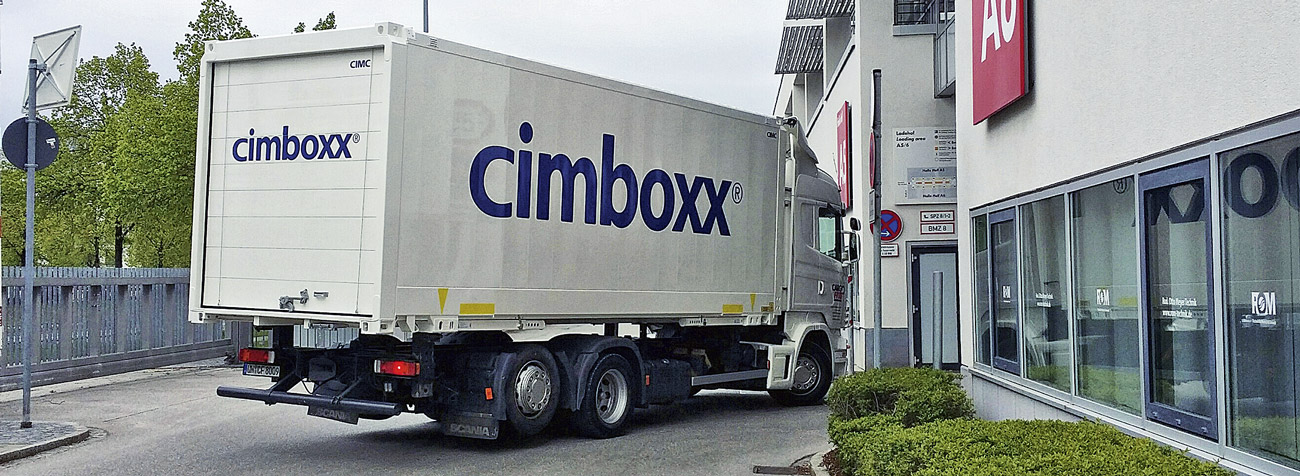
Завод полуприцепов DongGuan CIMC
Завод построен на окраине города Дунгуань, что расположен в дельте Жемчужной реки на север от Гонконга. Рядом находятся такие промышленные центры Китая, как Шэньчжень и Гуанчжоу. Для удобства в компании принято обозначение завода аббревиатурой DCVC по первым буквам DongGuan CIMC Vehicle Co., Ltd. Аналогичным образом называют завод в Шэньчжене: SCVC – Shenzhen CIMC Vehicle Co. Ltd.
Строительные работы начали в сентябре 2015 г., завершили в апреле 2016 г. К монтажу оборудования приступили в декабре 2015 г., в июне 2016-го запустили производство. Численность персонала 320 человек – очень мало для машиностроительного предприятия такого масштаба: 300 человек заняты непосредственно на производстве и 20 – административный персонал. На европейском, американском или российском предприятии с таким объемом выпуска работали бы 2000 человек.
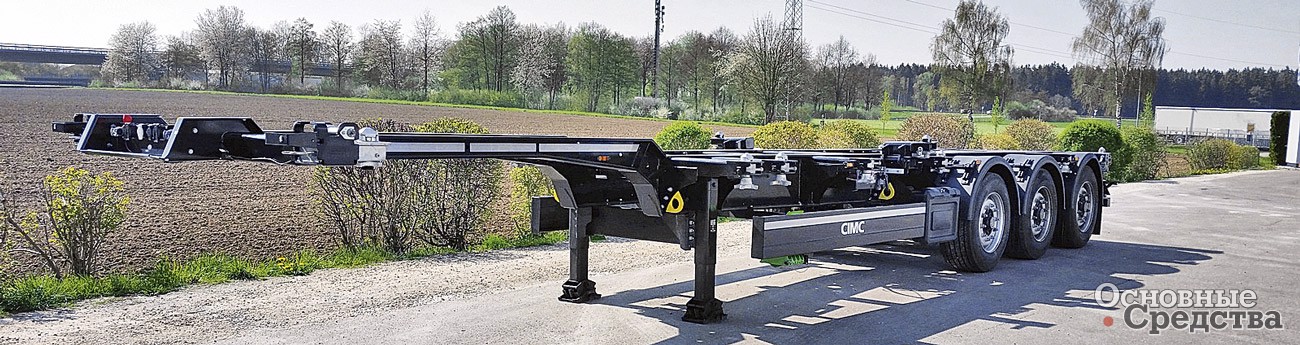
Общая территория завода DCVC охватывает 180 тыс. м2, из них под крышей 72 тыс. м2. Свободная территория отведена под стоянку готовой продукции. Завод выпускает широкий спектр контейнеровозов для североамериканского рынка, а для европейских стран – шторные полуприцепы, сменные кузова и контейнеровозы. Сегодня, работая в две смены, завод производит по 60 единиц продукции в смену. Большой тираж достигнут как благодаря передовым технологиям, так и за счет ограниченной номенклатуры изделий – работает эффект масштаба. Предприятие построено по современным промышленным канонам: все связанные технологические циклы под одной крышей. Завод полного цикла: в большом корпусе размещены линии лазерной резки, штамповки, гибки, роботизированной сварки, а также мощная линия финишной обработки, включающая пескоструйную очистку, KTL-обработку и порошковую окраску. На входе – листовой металл, на выходе – готовое изделие. Кроме того, производство крупносерийное, что положительно сказывается на себестоимости и качестве продукции.
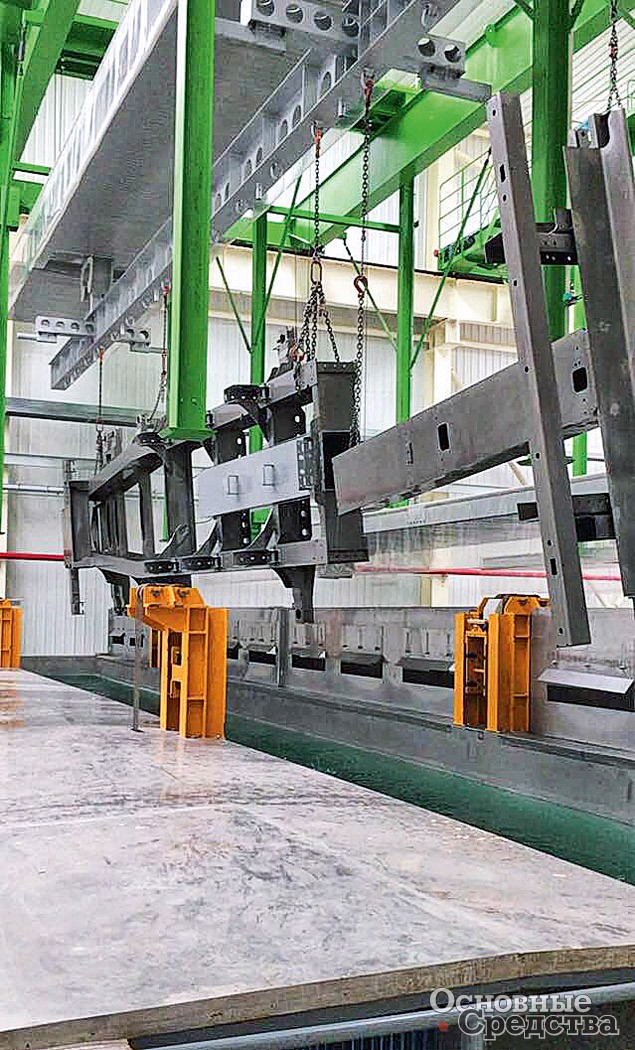
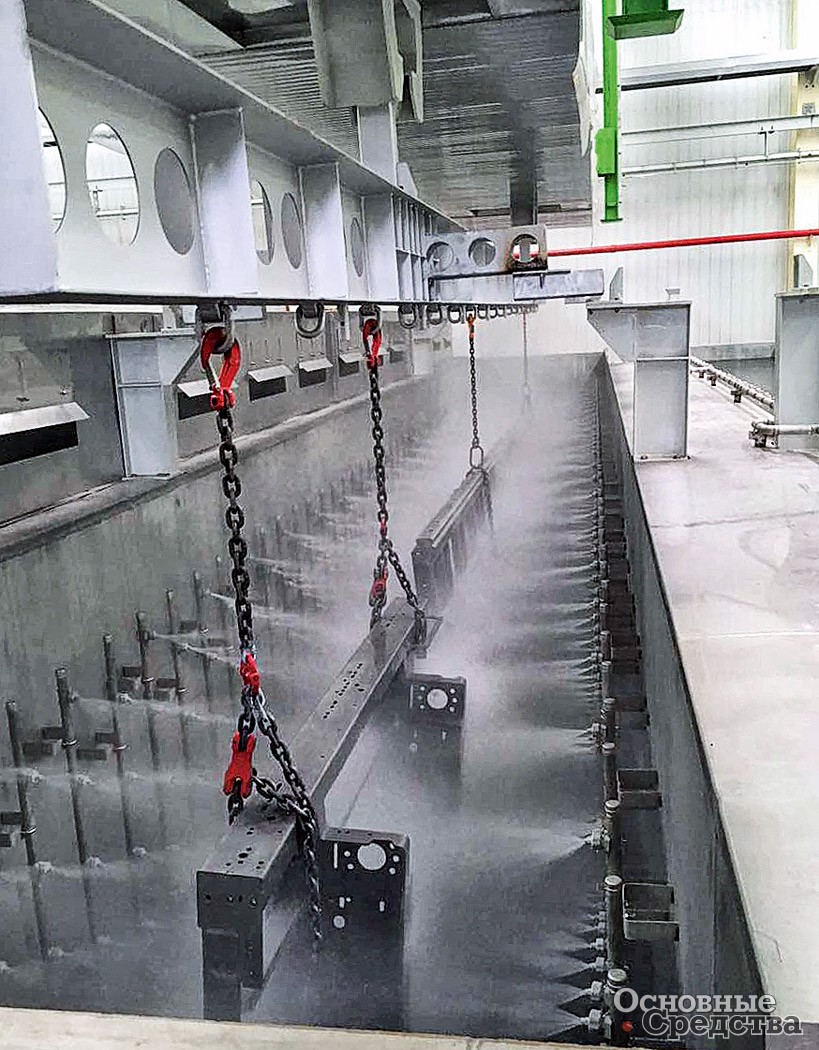
Листовой металл подвозят фурами непосредственно к воротам, сделанным как на складском терминале, и выгружают у линий лазерной резки. Линий лазерной резки две, каждая по 8 машин Fiberblade 3015 фирмы Messer Cutting Systems (США) с общей на линию автоматической системой подачи и возврата фирмы Remmert GmbH (Германия). Что характерно, именно Китай сегодня является основным покупателем прогрессивных производственных систем.
Преимущества лазерной резки – в абсолютной точности и в том, что после нее деталь не нуждается в механической обработке. Лазерный резак снимает фаски под сварку и даже гравирует на детали номер. Ограничение лазерной резки в толщине металла, но на заводе DCVC с толстым металлом не работают, поэтому в каких-либо других видах резки нет необходимости.
После резки детали поступают на линии штамповки и гибки, оснащенные прессами соответствующей мощности и длины. Выштампованные детали перемещаются на линию сборки рам. Рамы вручную собирают, прихватывают в кондукторах, затем роботизированная сварка обваривает все окончательно и с высочайшим качеством. Линия роботизированной сварки построена на базе современных промышленных манипуляторов и кантователей и насчитывает более 40 роботов. После сварки выборочно проводится дефектоскопия швов ультразвуком.
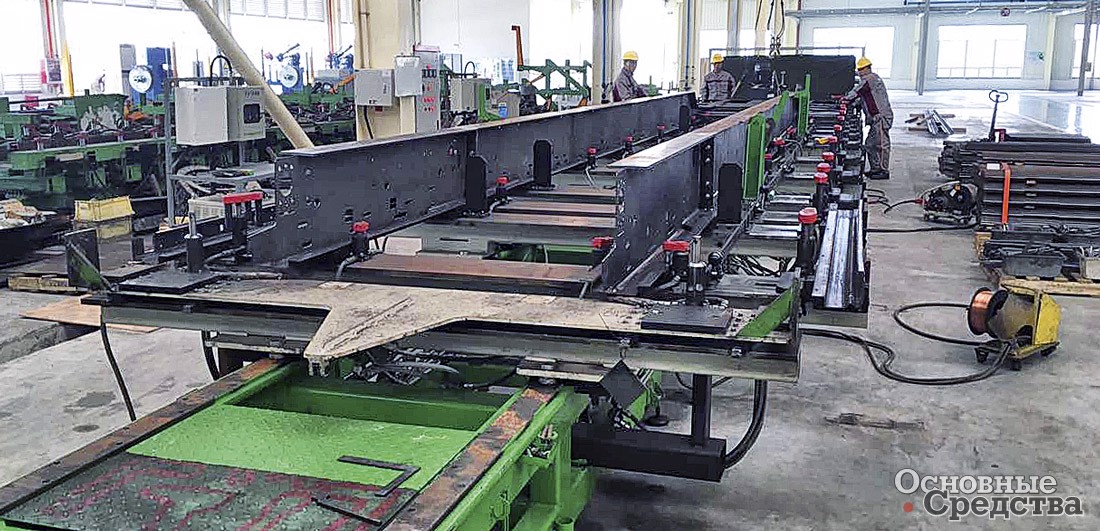
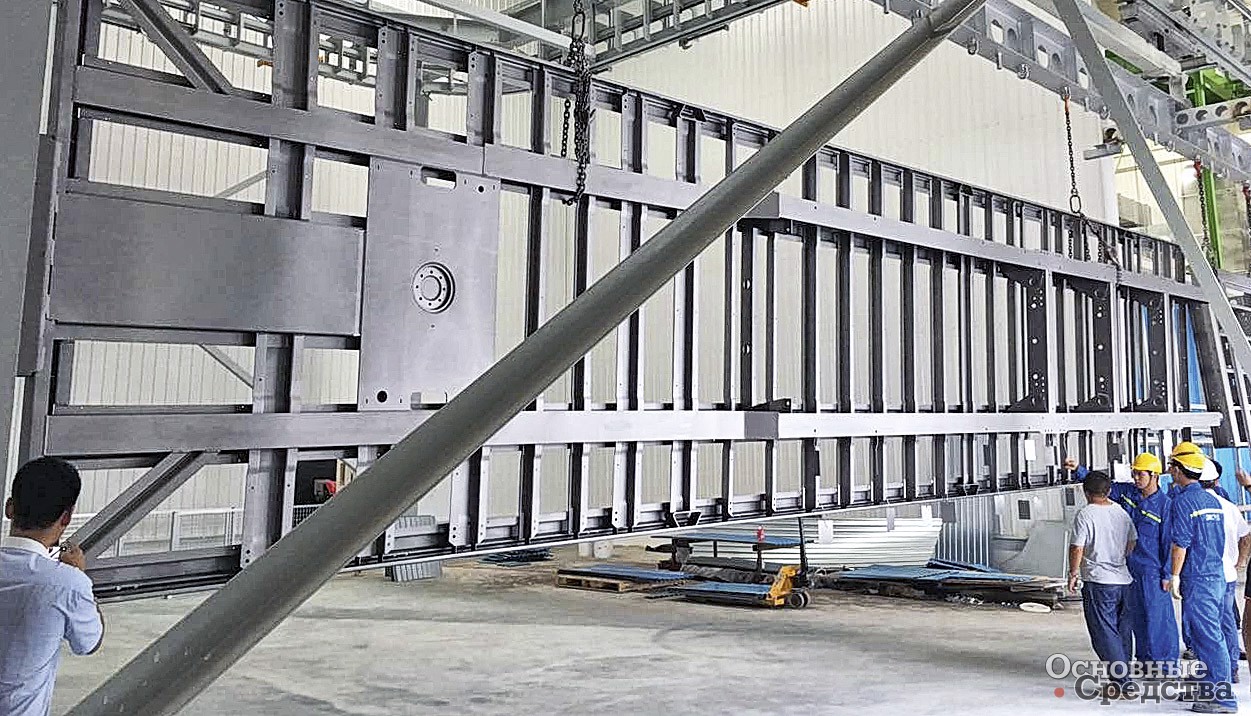
Стоит заметить, что Китай – самый крупный потребитель промышленных роботов и по темпам роботизации опережает другие развитые страны.
Сваренное изделие поступает на следующую линию, выполненную по последнему слову техники, – линию финишной обработки, включающую пескоструйную очистку, линию KTL-катафореза и роботизированную окраску. Линия KTL-катафореза состоит из 15 ванн размером 16300х2650х1100 мм, что позволяет обрабатывать 16-метровые рамы. Линия KTL-обработки движется с тактом 6,5–8 минут.
KTL-обработка обеспечивает коррозионную защиту изделия фактически на весь срок ее эксплуатации. Слой KTL-грунта надежно удерживается на поверхности за счет диффузии граничных слоев грунта и металла. Благодаря диффузии на обработанной поверхности никогда не возникает пучинистой коррозии, и небольшие повреждения – царапины, потертости – не повлекут образования участка коррозии.
После KTL-обработки рамы окрашивают порошковой краской в роботизированной камере. Краска не содержит летучих органических соединений и безопасна для окружающей среды. Производственный цикл полностью замкнут, а роботизированная окраска обеспечивает почти 100%-ную утилизацию краски.
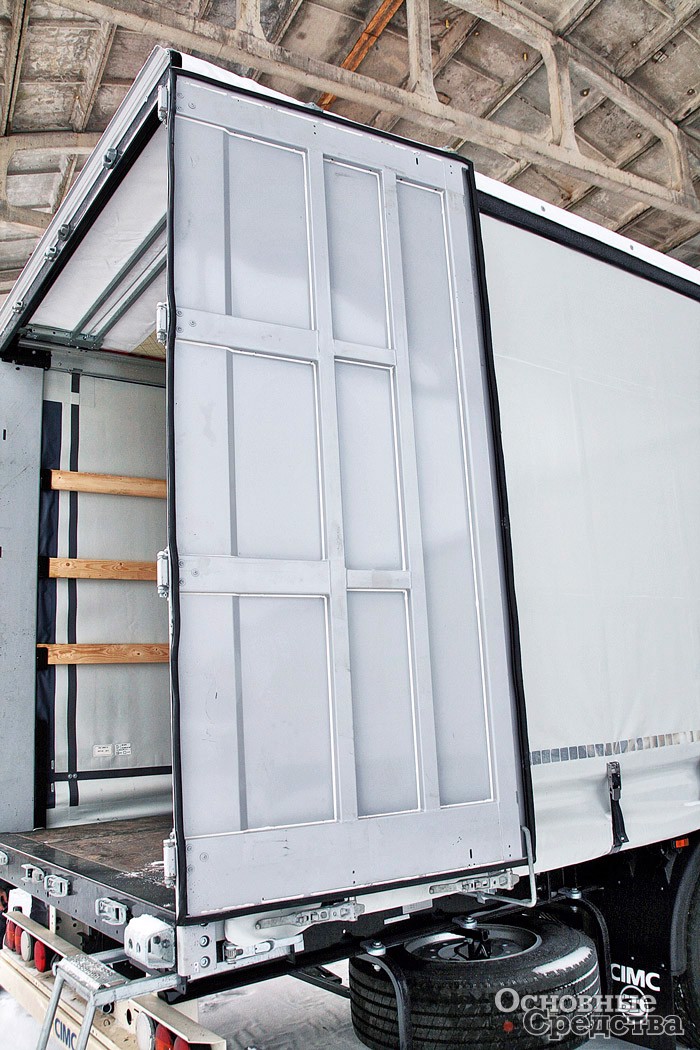
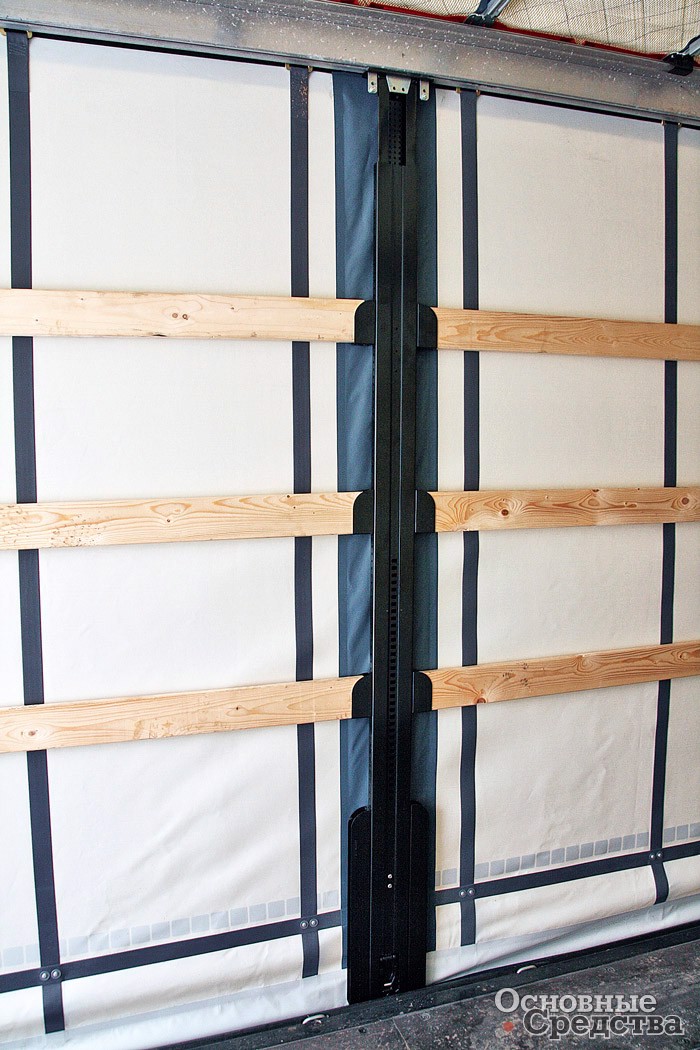
Окрашенные таким образом рамы перемещают на сборочную линию, где полуприцепы собирают до степени готовности к отправке. Полуприцепы перевозят в так называемых «китах», то есть стопкой по три штуки. В пункте назначения подразделения или партнеры компании CIMC выполняют окончательную сборку и предпродажную подготовку изделия. В России эти функции выполняет дочерняя компания OOO «СИМС Трейлер РУС».
В CIMC не собираются останавливаться на достигнутом и намерены нарастить мощность участков лазерной резки и штамповки, смонтировать и запустить сборочную линию и склад, а также перенести производство шторных полуприцепов и специальных шасси для американского рынка на площадку SCVC в 120 км от завода в Дунгуане.
Таким образом, компания CIMC располагает мощным производственным потенциалом для наращивания своего присутствия на европейском и российском рынках и вытеснения обосновавшихся там именитых производителей с историей.
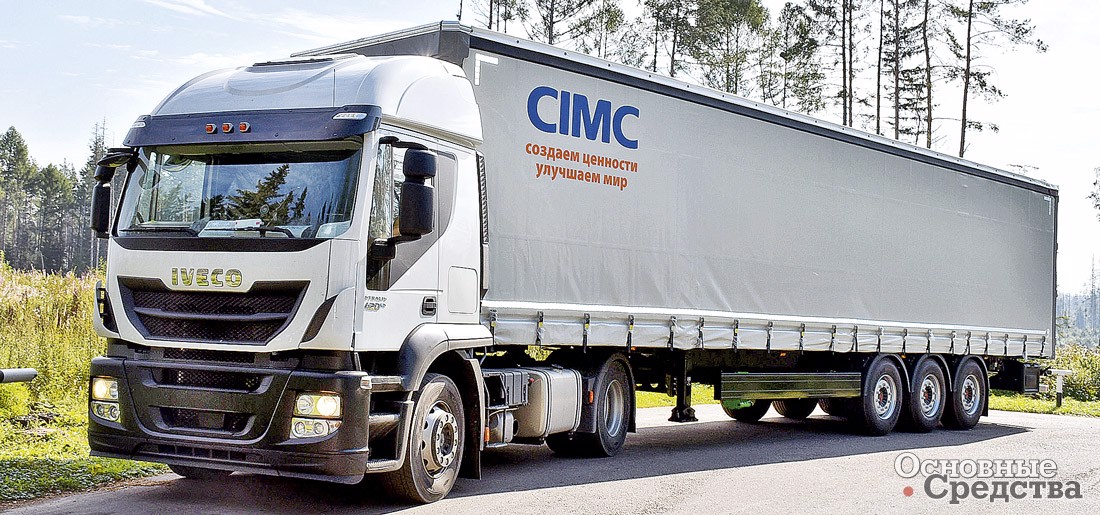