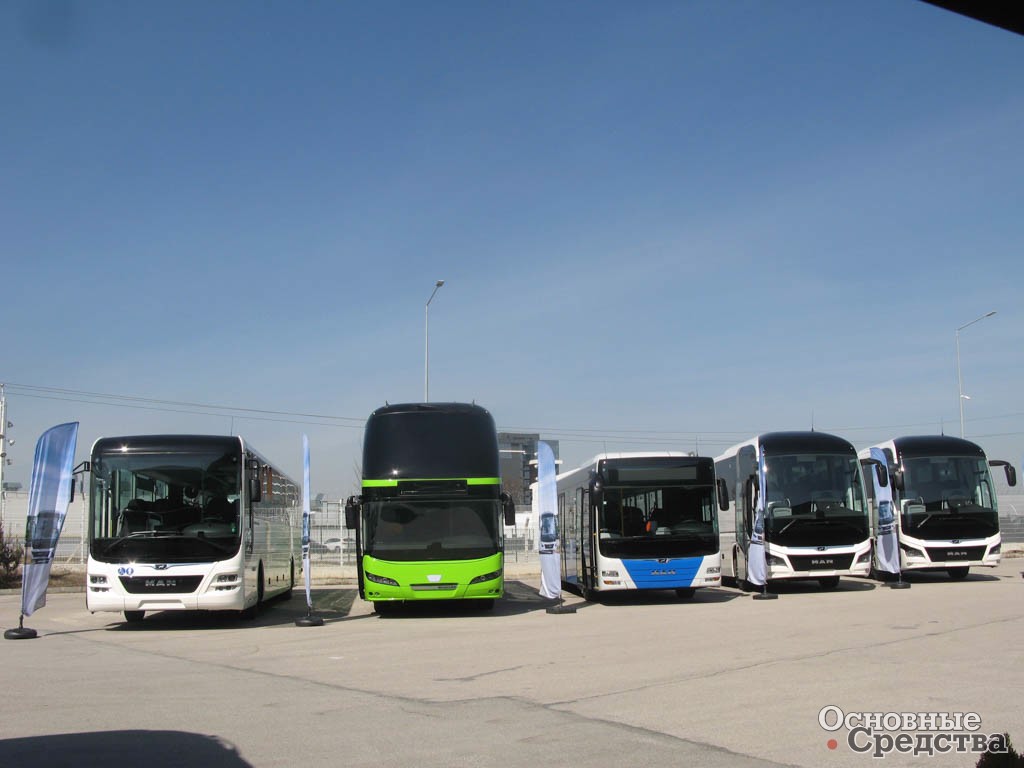
Визит на завод автобусов MAN в Анкаре
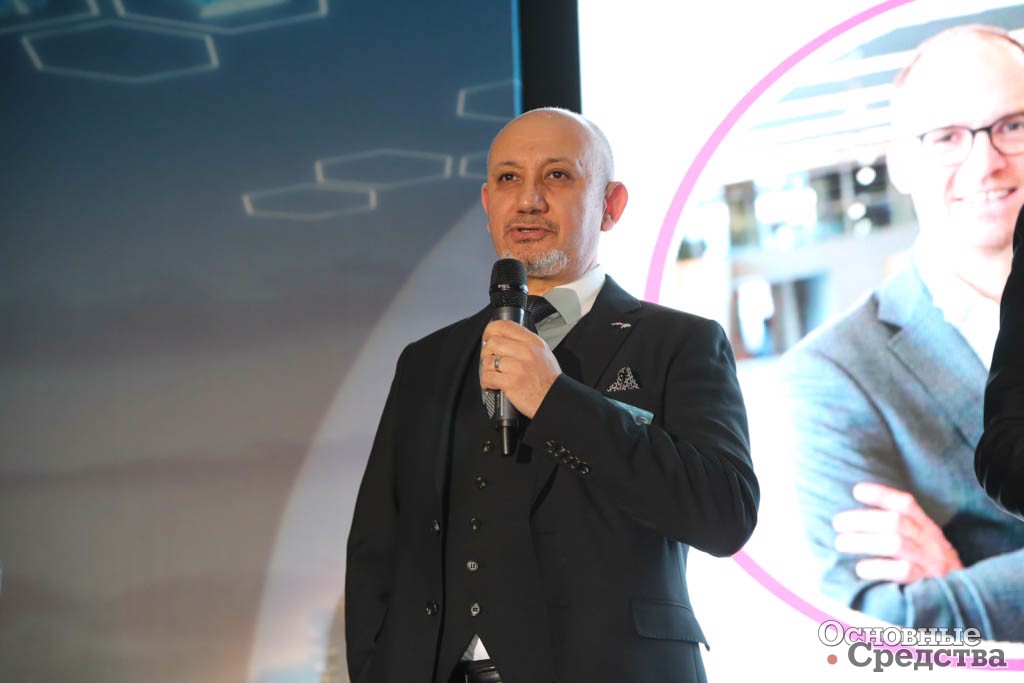
Краткая история предприятия
Турция по праву гордится темпами развития своей автомобильной промышленности. Еще в 2002 году общий выпуск легковых, грузовых автомобилей и автобусов составлял всего 357000 ед. В 2017 году был достигнут исторический максимум — 1696000 ед., а в 2019 году произвели 1462000 ед.
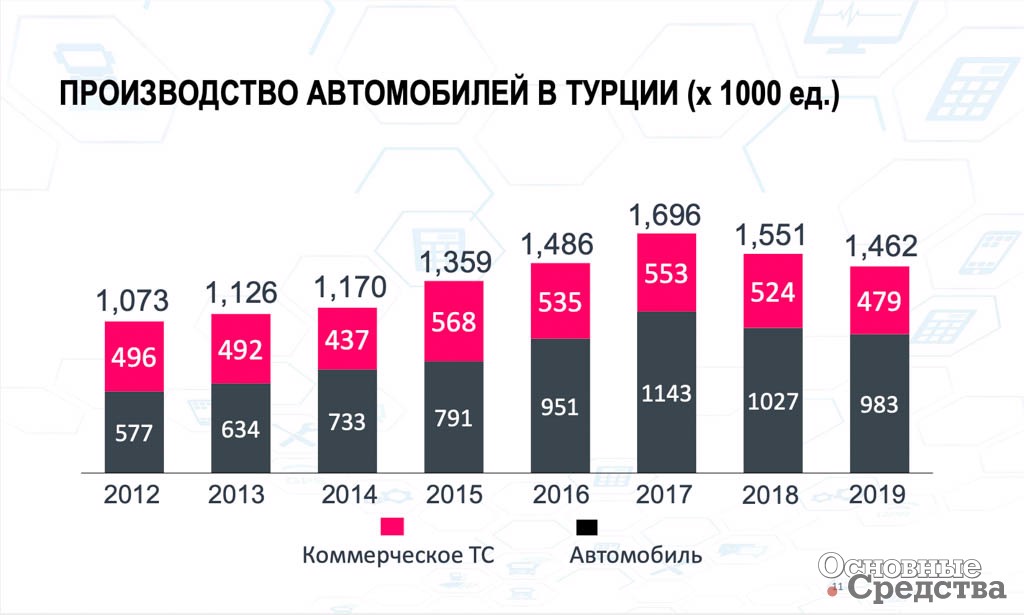
Завод по производству грузовиков компании MAN Türkiye A.Ş, 100-процентной «дочки» MAN Truck & Bus AG, был основан в 1966 году и первоначально располагался в Стамбуле.
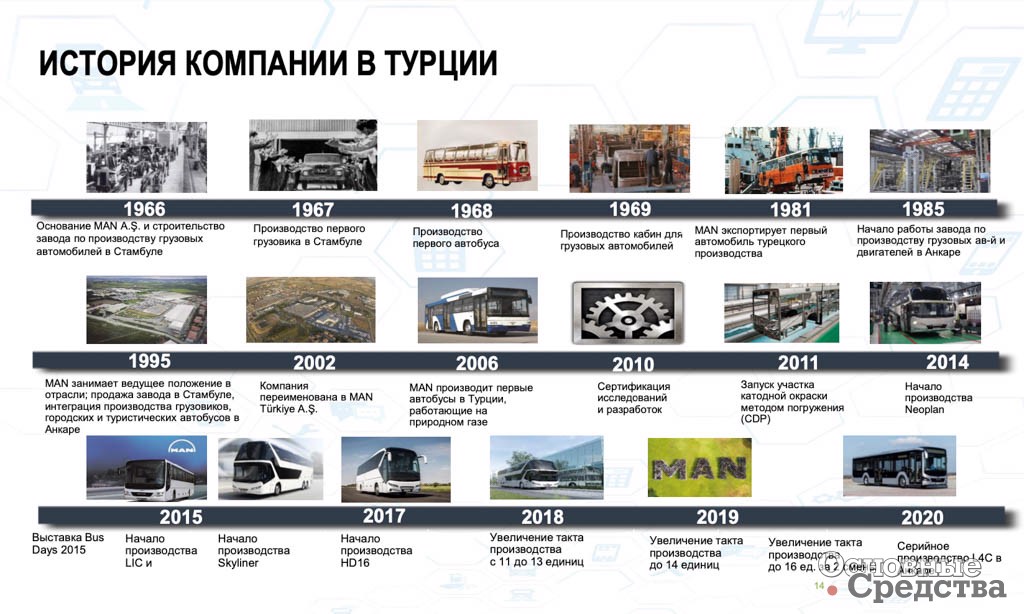
С 1968 г. на предприятии стали также производить автобусы.
В 1985 г. производственные мощности были переведены в Анкару.
С 2006 г. завод начал производить первые в Турции автобусы, работающие на природном газе.
В 2011 г. введен в строй участок антикоррозионного катодного покрытия KTL методом погружения.
С 2015 г. автобусы марки NEOPLAN разных моделей производятся только на заводе в Анкаре.
В настоящее время производственные площади предприятия составляют 317202 м2, завод выпускает только автобусы различных типов и моделей: городские L4C и Lion's City, туристические Lion's Coach и Tourliner, междугородные Lion's Intercity, двухэтажные Skyliner и автобусы премиум-класса Cityliner
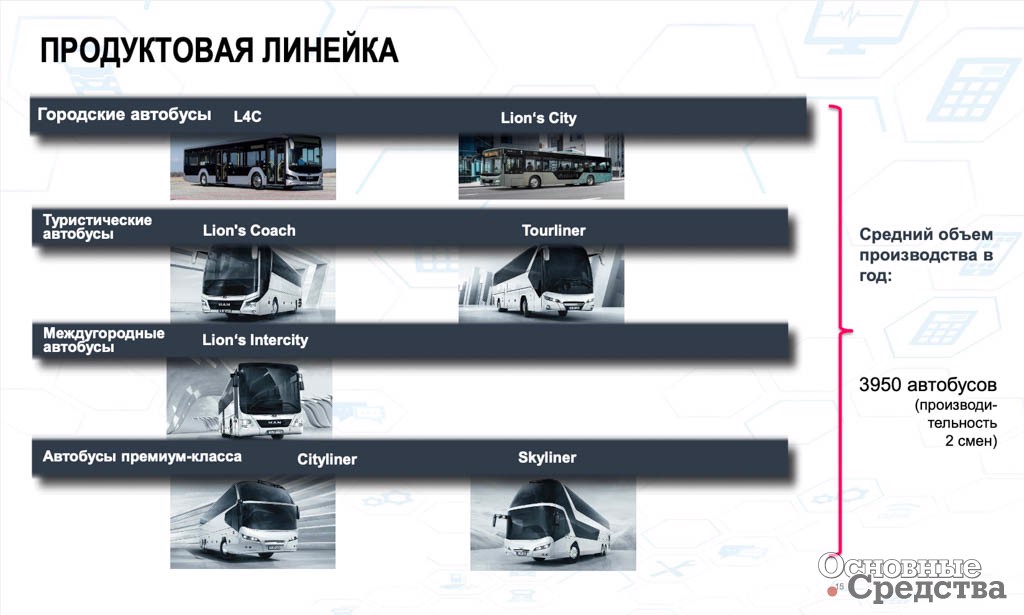
Темп производства достиг 16 автобусов за двухсменный рабочий день, годовой выпуск составляет около 4000 автобусов разных моделей. Это крупнейший в мире автобусный завод MAN.
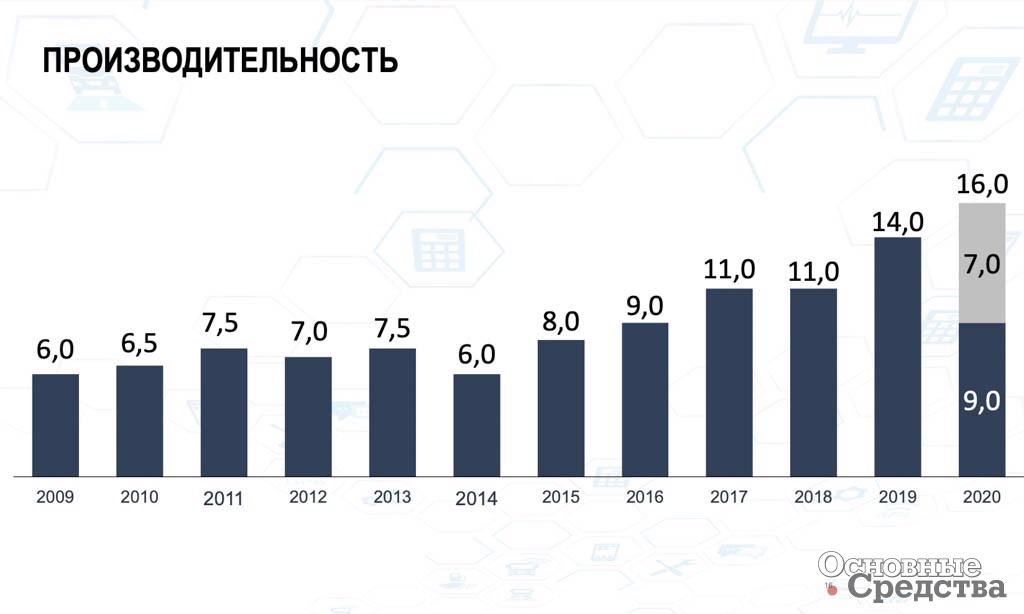
По плану численность работников на заводе в 2020 г. достигнет 3384 чел.
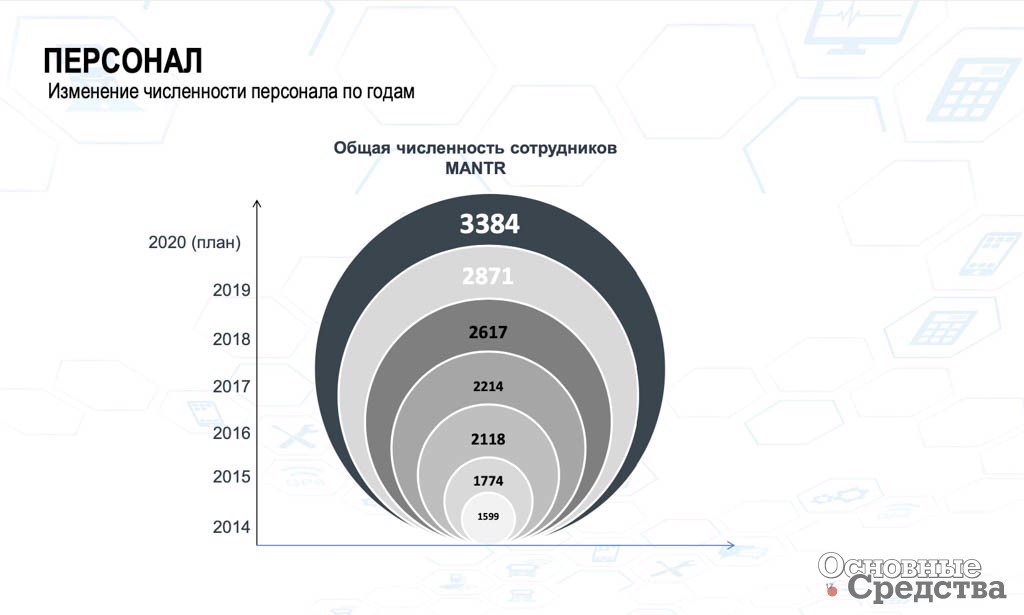
В структуре персонала существенную часть (59%) составляет офисные сотрудники за счет большого количества специалистов, ведущих конструкторско-исследовательские работы по созданию и совершенствованию автобусов. Центр исследований и разработок был открыт при заводе в 2012 г.
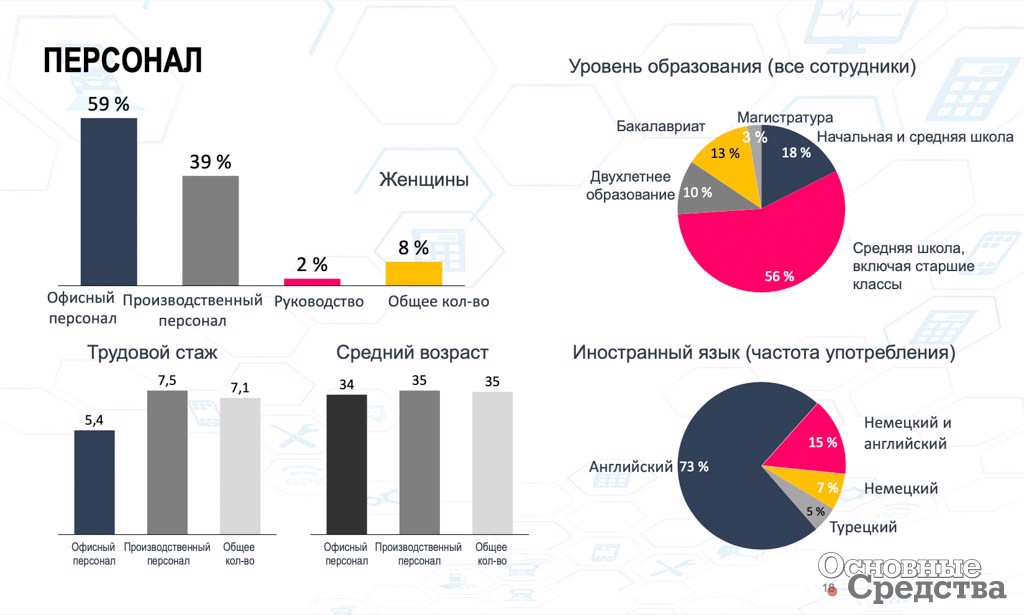
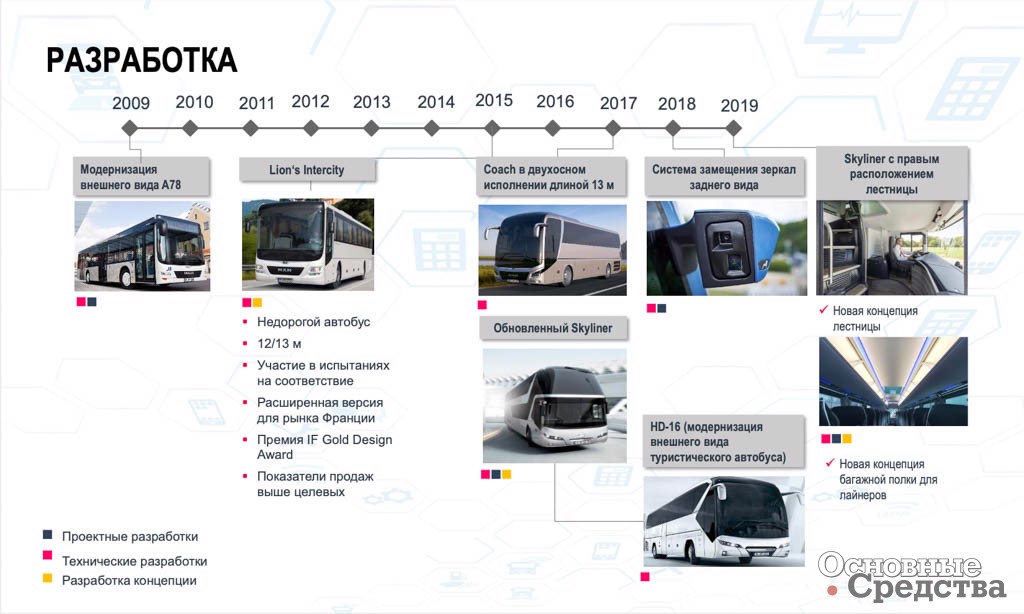
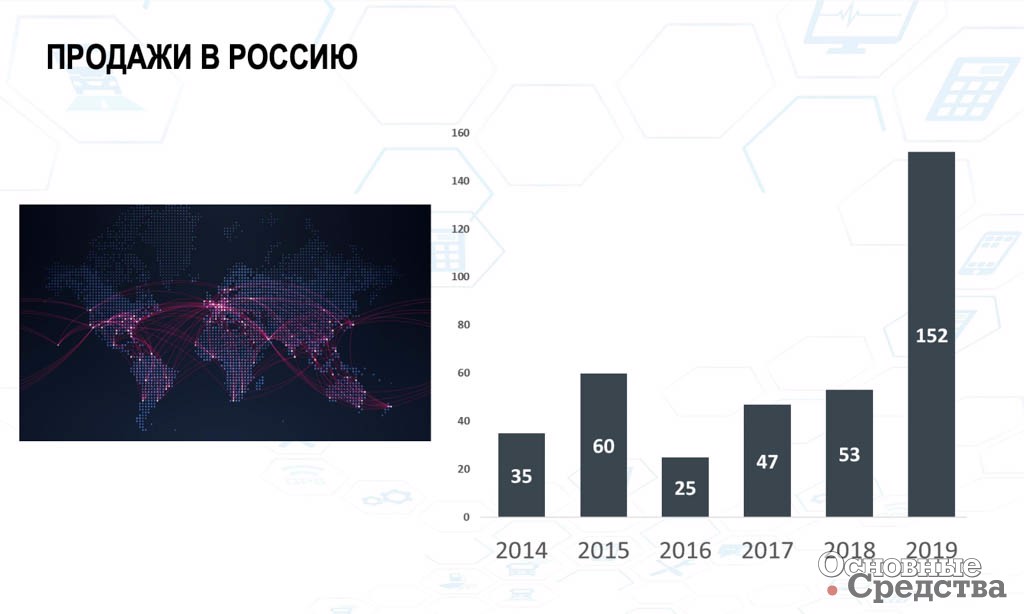
Продукция завода поставляется в десятки стран и в том числе — в Россию. В 2019 г. в нашу страну была поставлена рекордная партия турецких автобусов: 152 ед.!
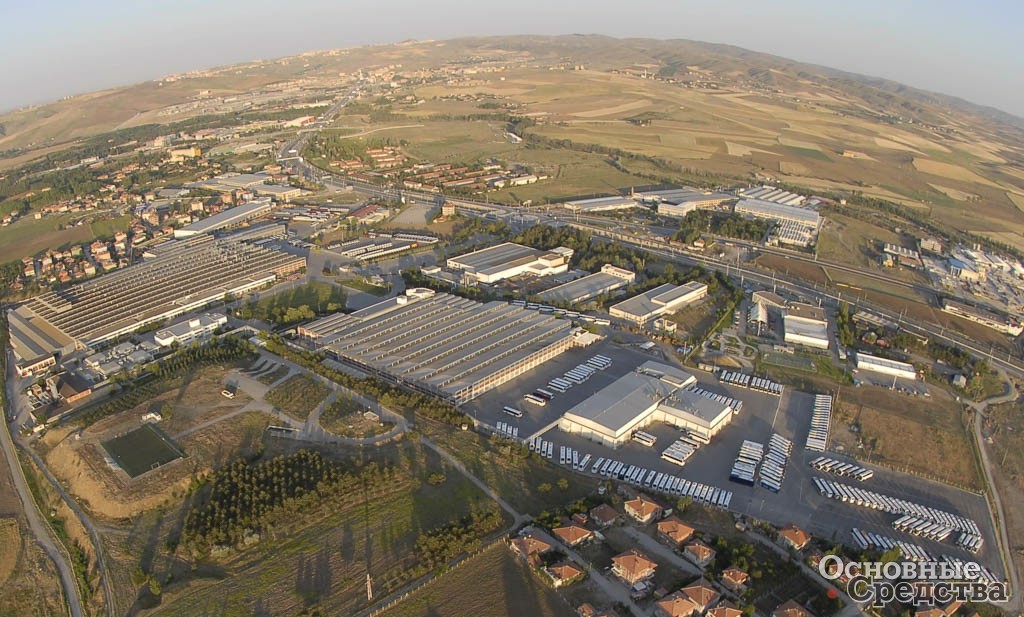
Производство
На заводе реализовано производство полного цикла, от стальных заготовок до готовой продукции. Локализация производства составляет более 60%. Но двигатели, коробки передач и оси поступают из Германии.
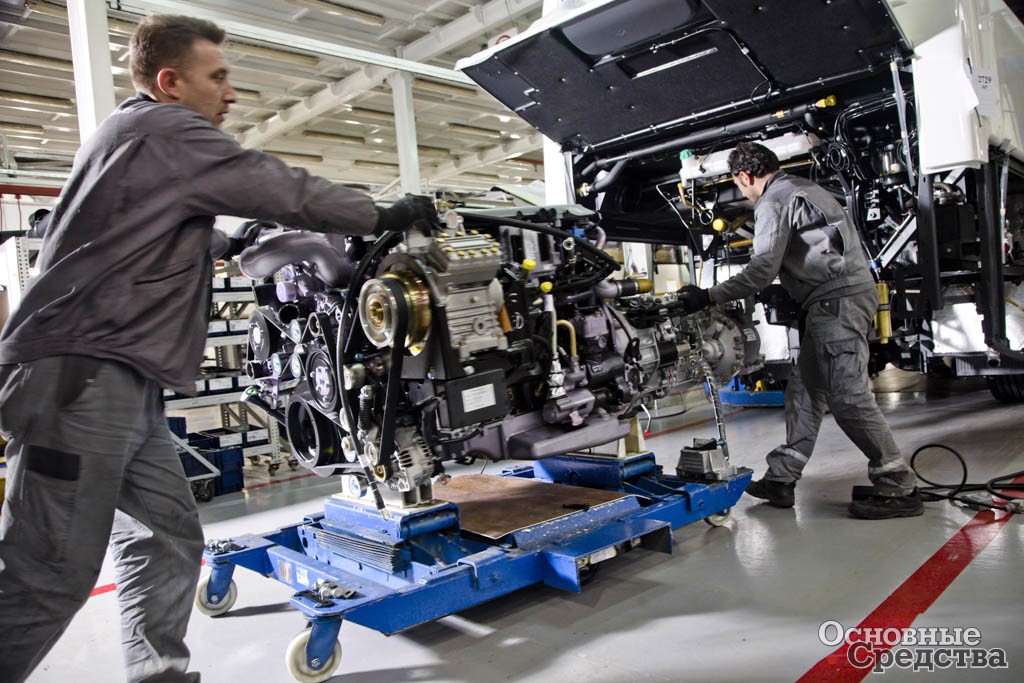
Сварка каркасов автобусов производится вручную на специальных стапелях и в кондукторах, чтобы исключить перекосы. Качество сварочных швов тщательно проверяется. Использование сварочных роботов нецелесообразно, т. к. на производственной линии изготавливаются десятки разных моделей и модификаций и настроить роботы на все варианты исполнения сложно. Однако, руководители предприятия заверили, что работа по автоматизации процессов сварки ведется.
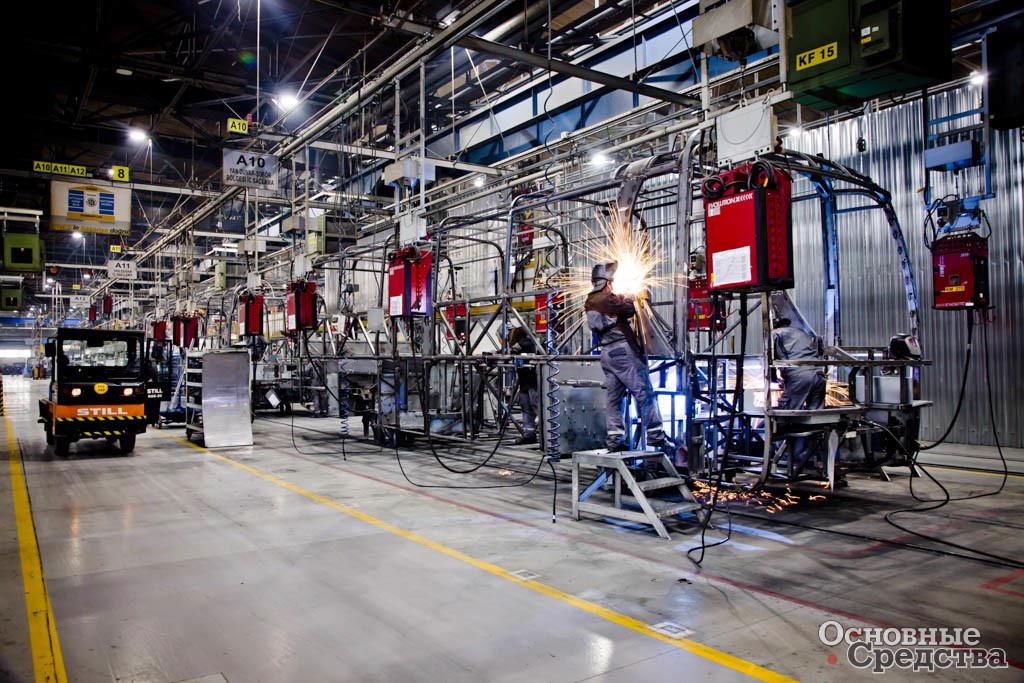
С 2011 года пространственная геометрия готовых каркасов проверяется в измерительной лаборатории лазерной 3D-установкой в 700 точках с точностью до 0,001 мм. Допускается отклонение от номинальных размеров не более 0,05%, что на кузове длиной 12 м составляет всего 6 мм. На сегодняшний день мощности установки хватает на измерение лишь каждого второго каркаса, а половина изделий проверяется традиционными способами измерений.
Проверенные каркасы обшиваются листами крыши, пола и боковой облицовки, а затем отправляются на участок нанесения антикоррозионного KTL-покрытия площадью 10000 м2, состоящий из серии огромных гальванических ванн, в которые помещается весь каркас автобуса.
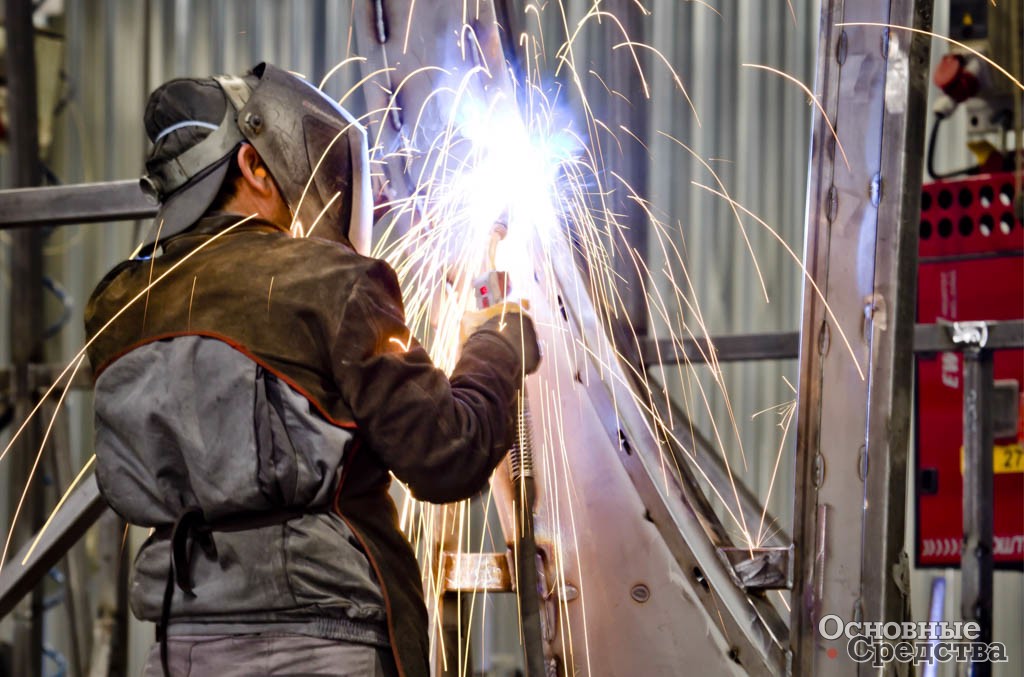
При погружении жидкость попадает не только на наружные, но и на внутренние поверхности квадратных профилей, из которых выполнены каркасы, т. е. антикоррозионная обработка производится не только снаружи, но и изнутри. Выполняется цинкование, а затем грунтование в два слоя. Общая толщина антикоррозионного покрытия составляет 25 мкм. Такая обработка гарантирует защиту от коррозии в течение не менее 10 лет.
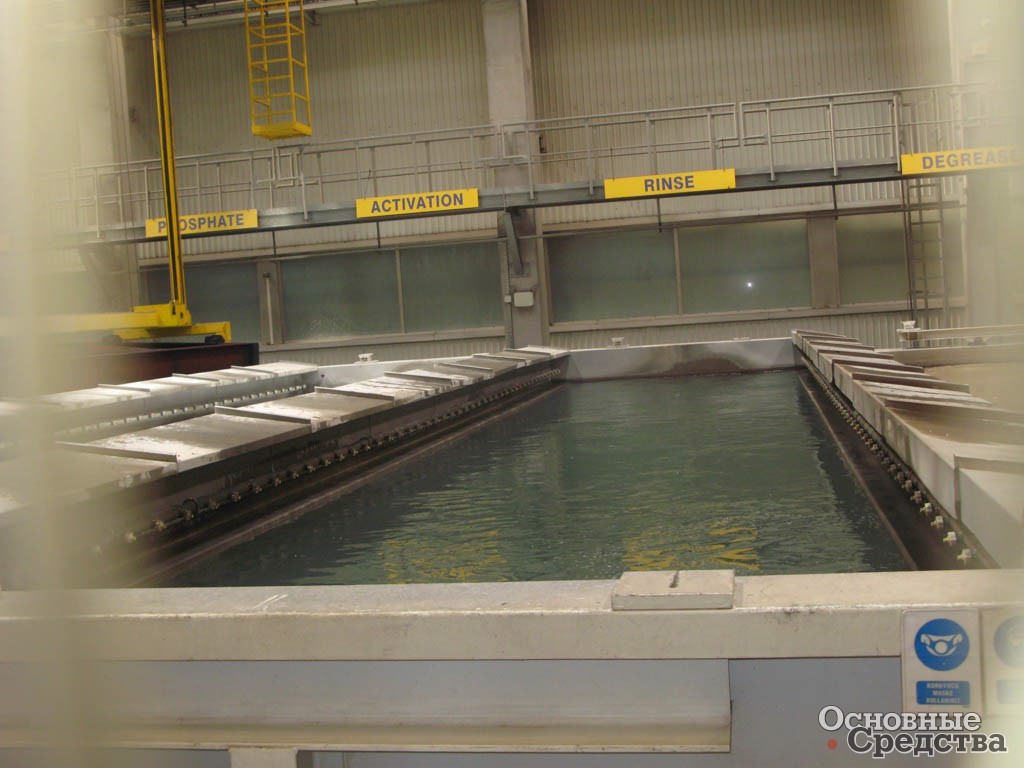
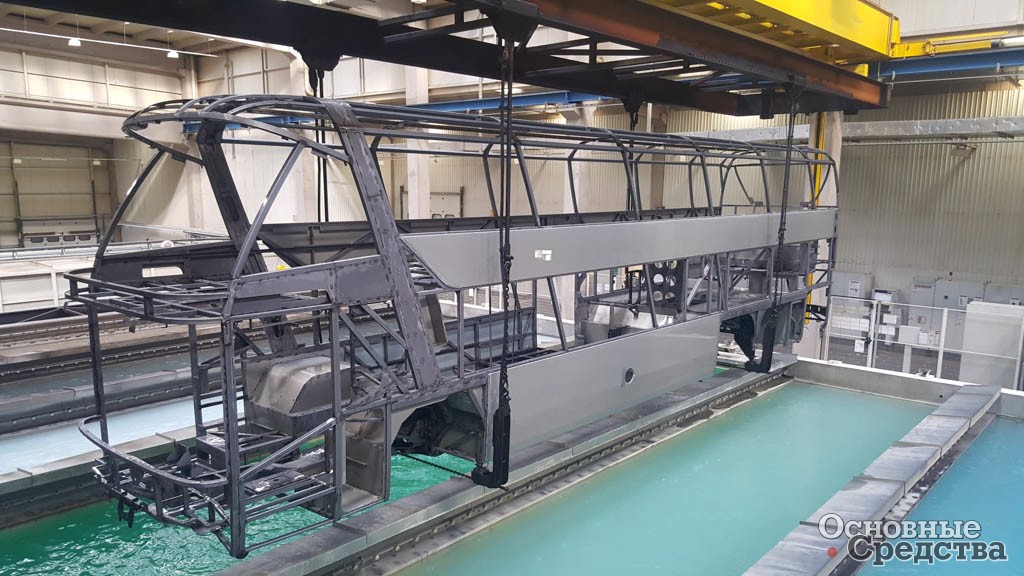
Затем кузов сушится на протяжении часа при температуре 230ºС и направляется на участок герметизации полостей, а затем - в окрасочный комплекс, который был запущен в эксплуатацию в январе 2015 г. Процесс окраски полностью автоматизирован и управляется компьютерами.
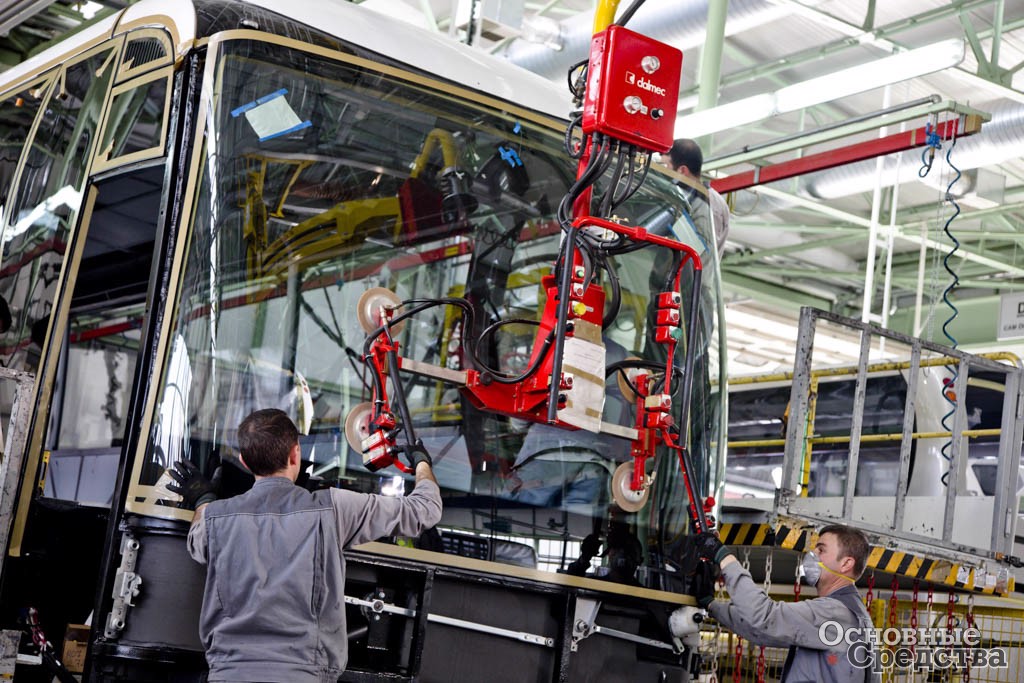
После сборки кузова и шасси все автобусы проходят проверку по многим параметрам: работа двигателя, тормозной системы, герметичность кузова и испытательный пробег на 80 км. Имеется «камера аудита», где установлено мощное освещение и контролеры периодически тщательно осматривают готовые автобусы, оценивая качестве сборки и окраски.
Вот так достигается прославленное качество автобусов NEOPLAN, а восточное происхождение придает им легкий пикантный привкус кофе по-турецки.
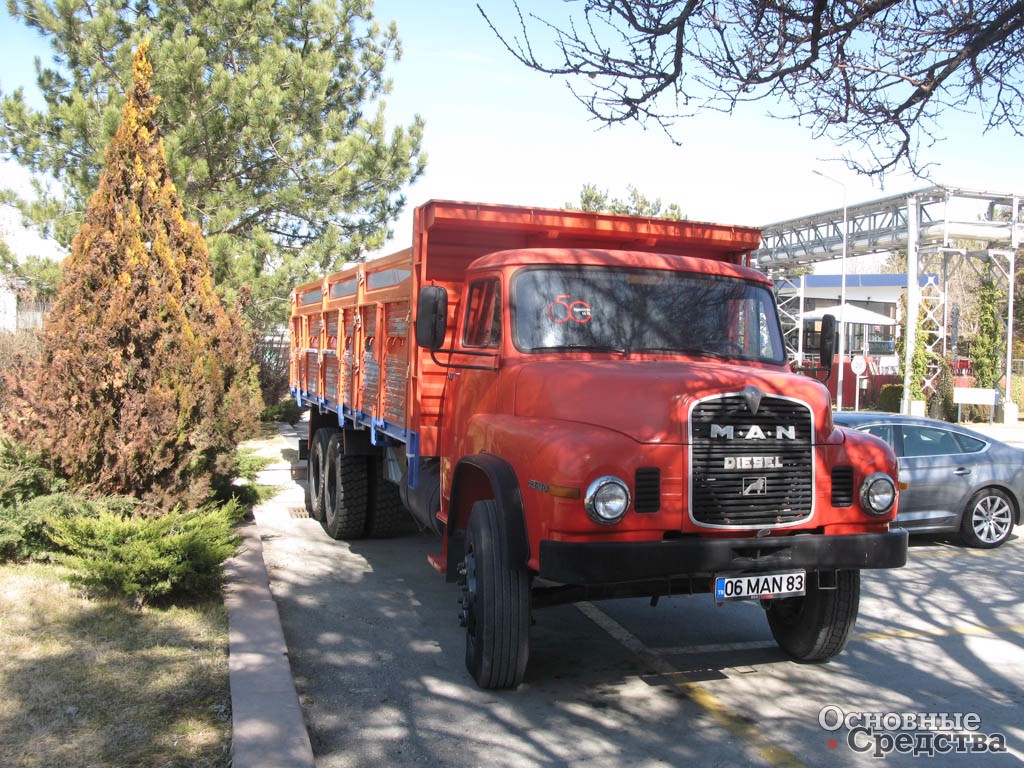