зависимости от качества используемого вторичного материала его долю можно довести до 90%. Асфальтобетонный завод Benninghoven TBA производительностью от 160 до 320 т/ч может эксплуатироваться в полумобильном или стационарном виде. Двухвальные смесители на 2, 3 или 4 тонны в составе TBA 2000, 3000 и 4000 обеспечивают производительность смешивания 160, 240 или 320 т/ч. Благодаря размещению главных компонентов в контейнерах и соединениям по принципу «подключи и работай» сокращается время монтажа.
Новые заводы Benninghoven серии ECO могут производить от 100 до 320 т асфальта в час. В них инновационные технологии АБЗ сочетаются c высокими производственными стандартами Benninghoven. Ключевой особенностью заводов ECO является мобильность: компоненты завода вместе с коммуникациями размещаются в отдельных модулях, изготовленных в соответствии со стандартами ISO для контейнеров. Такая конструкция позволяет ввести завод в эксплуатацию всего за пять недель, а также быстро интегрировать новые высокотехнологичные компоненты для оперативного реагирования на потребности клиентов и рынка.
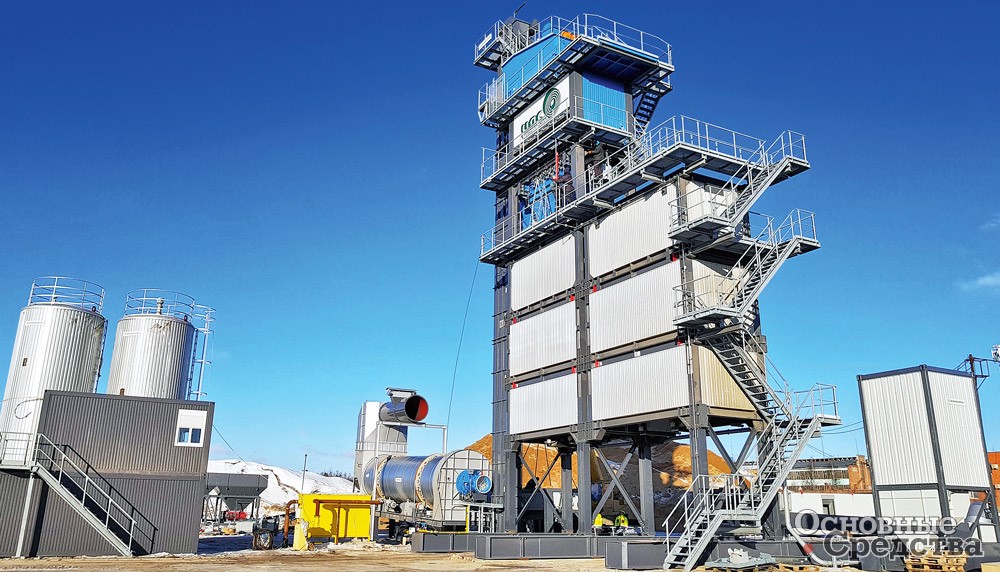
Одним из ключевых достижений компании Astec стало внедрение нового мобильного асфальтового завода Voyager 140, который можно ввести в эксплуатацию в сжатые сроки, а также быстро разобрать для перевозки на новую площадку. Основным рабочим элементом Astec Voyager 140 является барабанный смеситель Astec Double Barrel с V-образными скребками. Voyager 140 производительностью 140 т/ч и долей РАП, достигающей 50%, отличается компактными размерами. Защита окружающей среды обеспечивается рукавным фильтром производительностью 35 800 м3/ч с импульсной очисткой и 260-ю мешками из арамида.
Инновационный продукт от Marini (Fayat Group) был представлен на выставке Bauma 2019 в Мюнхене. Асфальтовый завод Master Tower снижает воздействие на окружающую среду сразу по нескольким параметрам: благодаря использованию переработанного асфальта, уменьшению выбросов и снижению энергопотребления. Новый завод с двумя сушильными барабанами использует только одну горелку, которая обеспечивает подачу достаточного количества тепла благодаря системе циркуляции горячего воздуха. Оба сушильных барабана располагаются над смесителем для предотвращения слипания материала. Гранулят старого асфальтобетона выходит из барабана с температурой 160°, позволяя оператору производить смесь с любым процентным содержанием РАП без риска перегрева первичного материала, сохраняя энергию и качество битума, содержащегося в РАП.
Кроме того, компания Marini дополнила свой ассортимент асфальтобетонных заводов четырьмя новыми супермобильными моделями: Xpress 1500, 1500P с максимальной производительностью 120 т/ч, загрузкой смесителя 1,5 т, горелками мощностью 7 и 9 МВт и Xpress 2000 и 2000P с максимальной производительностью 160 т/ч загрузкой смесителя 2 т, горелками мощностью 9 и 13,4 МВт.
Ранее в этой серии была представлена единственная модель Xpress 2500 производительностью до 200 т/ч. Все модели Xpress легко транспортируются и монтируются за один день благодаря гидравлической системе подъема. Ширина в транспортном положении составляет 3 м, длина – 21 м, вес полуприцепа – 40 т. При необходимости может быть добавлена простая система для РАП, позволяющая использовать до 25% вторичного материала при подаче через кольцо сушильного барабана, 30% РАП при подаче в смеситель. В то же время, используя комбинированную загрузку, можно использовать до 40% РАП. Другие опции включают производство теплой смеси, а также дополнительный набор для вспененного битума.

Отдельные системы хранения
С помощью новой дополнительной системы хранения от Astec можно расширить зону деятельности асфальтового завода. Компактные размеры такой силосной системы позволяют установить ее на небольшом участке, где размещение завода целиком невозможно. Набор компонентов вспомогательной силосной системы хранения состоит из разгрузочного бункера для выгрузки самосвалов, наклонного скребкового конвейера, силосов для долговременного хранения с антисегрегационными дозаторами, поперечного конвейера, из которого смесь подается в выбранный силос, и средств управления.
Американская фирма Asphalt Drum Mixers предлагает самомонтирующиеся бункеры объемом от 30 до 75 т. Готовая смесь доставляется в бункеры с помощью конвейеров. Бункеры ADM изготавливаются из высокопрочной стали с применением двухсторонней сварки. Пневматический дозатор с двойным грейферным затвором снижает риск сегрегации смеси. Покрытие из стекловолокна обеспечивает усиленную теплоизоляцию для поддержания температуры на необходимом уровне до момента выгрузки и формирования равномерного потока асфальта. Заказчики могут выбрать дополнительную масляную или электрическую систему подогрева конуса. Система аварийного оповещения о высоком или низком уровне смеси позволяет избежать переполнения или перегрева бункера.
Системы фильтрации
Рукавные фильтры Ammann способны снизить содержание твердых частиц в отработавших газах до значений ниже 10 мг/Н.м3. Фильтры Ammann обеспечивают максимальную эффективность, создавая минимальный перепад давления при потерях тепла. Рукавные фильтры Ammann различного размера могут быть оптимизированы исходя из отношения объемного расхода газа к рабочей поверхности рукавов по требованию клиента. Рукавные фильтры Ammatex рассчитаны на работу при высоких температурах и устраняют необходимость в использовании воздушной заслонки приточного воздуха. Полимерное покрытие PTFE и качественные швы придают конструкции высокую устойчивость к нагрузкам и продлевают срок ее службы. Стабильность формы рукавных фильтров Ammann обеспечивается термофиксацией.
Marini разработала и успешно применила новую систему фильтрации паров и маслянистых выбросов AeroFILTER. Масляные пары возвращаются в нижнюю часть бункера и выводятся через специальные емкости без какой-либо утечки наружу. Воздух, смешанный с загрязненными парами, проходит через камеру сгорания, где остаточные вредные вещества устраняются.
Система очистки асфальтосмесительных установок TELTOMAT на базе тканевых фильтров поддерживает уровень пыли ниже 10 мг/м3. В качестве фильтрующего материала используется иглопробивной войлок различной плотности с высокой степенью очистки. Фильтры TELTOMAT выдерживают рабочую температуру до 130 °С, а некоторые материалы и до 200 °C.
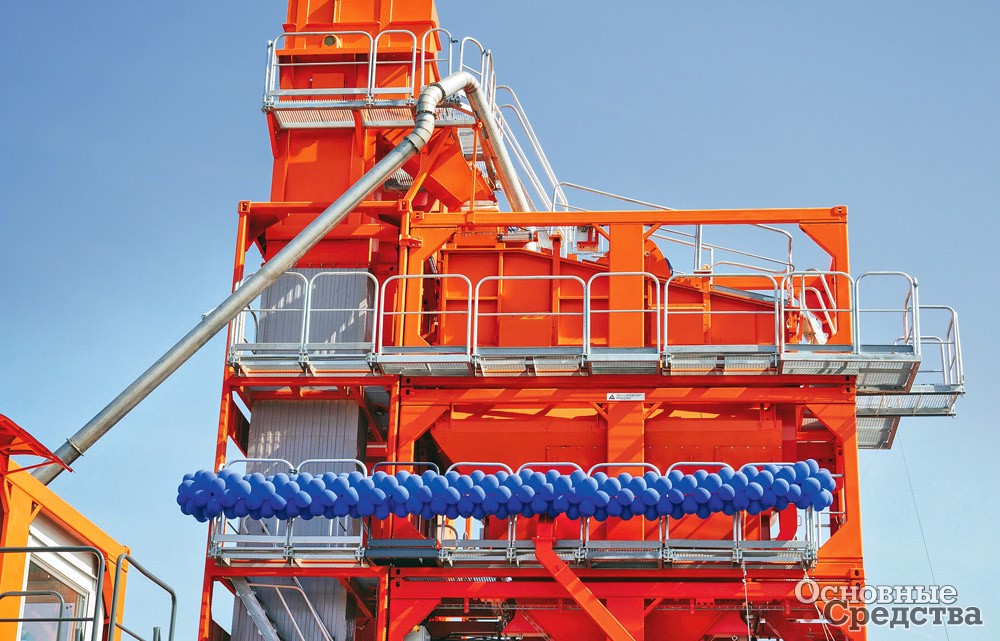
Отечественное производство
В прошлом году в России было произведено более 48 млн т асфальтобетонных смесей, что сопоставимо с объемами 2017 г. Для производства асфальта используется в основном импортное оборудование. Наибольшим спросом пользуются мобильные установки. Производителей АБЗ в России немного, а объемы выпускаемой продукции незначительны.
Хорошей новостью стала недавняя презентация в г. Тосно асфальтобетонного завода циклического действия ДС-1600 мощностью 128 т/ч, который можно транспортировать так же легко, как и обычные контейнеры. ДС-1600 разработан группой компаний в составе «Коминвест-АКМТ», ТоМез и Amomatic Oy. Реализация проекта по запуску в серийное производство нового завода для нужд дорожной и строительной отраслей России оказалось возможной благодаря финансовой поддержке Минпромторга России, который пошел на компенсацию части затрат на проведение НИОКР в рамках государственной программы Российской Федерации «Развитие промышленности и повышение ее конкурентоспособности».
АБЗ ДС-1600 позволяет изготавливать все основные виды асфальтобетона, щебеночно-мастичного асфальтобетона, литого асфальтобетона для автомобильных дорог и аэродромов. К 2021 г. планируется довести объемы выпуска до 20 установок в год. При успешной реализации намеченных планов новый продукт в перспективе может занять до 20% российского рынка АБЗ.
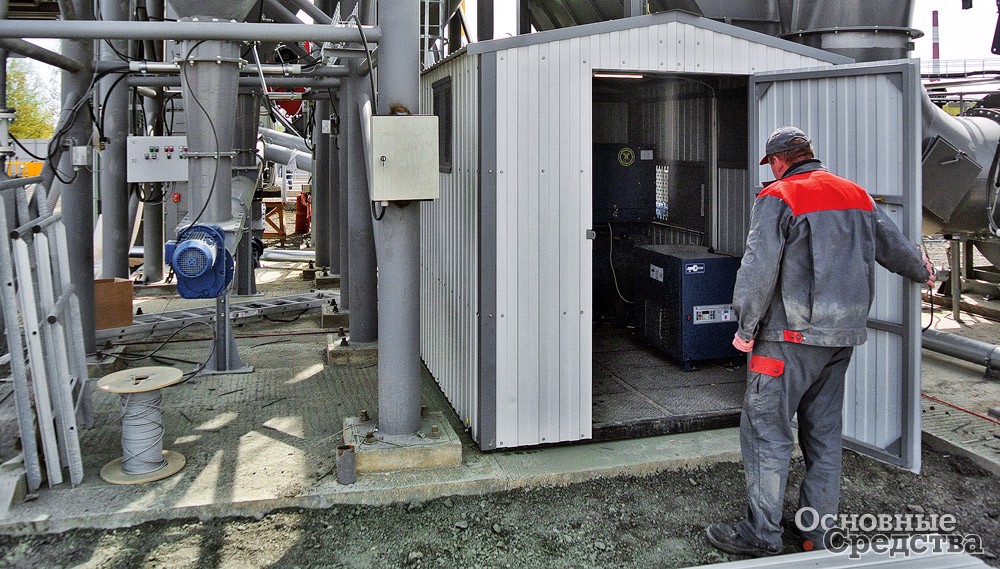
Для нормальной работы АБЗ требуется его обеспечение сжатым воздухом, электроэнергией, водой и паром. Сжатый воздух расходуется прежде всего на распыление топлива у форсунок, для пневматической транспортировки минерального порошка, питания пневматических инструментов и обеспечения работы автоматической системы управления. Компрессорная станция для асфальтобетонного завода проектируется индивидуально, исходя из требуемой производительности и потребности в сжатом воздухе. Расход сжатого воздуха рассчитывается исходя из расхода топлива, количества форсунок, рабочей скорости и диаметра трубопроводов пневмотранспорта, количества пневмоинструмента и расхода воздуха на него. Бежецкий завод «АСО» производит для АБЗ винтовые компрессоры с мощностью привода 11 и 15 кВт. Эти модели поставляются в унифицированном корпусе. Каждая модель может быть настроена на четыре варианта давления: 8/ 10/ 13/ 16 атмосфер. Наибольшим спросом пользуется компрессор мощностью 11 кВт, рассчитанный на давление 10 атм. Помимо поставки отдельных компрессоров Бежецкий завод «АСО» предлагает решения «под ключ». В этом случае компрессор комплектуется системой подготовки (осушки и фильтрации) сжатого воздуха и монтируется в контейнерном блоке (КБ-10). Заказчику остается только подключить свою пневмомагистраль к компрессорной станции.
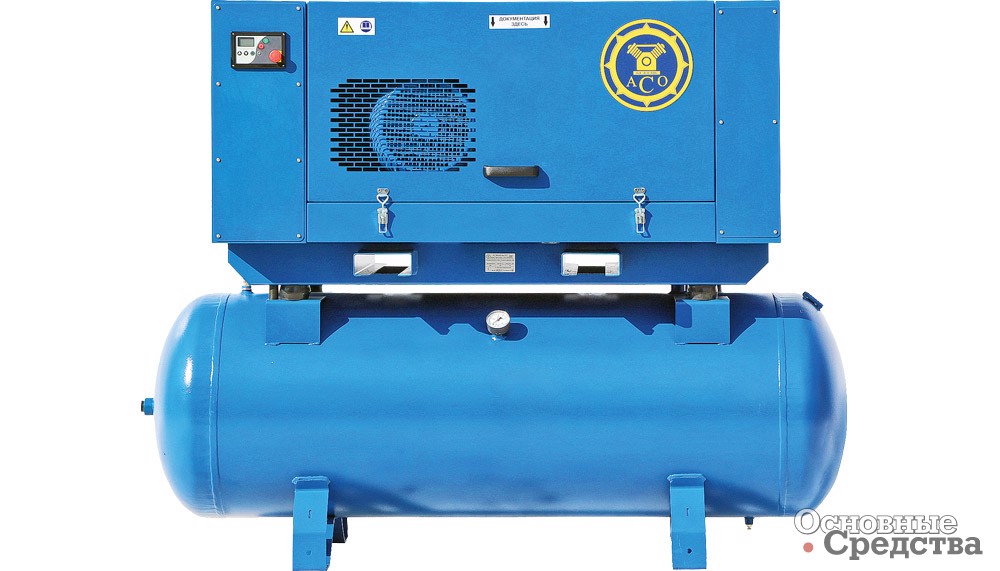